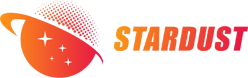
Niobium and niobium alloys (including Nb521 alloy) have the characteristics of high melting point, low density, excellent high-temperature strength and specific strength, good weldability and excellent corrosion resistance, and have broad application prospects in the fields of aviation and aerospace. When using traditional machining processes to prepare niobium and niobium alloys, due to the difficulty of processing, complex process, low material utilization rate and other reasons, a large amount of waste chips remain, resulting in a great waste of niobium resources and causing environmental pollution. Traditional melting and forging processes are difficult to achieve low-cost and high-performance precision manufacturing of niobium and niobium alloys with complex structures, which greatly limits the large-scale application and industrial development of niobium and niobium alloys. Compared with traditional processes, 3D printing near-net forming processes can integrate the preparation of high-performance and complex-shaped niobium and niobium alloy products, and have become a hot topic for global research in recent years. 3D printing processes usually use spherical metal powders with excellent fluidity as raw materials, and such powders are generally prepared by atomization methods. However, due to the extremely high melting point of niobium and niobium alloys, it is difficult to prepare fine (particle size below 45 μm) spherical powders of niobium and niobium alloys at low cost and high efficiency by traditional atomization process, which makes the price of spherical niobium and niobium alloy powders for 3D printing extremely high, becoming a key issue restricting the development and application of 3D printing high-performance niobium and niobium alloy products. It can be seen that the development of a low-cost and simple process for the preparation of niobium and niobium alloy powders for 3D printing is an urgent problem to be solved.
1 Experimental materials and methods
The preparation of nearly spherical Nb521 alloy powder for 3D printing is divided into two steps: hydrogenation-dehydrogenation (HDH) and fluidization modification. The HDH powder preparation uses cutting waste generated by traditional machining of Nb521 alloy as raw material. The hydrogen source is bottled H2 with a purity of 4 N (99.99%). The niobium chips are heated to 700 °C, and then the brittle hydrogenated Nb521 is prepared by heat preservation and hydrogenation. Then, the hydrogenated Nb521 is crushed to obtain powder, and then dehydrogenated at 700 °C to obtain irregular shaped hydrogenated dehydrogenated Nb521 alloy powder. Due to the irregular shape of the hydrogenated dehydrogenated powder and its extremely poor fluidity, it cannot meet the requirements of 3D printing powder laying. In order to improve the powder morphology, particle size distribution, sphericity and fluidity, the fluidized powder modification technology created by this project team was used, that is, the hydrogenated dehydrogenated Nb521 alloy powder was placed in a fluidized bed reactor and subjected to fluidized modification treatment for 10 to 30 minutes at a temperature of 450 to 900 °C and a certain flow rate (2 to 8 L/min) of high-purity flowing argon (purity of 5 N, oxygen mass fraction of 3 × 10‒6), as shown in Figure 1.
A JSM-SU8100 scanning electron microscope (SEM) was used to observe and measure the powder morphology and particle size; a MAC Science M21X X-ray diffraction (XRD) was used to analyze the powder phase; a Mastersizer 3000 laser particle size analyzer was used to determine the powder particle size; a Leco-Tch600 nitrogen, oxygen, and hydrogen content analyzer was used to determine the content of powder interstitial elements; a BT-1001 intelligent powder property tester was used to characterize the fluidity index of the fluidized powder; and an SLM 125HL printing device was used to evaluate the powder spreading effect.
2 Results and Discussion
2.1 Powder morphology and particle size distribution
Figure 2 shows the microscopic morphology of the hydrogenated dehydrogenated Nb521 alloy powder before and after fluidized modification. As shown in Figure 2 (a), Figure 2 (a1) and Figure 2 (a2), the Nb521 alloy powder prepared by hydrogenation and dehydrogenation has an irregular morphology, showing sharp edges and corners, and there are more ultrafine powders less than 10 μm. As shown in Figure 2 (b), Figure 2 (b1) and Figure 2 (b2), the number of ultrafine powder particles is significantly reduced after the powder is subjected to fluidization modification. As shown in Figure 2 (b1), the smoothness of the powder is improved due to the accelerated atomic migration rate on the powder surface at high temperature. As shown in Figure 2 (c) and Figure 2 (d), some fine powders are attached to the pits and cracks of large particles, which improves the sphericity of the powder to a certain extent. Figure 3 is the X-ray energy spectrum analysis of the Nb521 alloy powder before and after fluidization treatment. As can be seen from the figure, the phase composition of the Nb521 alloy powder before and after fluidization has not changed significantly, and both are single-phase structures with a body-centered cubic crystal structure. Table 1 shows the particle size analysis of the hydride dehydrogenation raw powder and the Nb521 alloy powder after fluidization treatment at different temperatures. It can be seen from the table that compared with the hydride dehydrogenation raw powder, the D10, D50, and D90 of the fluidized powder are slightly increased. With the increase of fluidization temperature, the particle size increases more obviously. This shows that the higher the fluidization temperature, the lower the surface energy of the powder, which is very likely to cause adhesion between powder particles, resulting in an increase in the overall particle size of the powder.
Figure 4 shows the particle size distribution of the powder before and after fluidization. Compared with the original hydride dehydrogenation powder before fluidization treatment, the particle size distribution curve of the powder after fluidization becomes narrower and shifts to the right. In other words, the ultrafine powder with a particle size less than 10 μm decreases, but the powder particle size increases. In addition, with the increase of fluidization treatment temperature, the particle size distribution curve of the treated powder becomes narrower, that is, with the increase of temperature, the trend is more obvious.
Figure 5 is a schematic diagram of the fluidization modification of powders, where v represents the relative tangential velocity. Since the powder is processed in a high temperature and high-speed airflow environment, firstly, the particles will collide and rub against each other, and the yield strength of the Nb521 alloy will drop significantly at high temperatures. The impact force and shear force generated by the collision and friction may cause plastic deformation of the sharp parts of the powder, which is conducive to eliminating the irregular surface edges of the Nb521 powder. Secondly, ultrafine powders tend to adhere to the surface pits of coarse particles, which significantly reduces the amount of ultrafine powders. At the same time, the collision between the fluidized powder particles leads to a decrease in their surface energy, and finally forms nearly spherical powder particles. In summary, after fluidization treatment, the particle size distribution and surface sphericity of the Nb521 alloy powder are improved, thereby greatly improving the fluidity of the powder.
2.2 Interstitial element content of powder
Generally, an increase in oxygen content increases the strength of niobium and niobium alloys, but also causes a decrease in their toughness and plasticity. Therefore, the oxygen content of Nb521 alloy powder is an important indicator for evaluating the final performance of the powder, which has an important influence on the mechanical properties of 3D printed Nb521 alloy parts. Table 2 shows the mass fractions of O, C, H, and N interstitial elements of Nb521 alloy powder before and after 450 ℃ fluidization treatment.
It can be seen from the table that the initial O, H, N, and C mass fractions of Nb521 alloy powder obtained by hydrogenation and dehydrogenation process are 0.26%, 0.009%, 0.021%, and 0.012%, respectively. After 450 ℃ fluidization treatment, the mass fractions of O and H elements are reduced. This is because ultrafine powder has a large specific surface area, high chemical activity, and is easier to adsorb impurity elements. However, during the fluidization process, a small amount of fine powder will be discharged from the fluidized bed equipment with the airflow, so the mass fraction of impurity elements in the powder after fluidization treatment is slightly reduced.
2.3 Powder Spreadability Evaluation
At present, powder bed or powder feeding 3D printing technology requires that the powder raw material has excellent fluidity in order to achieve a smooth powder feeding and spreading process. Therefore, the fluidity of the powder is a key factor in measuring whether the powder can be successfully transported and spread, and it also determines the performance and quality of the final 3D printed parts. The powder comprehensive property tester is used to characterize the fluidity index of the powder. Due to the serious agglomeration and bridging phenomenon, the fluidity of the hydrogenated dehydrogenated raw material powder is extremely poor. During the test, many powders were stuck inside the machine and no effective fluidity index data was obtained. After fluidization modification, the fluidity index of the powder increased to 66, which is a medium to high level and basically meets the powder spreading requirements of 3D printing. Figure 6 is the observation of the spreadability of the hydrogenated dehydrogenated raw material powder and the fluidized powder. Experimental process: Weigh the same weight of powder, and the powder falls on the platform through the funnel to show the spreadability of the powder. As shown in Figure 6 (a), due to the insufficient fluidity of the hydrogenated dehydrogenated powder before fluidization treatment, it showed serious agglomeration and bridging phenomena, so its spreadability was poor. On the contrary, the powder after fluidization treatment had significantly improved sphericity and particle size distribution, and the powder stacking angle was significantly reduced, which alleviated the agglomeration and bridging phenomena of the powder, as shown in Figure 6 (b), indicating that the fluidity of the fluidized powder was significantly improved.
The SLM 125HL model printing equipment was used to spread the Nb521 alloy powder on the printing substrate before and after fluidization treatment to characterize the fluidity and powder spreading effect of the powder. Due to the insufficient fluidity of the original hydrogenated dehydrogenated powder, its powder spreading effect was poor, and the powder was dispersed in a long triangular area on the substrate, and the distribution and thickness were uneven, indicating that it could not meet the requirements of uniform powder spreading for 3D printing. As shown in Figure 7 (b), the fluidized powder spread on the substrate of the printing chamber smoothly and evenly, which basically met the process requirements of 3D printing powder spreading. The above shows that the fluidized powder modification technology used in this study can effectively improve the fluidity of low-cost, irregular morphology powders, which can basically meet the needs of 3D printing process.
3 Conclusion
(1) The Nb521 alloy powder prepared by the hydrogenation and dehydrogenation powder preparation method has an irregular shape, a median diameter of 29.6 μm, and an oxygen content (mass fraction) of 0.26%.
(2) Based on the fluidized powder modification technology, the particle size distribution and sphericity of the hydrogenation and dehydrogenation Nb521 powder are improved, and the fluidity is significantly improved. With the increase of fluidization temperature, the effect is more obvious, the powder spreading effect is good, and the impurity content is effectively controlled.
(3) The preparation method of a near-spherical Nb521 powder for 3D printing proposed in this paper has the characteristics of low cost, simple process, and controllable impurities, which can effectively reduce the cost of 3D printing powder raw materials.
About Stardust Technology
Stardust Technology (Guangdong) Co., Ltd. is a national high-tech enterprise specializing in the research, development, production and sales of high-end spherical powder materials for 3D printing, powder metallurgy, surface engineering and other fields. The company insists on taking radio frequency plasma spheroidization powder making technology as the core, and provides internationally advanced powder products and application solutions.
The company's main products include high-end rare refractory metals such as tungsten, molybdenum, tantalum, niobium, vanadium, rhenium, chromium and their alloys, compound spherical powders, and also provides technical services such as radio frequency plasma spheroidization, plasma rotating electrode atomization, 3D printing, hot isostatic pressing, injection molding, powder metallurgy, etc.
Niobium tungsten alloy Nb521 material has excellent room temperature and high temperature mechanical properties and the advantages of high melting point, low density, high temperature and high strength and good machinability.
The spherical Nb521 refractory alloy powder produced by Stardust Technology is made by radio frequency plasma spheroidization atomization method, which has the characteristics of high purity hypoxia, high sphericity, smooth surface, no satellite, uniform particle size distribution, excellent flowability, high loose density and high vibration density.
Niobium tungsten alloy Nb521 is widely used in the manufacture of aerospace engines, weapon thrusters, rocket missile liquid bicomponent engines, nuclear reactors, submersibles, gas turbines, automobile engines, diesel engines, high-temperature furnace heating belts, high-temperature molds, high-temperature fixtures, and high-temperature crucibles.https://www.stardustpowder.com/spherical-refractory-nb521-powder-15-53m
For more details, please contact us
Paper citation information
Volume 40, No. 2 Powder Metallurgy Technology April 2022