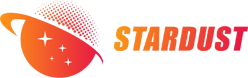
The application of additive manufacturing technology in the nuclear field has significant advantages and potential and can provide strong support for the development of the nuclear energy industry. Recently, another new application has emerged in the field of nuclear energy - debris filter bottom nozzle (fuel tube holder). The more well-known foreign companies are Westinghouse Electric and the domestic China Nuclear Power Research and Design Institute. Both institutions are making breakthroughs and playing a leading role in the application of nuclear energy additive manufacturing technology.
Series Additive Manufacturing of Nuclear Energy Components and Development of New Applications
With its forward-looking technological vision, Westinghouse Electric Company has become a well-known industry leader in using additive manufacturing technology to produce nuclear energy components. In March 2024, the company manufactured its 1,000th additively manufactured flow plate for reactor fuel. This particular part represents a major achievement for the nuclear energy industry, as it is the first additively manufactured component to enter series production for nuclear safety.
The company recently unveiled an innovatively designed bottom nozzle (fuel pipe holder). The new design significantly improves the debris removal efficiency and fuel durability in the fuel assembly, providing a strong guarantee for the safe operation and long-term stability of nuclear power plants. Assure. It is reported that these carefully manufactured nozzles have been successfully integrated into four fuel assemblies and are expected to be officially delivered to the nuclear power plant in the first quarter of 2024.
Westinghouse Electric develops additively manufactured nuclear fuel tube sockets
In pressurized water reactors (PWR), wear and tear of accumulated dirt particles on the fuel rod cladding (referred to in the industry as fouling) is one of the main causes of fuel assembly leakage. Westinghouse Electric Company uses additive manufacturing technology to significantly optimize the debris filtering effect by increasing the degree of design freedom, effectively reducing the diameter of debris particles entering the reactor. In rigorous testing, these additively manufactured components demonstrated excellent anti-fouling properties, improving their anti-fouling properties by 30% compared to traditional components.
Additively manufactured VVER-1000 spacer
This important milestone further consolidates Westinghouse's leadership in developing advanced solutions using additive manufacturing technology in the nuclear industry. As early as 2015, Westinghouse conducted pioneering material irradiation research on additively manufactured nuclear components. By 2020, the company successfully installed the first safety-related additively manufactured component in a commercial reactor - a casing plug. In 2024, Westinghouse produced the 1,000th additively manufactured part for VVER-440 fuel. This milestone once again demonstrated the company's deep strength in additive manufacturing. Tarik Choho, President of Westinghouse Nuclear Fuels, said: "Our additive manufacturing technology not only achieves breakthrough performance improvements, but also brings immediate positive impacts to our customers. This major technological innovation for pressurized water reactors effectively reduces the risk of fuel rod leakage due to debris accumulation, thereby enhancing the safety and efficiency of customers' operations."
Application of additive manufacturing technology in the domestic nuclear energy field
According to the Chinese government website, in 2016, the China Nuclear Power Research and Design Institute and Southern Additive Technology Co., Ltd. successfully printed my country's first small reactor (ACP100) pressure vessel test piece using self-developed heavy metal additive manufacturing technology. This marks a breakthrough in the most difficult material basic research and development and process research and development of additive manufacturing nuclear power pressure vessels, and is also a breakthrough in my country's heavy equipment manufacturing technology.
In addition, according to the National Energy Administration in 2018, China General Nuclear Power Group's subsidiary China General Nuclear Power Nuclear Power Operation Co., Ltd. took the lead in scientific research on the application of additive manufacturing technology in the field of nuclear power, and carried out the "3D printing technology in the manufacturing and maintenance of nuclear power plant spare parts and components key technology research" research project. And realized the engineering demonstration application of additive manufacturing technology at Daya Bay Nuclear Power Station, using metal additive manufacturing technology to develop and manufacture the nuclear compressed air production system refrigerator end cover, marking the additive manufacturing technology in the field of nuclear power has made a breakthrough progress.
According to the news released by the Nuclear Power Research and Design Institute of China, in 2021, the institute demonstrated the additive manufacturing modular high-efficiency heat exchanger, Longyan 350 nuclear energy customized 3D printer and Ruimou intelligent monitoring system jointly developed with Hanbang Laser and others at the TCT Asia Exhibition; in 2023, the institute took the lead in establishing two important additive manufacturing research and promotion institutions in the nuclear energy field-the Sichuan Provincial Key Laboratory of Nuclear Energy Additive Manufacturing and the Nuclear Energy Working Group of the China Additive Manufacturing Industry Alliance; in the same year, the Ministry of Industry and Information Technology announced the list of typical application scenarios for additive manufacturing in 2023, and the institute's application for "full process monitoring and forming manufacturing of nuclear energy equipment" was successfully selected.
Modular high-efficiency heat exchanger manufactured by additive manufacturing (from the Nuclear Power Institute)
The "Rui Mou" process monitoring system developed by the Nuclear Power Institute of China (from the Nuclear Power Institute of China)
According to public information, the institute is one of the earliest units in the domestic nuclear energy field to carry out and continuously promote research on additive technology. In 2021, it was identified by the Ministry of Industry and Information Technology as the leading unit of "one-stop additive manufacturing" in the nuclear energy field. The Nuclear Power Institute said that it will focus on promoting the widespread application of additive products in the nuclear energy field in the next step, and contribute to the high quality of the nuclear power industry.
What issues should be considered in the application of nuclear energy additive manufacturing technology
The successful application of additive manufacturing in the field of nuclear engineering has fully demonstrated the great potential of this technology in improving the safety and efficiency of nuclear power plants and reducing operating costs. As the technology continues to mature and its application expands, we have reason to believe that additive manufacturing will be more widely recognized and applied in the entire nuclear power industry in the future, injecting new impetus into the development of clean energy.
The application of additive manufacturing components in the field of nuclear safety must fully consider the selection and performance of materials to ensure high temperature resistance, radiation resistance and corrosion resistance; design and manufacturing precision to ensure the accuracy and reliability of components; safety and reliability assessment, covering equipment, data and material safety; production cost and efficiency to achieve cost-effectiveness optimization; and environmental and health impacts to ensure compliance with environmental protection requirements and no harm to public health. Only after these factors are fully met and evaluated can additive manufacturing technology be safely and effectively applied in the field of nuclear safety.
END
In general, additive manufacturing technology, with its unique molding principle, makes it possible to manufacture nuclear energy components with complex shapes and internal structures. From nuclear reactor fuel assemblies to high-precision components such as heat exchangers and nozzles, additive manufacturing technology has demonstrated its high efficiency, precision and flexibility. This technology can optimize material use, reduce waste, reduce production costs, and improve component performance and reliability.
The application of additive manufacturing technology in the nuclear energy field internationally has also become diversified, and has shown great potential and value in manufacturing, maintenance, fuel production, waste treatment, etc. With the continuous advancement of technology and the continuous expansion of the market, additive manufacturing technology will play a more important role in the nuclear energy field and make greater contributions to the development of global clean energy.