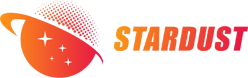
Tungsten with high melting point and high hardness is an important strategic material, which is widely used in tungsten carbide tools, electric lamps, tool steel additives, rockets, spacecraft, nuclear reactors and other fields. With the development of science and technology, new special requirements are constantly being put forward for the raw material tungsten powder, such as ultrafine tungsten powder for high-quality hard alloys; Electronic materials and filter materials require spherical tungsten powder.
Compared with ordinary tungsten powder, spherical tungsten powder has two obvious characteristics. Firstly, the appearance is spherical and the powder has good flowability; The second is high compaction density. Spherical tungsten powder, as a high-tech material used in industries such as thermal spraying, porous materials, and powder metallurgy, has received close attention from domestic and foreign markets and researchers due to its unique preparation process and excellent performance, and has invested a large amount of manpower and resources in research and development. China is a major country in tungsten resources, accounting for two-thirds of the world's tungsten resources. The research and development of high-performance spherical tungsten powder is of great significance for fully leveraging China's tungsten resource advantages and promoting the development of China's material industry.
Preparation method of spherical tungsten powder
1. Arc spray gun method. Using a regular DC arc welding machine in series as the power source, a simple SCDP-3 arc spray gun is used to transmit and control the intersection of two consumable electrode tungsten wires, starting the arc melting and atomizing into spherical tungsten powder with compressed air. Measure the diameter of tungsten wire with a micrometer, and adjust and measure the wire feeding speed, melting current, and voltage between two tungsten wires using the instruments and devices of the arc spray gun itself. The effects of tungsten wire diameter, wire feeding speed, and electrode voltage on working current, powder spraying effect, and powder quality were studied. The spherical tungsten powder prepared by this method has a wide particle size distribution. Coarse powder can be used to manufacture filters, while fine powder can be used to manufacture porous tungsten ion generators. At the same time, this method has simple and easy equipment, low cost, but low production efficiency, which is not conducive to industrial production.
2. Microwave single membrane cavity method. Place tungsten powder into a timed glass tube and heat treat it in a single mode sintering furnace under microwave action to spheroidize FW-1 tungsten powder. The results indicate that spheroidization of FW-1 grade tungsten powder can be observed after different times when the microwave power is between 450 and 1000 watts. The particle size of W powder is basically the same, with a large total surface area and a small particle size. It has sufficient input depth for microwaves and heats each other very evenly. With the increase of heating power and temperature, the surface diffusion of tungsten powder becomes stronger, and the spheroidization degree of tungsten powder becomes higher. Therefore, increasing power and prolonging processing time are beneficial for the spheroidization of tungsten powder.
3. Plasma method. The so-called plasma spheroidization technology refers to adding ordinary tungsten powder to the plasma jet, causing the surface (or overall) of tungsten powder particles to melt and form liquid droplets. The molten droplets contract due to surface tension to form a sphere, which is then fixed by rapid cooling to obtain spherical tungsten powder.
4. Vapor deposition method. In the 1960s, foreign countries began to study the preparation of spherical powders of refractory metals and their compounds. In 1963, an American company invented a process for obtaining large-sized spherical tungsten powder from WF6 through vapor deposition. This process involves highly corrosive hydrogen fluoride, with harsh working conditions and high environmental protection requirements.