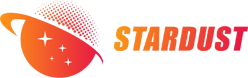
Abstract: This paper introduces the research progress of additive manufacturing of pure tungsten, high-density tungsten alloys and W-Cu composites from the aspects of forming process and microstructure of formed parts, and introduces the application and main problems of additive manufacturing of tungsten alloys.
Tungsten is an important refractory metal material with the characteristics of high melting point and boiling point, high hardness, low expansion coefficient and low vapor pressure. It has important applications in aerospace, electronics, chemical industry, nuclear industry and other extreme environment fields[1]. However, due to its high melting point and low-temperature brittleness, tungsten is difficult to be prepared using conventional casting and machining methods. Usually, most tungsten parts are prepared by powder metallurgy, but the application range of conventional sintered tungsten products is greatly limited due to the disadvantages of low density, low strength, poor plasticity and difficult to control impurity content[2-3]. At the same time, in practical applications, the structure of tungsten parts is often complex, usually with features such as curved surfaces, curved pipes, holes and grooves, which are difficult to achieve with traditional powder metallurgy methods. Therefore, in order to overcome the shortcomings of traditional forming methods, it is necessary to adopt some new forming technologies.
In recent years, the rapidly developing metal additive manufacturing technology (or 3D printing technology) uses high-energy heat sources to melt metal powders and directly manufacture three-dimensional solid parts through a point-by-line-by-layer stacking method. It has the advantages of mold-free and near-net forming. In addition, due to the use of micro-melting pool layer-by-layer stacking, small melting volume, and fast solidification speed, the formed sample has fine structure and excellent mechanical properties [4-5]. At present, this technology has been widely used in the manufacture of complex parts of stainless steel, high-temperature alloys and titanium alloys [6-8]. This technology also provides an effective way to prepare high-melting-point tungsten alloys. There are many types of tungsten alloys, mainly including solid solution alloys, precipitation-strengthened alloys, high-density tungsten alloys, W-Cu, W-Ag composites and WC cemented carbide, etc. However, there are still few reports on additive manufacturing of tungsten at home and abroad, mainly focusing on pure tungsten, W-Ni-Cu, W-Ni-Fe high-density alloys and W-Cu composites. This article introduces the research progress, application status and main problems faced by additive manufacturing technology for preparing tungsten materials.
1 Typical additive manufacturing process of tungsten and tungsten alloys. Most of the additive manufacturing tungsten and tungsten alloys reported so far are prepared by laser selective melting forming technology in additive manufacturing technology. The process of laser selective melting forming is to first build a three-dimensional model of the part, and then slice and layer the model according to a certain thickness. The laser beam selectively melts the metal powder raw material spread on the powder spreading platform according to the information of the slice. After the melting is completed, the powder spreading platform drops to a certain height, and then spreads another layer of powder, and then selectively melts. This is repeated, and after layer-by-layer melting and accumulation, a metal part with metallurgical bonding and dense organization is finally formed.
2 Additive manufacturing of pure tungsten materials
Pure tungsten materials play a very important role in modern electronics, semiconductors, photovoltaic industries, etc. due to their good electrical conductivity and high temperature stability. However, due to the high melting point, high density, low thermal conductivity, high melt surface tension and high viscosity of tungsten, the small droplets are unstable and the spheroidization phenomenon is significant during the additive manufacturing process, resulting in greater difficulty in additive manufacturing. Zhou Xin et al. [9-10] conducted a study on the laser selective melting forming process of pure tungsten to address the above problems. They used laser scanning of a single layer of powder to study the laser melting-solidification process of pure tungsten powder, explored the forming processing window, and observed the spheroidization phenomenon of the molten droplet. They also used the molten droplet spreading-solidification competition model to explain the spheroidization mechanism, and proposed to use the enhanced substrate and powder to absorb the laser to increase the peak temperature of the molten droplet and prolong the solidification time to reduce the spheroidization tendency. In the additive manufacturing process, micro-molten pools are stacked layer by layer, the melting amount is small, and the solidification speed is fast, so the microstructure of the additively manufactured tungsten alloy will be different from that of the tungsten alloy prepared by the traditional powder metallurgy method. Zhang Danqing et al. [11] observed the microstructure of pure tungsten samples formed by laser selective melting and found that laser melting-solidification formed a needle-like structure with a size of about 500 nm and a certain directionality. The formation of this microstructure is due to the fact that the processing directions of the heat flow between layers are perpendicular to each other during the layer-by-layer melting process, resulting in directional growth of the crystal structure; on the other hand, it is due to the laser heat source acting on the metal powder to form a fine molten pool, which is formed under the action of the melt surface tension. At the same time, it is found that the microhardness of the formed sample decreases with the increase of the number of scanning layers. When the scanning thickness increases from the first layer to the sixth layer, the microhardness of the sample decreases from 826HV to 353HV, and then the microhardness fluctuates in the height direction of the sample.
3 Additive Manufacturing of High-density Tungsten Alloys
High-density tungsten alloys are based on tungsten (the mass percentage of tungsten is 85% to 99%), with a small amount of Ni, Cu, Fe and other elements added, and the density can reach 16.5 to 19.0 g/cm3
. This alloy has the advantages of high density, high strength, good ductility and no pollution. It is widely used in the inertial rotating elements, counterweight elements and weapon materials such as armor-piercing projectile cores in the aerospace field. At present, the research on additive manufacturing of tungsten alloys is mainly focused on high-density tungsten alloys, especially W-Ni, W-Ni-Fe and W-Ni-Cu systems. It is difficult for pure tungsten laser selective melting samples to form a completely dense structure under low energy input. However, since low melting point elements such as Ni, Cu, and Fe are added to high-density tungsten alloys, low melting point Ni powder, Fe powder, Cu powder, and W powder are mixed as raw materials. During the additive manufacturing process, an activated sintering process similar to that in the powder metallurgy process can be formed, which can effectively improve the density of the product. Zhang DQ et al. [12] studied the forming mechanism and microstructure evolution of W-Ni alloy during laser selective melting. They pointed out that the forming mechanism is that Ni particles and part of W particles melt as a bonding phase, and the solid phase W particles are liquid-phase sintered. The microstructure of W-Ni in additive manufacturing was studied and showed that with the increase of Ni content, the microstructures of W-Ni alloy formed by laser selective melting are strip-shaped, dendritic-shaped, and honeycomb-shaped. This is mainly due to the addition of low melting point element Ni, which changes the heat absorption rate, specific heat, melting point, etc. of the powder, causing a decrease in temperature gradient and cooling rate. The increase in Ni content can effectively reduce the viscosity of the melt, improve the heat flow performance of the melt, and improve the uniformity of the structure. Zhang Danqing et al. [13] studied the forming mechanism and microstructure evolution of the W-Ni-Cu alloy laser selective melting process and pointed out that its sintering mechanism is a comprehensive effect of liquid phase sintering and tungsten particle melting-solidification. The densification process of the alloy can be attributed to the movement of the un-escaped gas in the powder layer and the improvement of liquid phase flow. At the same time, the W-Ni-Fe alloy was used as the research object [14], and the finite element method was used to simulate the influence of laser selective melting forming process parameters on the temperature field, revealing the mechanism of the alloy sintering process. Studies have shown that under the premise of a certain laser power and high scanning speed, the mechanism of densification of W-Ni-Fe alloy is liquid phase sintering, and the structure is liquid phase solidification bonding unmelted particles; as the scanning speed decreases, the dendrites in the structure gradually increase, indicating that the molten pool temperature increases and the tungsten particles melt; when the scanning speed is further reduced, the alloy structure is a columnar crystal structure, and its forming mechanism is the alloy powder melting-solidification mechanism. Li Ruidi [15] et al. also studied the laser selective melting forming technology of high-density tungsten alloy (W-7Ni-3Fe) and reached a similar conclusion. Wang Pan et al. [16] used laser selective melting to prepare W-Ni-Fe high-density alloy mechanical tensile test pieces. By testing the tensile strength and hardness, combined with the research and analysis of the structure and composition ratio, it is pointed out that there is still a certain gap between the mechanical properties of the sample and the traditional powder metallurgy sintering process.
4 Additive manufacturing of tungsten-copper composites
W-Cu composites have the advantages of good arc erosion resistance, welding resistance and high strength due to their high electrical conductivity and thermal conductivity of copper and high temperature strength and strong arc ablation resistance of tungsten. This makes W-Cu composites widely used in the fields of power, electronics, machinery and metallurgy, especially in the electrical contacts of various high-voltage electrical switches. Li Ruidi et al. [17-18] studied the process of forming W-Cu composites by laser selective melting. The results show that due to the high thermal conductivity of Cu, it is difficult to form a high temperature field. At the same time, due to the large difference in the melting points of W and Cu, the forming of W-Cu composites is mainly achieved through liquid phase sintering, that is, the tungsten skeleton is bonded by liquid phase Cu to achieve densification. Dai Donghua et al. [19] simulated the temperature field and velocity field of the molten pool during the process of laser selective melting of W-Cu composites, and studied the stress and densification process of W powder particles in Cu melt. The study pointed out that as the laser power increases from 600W to 900W, the Marangoni flow characteristics in the molten pool change significantly. When the laser power is greater than 800W, pressure F and secondary flow caused by the pressure difference will be formed around the powder. When the angle between the pressure F and the gravity FR generated by the secondary flow is acute, the W particles tend to form a small ring structure, the particles are difficult to rearrange, and they are easy to agglomerate; when the angle between the pressure F and the gravity FR generated by the secondary flow is obtuse, the W particles tend to form a large ring structure, which is conducive to the rearrangement of particles. Gu Dongdong [20-21] et al. used laser selective melting forming technology to prepare a series of W-Cu composite materials with W content ranging from 30wt% to 50wt%. At the same time, it was found that when the Cu content reached 40%, under the rearrangement of the Marangoni gas flow and solid tungsten particles, a special microstructure of W ring Cu core can be formed.
5 Application in Typical Parts
At present, additive manufacturing of tungsten parts has been applied to a certain extent internationally. Smit R駟ntgen, a subsidiary of Philips and a manufacturer of medical imaging parts, has developed a series of products using additive manufacturing of pure tungsten. Taking advantage of the additive manufacturing process in the preparation of thin-walled parts, Smit R駟ntgen used laser selective melting technology to prepare pure tungsten pinhole collimators, which brings great manufacturing freedom to the collimation aperture angle and shape. At the same time, since the additive manufacturing process can reduce material consumption and save production costs, it can achieve more complex designs and make geometric shapes that cannot be achieved by traditional technology compared to traditional metal casting. Smit R駟ntgen also applies additive manufacturing technology to the forming of high-precision tungsten parts on X-ray fluoroscopy equipment such as CT/PET/SPECT. These tungsten parts have free structures and low manufacturing costs. At the same time, the company has also begun to design and produce industrial parts to accurately and efficiently manufacture highly complex concave or support parts. In addition, the European Space Agency also demonstrated a tungsten alloy component that can withstand 3000℃ made by laser selective melting process at Amaze launched at the Science Museum in London. ESA said that the component can work in nuclear fusion reactors and rocket nozzles.
6 Conclusion
At present, the additive manufacturing process of tungsten alloy in China mainly uses laser as the energy source, which can be fully formed under certain conditions, but during the forming process, the sample density may be low, the microstructure uniformity may be poor, and the composition may be segregated. The performance of the sample cannot be improved, and in-depth forming process research, strengthening process monitoring, and improving the geometric accuracy of complex parts forming are required. At the same time, higher energy additive manufacturing processes can be introduced, such as electron beam selective melting forming process, which is also a typical metal additive manufacturing technology. Its working principle is similar to laser selective melting, but because it uses high-energy electron beam as the energy source and uses magnetron deflection to control the electron beam, it can more effectively improve the forming energy and forming efficiency, while avoiding cracking of the formed parts. It is also a more ideal forming method.
Paper citation information
Hot Working Technology 2016,Vol.45,No.24
DOI: 10.14158/j.cnki.1001-3814.2016.24.004
Stardust Technology uses radio frequency plasma spheroidization technology to prepare a variety of refractory spherical powders, including tungsten (W), molybdenum (Mo), tantalum (Ta), niobium (Nb), vanadium (V) and other refractory metals and their alloys and compound spherical powders to meet the diverse needs of different industries and different application scenarios. The powder's excellent fluidity, high bulk density and tap density allow it to be tightly packed during the 3D printing process, reducing the generation of pores, making the internal structure of the printed product dense, and significantly enhancing the mechanical properties of the material.
For more details, please contact Vicky Zhang at +86-13318326185