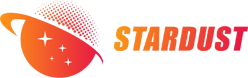
1 Introduction
Ta-10W alloy is a rare metal alloy material with high density, high melting point and high strength. It has high high-temperature strength, good ductility, weldability and excellent corrosion resistance. It is suitable for working environments such as high temperature, high pressure and corrosion resistance. It is a widely used engineering and functional material. Tungsten forms a substitutional continuous solid solution with tantalum in tantalum. Tungsten mainly plays a solid solution strengthening role on tantalum, significantly improving the mechanical properties of tantalum metal. Since Ta-10W alloy is often used in high-temperature environments, its high-temperature performance is an important performance that has received much attention. This article focuses on the high-temperature mechanical properties of Ta-10W alloy from 1000℃ to 2000℃, and discusses the law of changes in the mechanical properties of the alloy with temperature.
2 Test materials
The Ta-10W alloy rod used in the test is an ingot (ingot size φ97.5mm) melted twice by vacuum electron beam, hot forged to about φ34mm, vacuum annealed for recrystallization, cold worked to φ14 mm, and then vacuum recrystallized annealed. The chemical composition of the rod is shown in Table 1.
The sample was cut from the product, with a total length of 116 mm, a gauge length of 40 mm, and a test section diameter of φ5 mm. The sample was in a recrystallized state, and the metallographic structure is shown in Figure 1. This paper analyzes the change law of the mechanical properties of the alloy from 1000℃ to 2000℃, explores the reasons for the change law, and observes and analyzes the fracture at each temperature with SEM.
3 Test results
Figure 2 shows the relationship between the mechanical properties (tensile strength og, yield strength op02, elastic modulus E₁, elongation 6s and section shrinkage w) of the annealed Ta-10W rod and temperature. The tensile strength decreases rapidly from 1000℃ to 1600℃, and the decrease rate slows down from 1600℃ to 2000℃; the yield strength decreases slower than the tensile strength from 1000℃ to 1600℃, and is basically linear. As the temperature rises, the two curves become closer and closer, that is, the yield strength ratio of the material increases. The elastic modulus decreases basically linearly from 1000℃ to 1600℃, and then enters a platform.
The elongation of Ta-10W rods gradually increases from 1000℃ to 1200℃, and then enters a platform. From 1400℃, the elongation gradually increases again, reaches the highest point at 1600℃, and then gradually decreases, and enters a platform again at 1800℃. The cross-sectional shrinkage gradually increases from 1000℃ to 1200℃, and then enters a platform, and then gradually increases at 1600℃, reaches the highest point at 1800℃, and then enters a platform again. Both the elongation and the cross-sectional shrinkage rate showed a platform at 1200℃, but the cross-sectional shrinkage rate platform continued to 1600℃, and the elongation rate only continued to 1400℃.
Figure 3 shows the SEM morphology of the sample fracture at various temperatures, with the following characteristics:
① At 1000℃, it is a typical equiaxed dimple fracture, and the dimple is small (Figure 3a).
② At 1200℃, the dimple is larger and deeper than that at 1000℃, indicating that the plasticity of the material has improved. There are inclusions at the bottom of the dimple (see Figure 3b).
③ At 1400℃, the large dimple is surrounded by dense small dimples, and secondary cracks perpendicular to the slip direction can be seen. There are obvious traces of grain boundary sliding, and the morphology of intergranular fracture can also be seen. The fracture at this temperature is more complicated and should be a mixed fracture of dimples and intergranular fracture (see Figures 3c and 3d).
④At 1600℃, two different fracture morphologies appeared at the same time, one is a common dimple, and the other is a special new dimple, with a relatively regular serrated longitudinal section. There is a secondary crack at the bottom of this dimple. It may be because of the simultaneous appearance of these two different dimples that the elongation of the material reaches the highest at 1600℃ (see Figure 3e).
⑤At 1800℃, it returns to equiaxed dimple fracture. The dimple is larger and deeper, indicating better plasticity. At this time, the cross-sectional shrinkage of the material reaches the maximum. Inclusions are found at the bottom of the dimple (see Figure 3f).
⑥At 2000℃, the same new type of dimple as at 1600℃ appears again, and this time this new type of dimple exists alone. SEM analysis shows that there are Al and O inclusions at the bottom of the dimple. At this time, the cross-sectional shrinkage has not decreased and is still on the highest platform. The elongation is slightly lower than that at 1600℃ and is on the same platform as at 1800℃ (see Figures 3g, 3h).
4 Discussion
During the high temperature stretching process, there are two opposite processes, work hardening and dynamic recovery or recrystallization. The role of dynamic recovery is to offset the work hardening effect, but if it is slow, the energy storage will continue to increase during the deformation process, and dynamic recrystallization can occur when a certain critical condition is reached. Although the microstructural changes produced by these two softening processes are different, they are both thermally activated processes, and the flow stress is closely related to temperature and strain rate. Under the condition of a certain strain rate, the deformation temperature plays a decisive role. The higher the temperature, the greater the effect of dynamic recrystallization. Work hardening occurs at the same time as dynamic recrystallization, and the cause of work hardening is the result of dynamic strain aging. Dynamic strain aging is an aging process that occurs when metals and alloys undergo plastic deformation. In essence, dynamic strain aging is the result of the interaction between solute atoms and dislocations. When dynamic strain aging occurs, strengthening and plastic deformation occur simultaneously. Solute atoms chase the movement of dislocations through diffusion and interact with dislocations to pin them. The diffusion capacity of solute atoms increases with increasing temperature. The law of the change of the plasticity and strength of the material with the increase of temperature depends on the result of the combined effect of dynamic recrystallization and dynamic strain aging.
When stretched at 1000℃, the dynamic recrystallization of the material interacts with the proliferation of dislocations caused by work hardening. With the increase of temperature,
on the one hand, the cross slip of dislocations changes to the climb of dislocations. On the other hand, the increase of temperature further reduces the strength of the grain boundary. Therefore, grain boundary sliding and intergranular fracture occur at 1200℃ and 1400℃. The increase of temperature also starts a new slip system, which improves the plasticity of the material. At 1600℃, the appearance of double dimples in the tensile fracture further increases the plastic deformation of the material, which further improves the plasticity of the material. The higher the temperature, the greater the effect of dynamic recrystallization and the better the plasticity of the material. The cross-sectional shrinkage rate gradually increases with the increase of temperature, indicating that the area where the Ta-10W alloy undergoes plastic deformation expands with the increase of temperature, thereby improving the plasticity of the alloy. The new dimples appeared at 1600℃ and 2000℃. The plasticity of this new dimple is very good, so that the alloy reaches the highest elongation at 1600℃, the maximum cross-sectional shrinkage at 1800℃, and maintains high plasticity until 2000℃. The main reason for the formation of this dimple is the presence of high melting point inclusions at the bottom of the dimple, and the impurities become crack sources. This is confirmed by SEM observations at 1800℃ and 2000℃.
The elastic modulus is an index of the resistance of metals and alloys to elastic deformation, while the yield strength is an index of the resistance of metals and alloys to plastic deformation. Both are manifestations of the deformation resistance of materials, so as the test temperature increases, the two show a similar downward trend. The deformation resistance of Ta-10W alloy decreases slowly with the increase of test temperature, which is related to the high solute atom content of the alloy. The high solute atom content causes the alloy to further strengthen the effect of dynamic strain aging, thereby increasing the work hardening rate of the alloy. On the other hand, the higher the temperature, the greater the effect of dynamic recrystallization. As can be seen from Figure 4, as the temperature increases, the closer the tensile strength is to the yield strength, the smaller the work hardening increment of the material is, and the change is basically linear. This is an obvious proof that the dynamic recrystallization effect increases with the increase of temperature. As a result of the combined effect of dynamic strain aging and dynamic recrystallization, the yield strength and elastic modulus of Ta-10W alloy slowly decrease with the increase of temperature.
5 Conclusion
1) With the increase of test temperature, the tensile strength, yield strength and elastic modulus of Ta-10W alloy all show a downward trend, but the decrease rate of tensile strength is faster, while the decrease rate of yield strength and elastic modulus is obviously slowed down;
2) With the increase of test temperature, the elongation and cross-sectional shrinkage of Ta-10W alloy increase slightly;
3) The change law of strength and plasticity of Ta-10W alloy with increasing temperature is the result of the combined effect of dynamic recrystallization and work hardening caused by dynamic strain aging, and at high temperature, dynamic recrystallization plays a leading role;
4) Through the analysis of the fracture mechanism of Ta-10W alloy, it can be concluded that with the increase of test temperature, the influence of high melting point substances on the alloy becomes greater and greater, and the effect of dynamic recrystallization becomes more and more obvious.
Paper citation information:
RARE METALMATERIALSANDENGINEERING
Vol.35, Suppl.2 August 2006
The spherical Ta-10W alloy powder produced by Stardust Technology is prepared by radio frequency plasma spheroidization process, with the characteristics of high purity and low oxygen, high sphericity, smooth surface, no satellite, uniform particle size distribution, excellent flowability, high bulk density and tap density.
https://www.stardustpowder.com/tantalum-10-tungsten-alloy-powder-15-53mm
The following are the printing verification parameters of the spherical Ta-10W alloy powder produced by Stardust Technology. For more details, please contact Vicky+86-13318326185