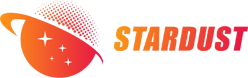
3D打印用球形钨、钽粉末的等离子球化工艺研究
ZHANG Taomei 1 , ZI Xuhui 1 , CHEN Xiaofan 1 , CHEN Chao 1, 2 , ZHOU Kezhao 1, 2
( 1. State Key Laboratory of Powder Metallurgy, South Central University, Changsha, Hunan 410083, China)
2. Shenzhen Research Institute, Central South University, Shenzhen, Guangdong, 518057, China)
Abstract: In order to obtain spherical refractory metal powders suitable for 3D printing, tungsten and tantalum powders with irregular shape were spheroidised by a radio frequency (RF) plasma torch, and the effects of spheroidisation process parameters on the physical and chemical properties of tungsten and tantalum powders, such as sphericity, particle size distribution, bulk density, mobility, oxygen content, etc., were studied, and the selective laser melting technique was chosen to verify the suitability of the powders for printing before and after spheroidisation. The morphology and particle size distribution of tungsten powder and tantalum powder before and after spheroidisation were characterised by scanning electron microscopy (SEM) and laser particle size analyzer (LPSA), respectively, and the changes in oxygen content of tungsten powder and tantalum powder before and after spheroidisation were detected by nitrogen-oxygen analyser. The results show that the proportion of spherical powder increases with the decrease of the feeding rate. When the feeding rate of tungsten powder and tantalum powder is 6g/min and 10g/min respectively, the spheroidisation rate of tungsten powder and tantalum powder is more than 95%. The particle size distribution of tungsten and tantalum powders after plasma treatment was more concentrated, and the fluidity and bulk density of the powders were significantly improved.
Keywords: plasma spheroidisation; refractory metals; tungsten powder; tantalum powder; spherical powder; selective laser melting
Classification number: TG146.3 Literature symbol code: A
Article Number:1672-7207(2022)07-2439-08
Plasma spheroidisation of tungsten/tantalum powders for 3D printing
ZHANG Taomei1, ZI Xuhui1, CHEN Xiaofan1, CHEN Chao1, 2, ZHOU Kechao1, 2
( 1. State Key Laboratory of Powders Metallurgy, Central South University, Changsha 410083, China; 2.
2. Shenzhen Research Institute, Central South University, Shenzhen 518057, China)
Abstract: In order to obtain spherical refractory metal powder for 3D printing, the irregular shape tungsten powders and tantalum powders were spheroidised by RF plasma torch. The effects of spheroidizing process parameters such as sphericity, particle size distribution, bulk density, fluidity and oxygen content on the physicochemical properties of the powder were investigated. The effects of spheroidising process parameters such as sphericity, particle size distribution, bulk density, fluidity and oxygen content on the physicochemical properties of tungsten powders and tantalum powders were studied. powders and tantalum powders before and after spheroidisation was ve
Table 1 Process parameters of plasma spheroidization
实验参数 | 数值 |
中心气体(Ar)流量/(L·min−1) | 25 |
鞘气(Ar)流量/(L·min−1) | 90 |
载气(Ar)流量/(L·min−1) | 3.5 |
送粉速率/(g·min−1) | 4~25 |
球化过程压力/(6.890 kPa) | 14.7 |
等离子发射器功率/kW | 15 |
Table 2 Process parameters of selective laser melting of irregular and spherical tungsten and tantalum powders
样品 | 激光功率/W | 激光扫描速度/(mm·s-1) | 层厚/mm | 扫描间距/ mm |
钨粉 | 475 | 600 | 0.03 | 0.09 |
钽粉 | 250 | 600 | 0.03 | 0.09 |
2 Analysis and discussion of results
2.1 Effect of feeding rate on the morphology of tungsten and tantalum powders
The SEM images of pristine tungsten powder and tantalum powder and spheroidised tungsten powder and tantalum powder at different feeding rates are shown in Figures 1 and 2, respectively. The irregular pristine tungsten powder and pristine tantalum powder shown in Fig. 1(a) and Fig. 2(a), respectively, both exhibit serious agglomeration and adhesion. From Figs. 1(b)~1(f) and Figs. 2(b)~2(f), it can be seen that the feeding rate significantly affects the morphology of the spheroidised metal powders; when the feeding rate of tungsten and tantalum powders is more than 10 g/min, the contents of spherical tungsten and tantalum powders in the field of view are less, and the contents of irregular powders are more, and the agglomeration phenomenon of the powders is more obvious. This is mainly due to the fact that the energy absorbed by individual tungsten and tantalum powder particles is not enough to melt them completely when the feeding rate is too fast. From Figures 1(d) and 2(d), it can be seen that: when the feeding rate decreased to 10 g/min, the spherical tungsten powder and tantalum powder increased, and the agglomeration phenomenon was obviously reduced; when the feeding rate of tungsten powder and tantalum powder decreased to less than 6 and 8 g/min, respectively, most of the tungsten powder and tantalum powder were spheroidised, and the distribution of the particles was uniform, and the agglomeration phenomenon basically disappeared. The spheroidisation rate of tungsten powder was counted using Image-Pro Plus (IPP) software. When the feeding rate of tungsten powder and tantalum powder was 6 g/min and 10 g/min, the spheroidisation rates of tungsten powder and tantalum powder were more than 95%; when the feeding rate of tungsten powder was more than 6 g/min, the spheroidisation rate of tungsten powder was obviously reduced; when the feeding rate of tungsten powder was more than 15 g/min, the spheroidisation rate of tungsten powder was less than 50%. This rule also applies to the spheroidisation process of tantalum powder.
When the critical feeding rate is exceeded, as the feeding rate rises, the tungsten powder and tantalum powder passing through the plasma area in unit time increases, and the energy required for the completion of globalisation of the powder particles also increases, but the energy provided by the plasma is a fixed value under the determined experimental conditions, and no more energy can be provided, and at this time, most of the tungsten and tantalum particles melt and spheroidise due to the failure of obtaining sufficient energy in the plasma torch, leading to spheroidisation. In this case, most of the tungsten and tantalum powder particles are melted and spheroidised due to insufficient energy in the plasma torch, resulting in a low spheroidisation rate. On the contrary, when the delivery rate is low, fewer powder particles enter the plasma torch per unit time, and the particles can absorb enough energy to melt into liquid droplets and sphericalise under the action of surface tension, and finally solidify into spherical powder, and in this process, the carrier gas will take away the smaller powder particles, and at this time, the recovery rate of the powder will be reduced [24]. Therefore, the optimum powder feeding rates for tungsten and tantalum powders are 6 g/min and 10 g/min, respectively. In addition, agglomeration of small spherical powders was observed in the SEM images after spheroidisation, which may be attributed to the fact that the spherical droplets, which have not yet solidified to completion, collide with each other during the spheroidisation process and are agglomerated together after the solidification is completed.
(a) 原始钨粉;(b) 25 g/min;(c) 15 g/min;(d) 10 g/min;(e) 6 g/min;(f) 4 g/min
Fig. 1 SEM images of original tungsten powders and tungsten powders after plasma spheroidization at different feeding rates
(a) 原始钽粉;(b) 16 g/min;(c) 12 g/min;(d) 10 g/min;(e) 8 g/min;(f) 6 g/min
Fig. 2 SEM images of original tantalum powders and tungsten powders after plasma spheroidization at different feeding rates
In summary, the larger the feeding rate, the smaller the spheroidisation rate of tungsten and tantalum powders. It can be seen from Fig. 1 and Fig. 2: when the feeding rate exceeds the critical value, the spheroidisation rate of tungsten powder and tantalum powder decreases rapidly with the increase of feeding rate. Therefore, controlling the feeding rate has a very important influence on the spheroidisation effect of tungsten powder and tantalum powder.
2.2 Influence of feeding rate on particle size distribution of tungsten powder and tantalum powder
The laser particle size analyser was used to determine the particle size of the original tungsten powder and tantalum powder, as well as tungsten powder and tantalum powder with a spheroidisation rate of 95%, and the particle size distribution is shown in Figure 3. As seen in Figure 3, the particle size distribution of raw tungsten powder and tantalum powder is relatively wide, and for tungsten powder and tantalum powder with a spheroidisation rate of 95% (as shown in Table 3), the particle size distribution of spherical tungsten powder and tantalum powder is relatively narrow. The main reason is that, in the spheroidisation process, when the powder enters the plasma zone, very few nano-sized primitive powders melt and vaporise directly at high temperatures, and the rest of them are also formed into fine particles as a result of cooling and are collected by the cyclone collector along with the working gases, so there are basically no nano-sized particles . When the large particles enter the plasma high temperature zone, the particles melt into large droplets, and when moving with the working gas, due to their own surface tension and the role of the external gas can not maintain its original size, so it is divided into two or more droplets, and then cooled into multiple small spherical particles. There are also more agglomerates in the original powder particles, which are dispersed into smaller spherical particles during the spheroidisation process, which are evenly dispersed, so that the average size of the overall powder becomes smaller after spheroidisation, and the distribution of the particle size is more concentrated.
(a) Raw tungsten powder and tungsten powder after spheroidisation at the optimum feed rate;
(b) Raw tantalum powder and tantalum powder after spheroidisation at the optimum feed rate
Fig. 3 Particle size distribution of tungsten powders and tantalum powders
Table 3 Particle size distribution of original and spherical tungsten powders/tantalum powders
样品 |
D10/μm |
D50/μm |
D90/μm |
原始钨粉 |
27.80 |
54.9 |
101.0 |
球形钨粉 |
24.10 |
46.1 |
83.6 |
原始钽粉 |
4.91 |
14.4 |
46.7 |
球形钽粉 |
5.31 |
13.3 |
37.2 |
Note: D10, D50 and D90 are the particle sizes when the cumulative mass fraction of particles reaches 10%, 50% and 90%, respectively.
2.3 Effect of sphericity on the flowability and bulk density of tungsten and tantalum powders
In order to study the effect of spheroidisation rate on the flowability and bulk density of the powders, a flow meter was used to determine the flow rate and bulk density of the original tungsten and tantalum powders and the tungsten and tantalum powders with a spheroidisation rate of more than 95% (hereafter referred to as spherical tungsten powders) in Fig. 2, and the results of the measurements are shown in Table 4. From Table 4, it can be seen that after spheroidisation, the flow velocity and bulk density of the powders are significantly increased. After spheronisation, the morphology of the particles changes from very irregular shape to spherical shape, the contact area between particles is small, the frictional resistance between particles is reduced, and the particles are more densely packed.
2.4 Influence of spheroidisation process on the phase composition of tungsten powder and tantalum powder
The XRD diagrams of tungsten powder and tantalum powder before and after plasma spheroidisation are shown in Figure 4. From Figs. 4(a) and 4(b), it can be seen that the diffraction peaks of tungsten and tantalum powders after spheroidisation are consistent with those of the original tungsten and tantalum powders, and the diffraction peaks are located in the positions of (110), (200), and (211) respectively, which are consistent with the standard PDF cards of tungsten and tantalum and are all body-centred cubic (bcc) structures. Table 5 shows the results of the chemical composition analysis of the original powder and spheroidised powder, which, together with the XRD analysis results, verified that no oxidation and other impurities intervened in the preparation of spherical tungsten and tantalum powders.
Table 4 Bulk density and fluidity of raw and spherical tungsten powders and tantalum powders
样品 | 松装密度/(g·cm-3) | 流动性/(s·(50 g)-1) |
原始钨粉 | 5.99±0.04 | 12.7±0.10 |
球形钨粉 | 10.63±0.06 | 5.63±0.03 |
原始钽粉 | 4.68±0.08 | 36.7±0.10 |
球形钽粉 | 8.76±0.03 | 17.6±0.20 |
Fig. 4 XRD patterns of tungsten powders and tantalum powders before and after plasma spheroidization
2.5 Verification of 3D printing of spherical tungsten and tantalum powders
The raw tungsten and tantalum powders and tungsten and tantalum powders with 95% sphericity were used as raw materials, respectively, and were shaped by the Selected Zone Laser Melting (SLM) technique, and the microstructures and densities of the printed blocks were analysed and characterised.
Table 5 Chemical composition of original and spherical tungsten powders and tantalum powders
样品 |
质量分数/% |
|||||
C |
O |
N |
H |
W |
Ta |
|
原始钨粉 |
0.001 |
0.013 |
0.001 |
0.012 |
余量 |
|
球形钨粉 |
0.001 |
0.018 |
0.001 |
0.016 |
余量 |
|
原始钽粉 |
0.015 |
0.190 |
0.001 |
0.012 |
|
余量 |
球形钽粉 |
0.016 |
0.180 |
0.001 |
0.014 |
|
余量 |
2.5.1 Microscopic morphology of tungsten and tantalum by selective laser melting and forming (SLM)
The photomicrographs of spherical tungsten and tantalum powders and raw tungsten and tantalum powders after selective laser melting are shown in Figure 5. From Fig. 5, it can be seen that a large number of metallurgical defects, such as microcracks and pores, existed on the surface of the samples prepared using raw powders under the same parameters. The positive surface images of the samples obtained by SLM moulding of raw tungsten and tantalum powders are shown in Figs. 5(a) and 5(b), respectively. It can be seen that there are a large number of cracks on the surface, and the crack distribution on the surface of the tungsten block is almost parallel to the direction of the laser scanning, whereas the cracks on the surface of the tantalum block are mainly distributed along the grain boundaries. Due to the high temperature and thermal stress in the contact area between the two lasers during laser scanning, irregular powders may have unmelted portions in the laser contact area under laser melting, and thus are prone to crack sources. Usually, the cracks will expand along the laser scanning direction, so there are a large number of cracks in each laser contact area. Due to the laser scanning process, the shape of the original powder is irregular, and the stacking is not uniform, which leads to the instability of the molten pool in the centre of the laser scanning, and there may be holes and undissolved particles, resulting in defects, which can easily generate crack sources at the weakly bonded grain boundaries under the thermal stresses caused by the fast cooling, and the temperature of the laser molten pool gradually decreases from the centre to the two sides, so the cracks will be extended along the centre of the molten pool to the two sides, and cracks will be Expansion connects multiple melt pools and expands into macroscopic cracks. The reason for the formation of holes is that the original tungsten powder has different particle sizes and shapes during the powder spreading process, and the original tungsten powder particles are large, so when scanning the morphology of the layer, the tungsten powder is not uniformly piled up during the powder spreading process, and the phenomenon of the particles not being melted occurs, which leads to the formation of holes. Figures 5(b) and 5(d) show the ortho-surface metallographies of the specimens prepared by spherical tungsten powder and tantalum powder, respectively, which show that the surface pores of the samples formed by selective laser melting with spherical tungsten powder and tantalum powder as the raw materials are fewer, with only a few small pores, and cracks basically disappeared. In the process of spherical powder laser forming, due to the small powder stacking gap, the powder spread powder uniformity, so there is basically no unmelted particles in the laser scanning process, resulting in fewer defects [25-27].
2.5.2 Densification of tungsten/tantalum by selective laser melt moulding (SLM)
The densities of bulk tungsten and bulk tantalum formed by SLM before and after spheronisation were measured, and then the densities of bulk tungsten and bulk tantalum were obtained by dividing the measured actual densities by the theoretical densities, as shown in Table 6. As can be seen from Table 6, the densities of tungsten and tantalum blocks after spheronisation are significantly higher than the densities of blocks before spheronisation.
(a) virgin tungsten powder; (b) spherical tungsten powder; (c) virgin tantalum powder; (d) spherical tantalum powder
Fig. 5 Top morphologies of SLM-ed samples with different raw powders
Table 6 Density of raw tungsten and tantalum powders and spherical tungsten and tantalum powders formed by
selective laser melting
球化前后 | 钨块致密度/% | 钽块致密度/% |
球化前 | 94.7 | 94 |
球化后 | 95.2 | 96.7 |
3 Conclusions
1) The larger the feeding rate of tungsten powder and tantalum powder, the shorter the residence time of tungsten powder and tantalum powder particles in the plasma torch, resulting in the decrease of spheroidisation rate. When the feeding rates of tungsten and tantalum powders exceeded 6 g/min and 10 g/min, respectively, the spheroidisation rates of the powders decreased sharply with the increase of the feeding rates.
2) As the spheroidisation rate of tungsten powder and tantalum powder increases, the flowability of tungsten powder and tantalum powder becomes better, and the bulk density gradually becomes larger. XRD inspection and composition analysis of spheroidised tungsten powder and tantalum powder showed that neither of them was oxidised and no other impurities were involved.
3) When the spherical tungsten and tantalum powders were shaped from virgin tungsten and tantalum powders and spherical tungsten and tantalum powders by SLM, the densities of the spherical powder shaped samples were improved under the same parameters.
References:
[ 1] JIN Yuanyuan, HE Weiwei, CHEN Binke, et al. Preparation of spherical refractory metal powders[J]. Aeronautical Manufacturing Technology, 2019, 62(22): 64-72.
[2] BAI Shuxin, NIU Dun, ZHU Li'an, et al. Research status and prospect of preparation of refractory metals by chemical vapor deposition[J]. Cemented Carbide, 2018, 35(6): 381-389.
[3] STRIGUL N, KOUTSOSPYROS A, ARIENTI P, et al. Effects of tungsten on environmental systems[J]. Chemosphere, 2005, 61(2): 248-258.
[4] MÜLLER A V, SCHLICK G, NEU R, et al. Additive manufacturing of pure tungsten by means of selective laser beam melting with substrate preheating temperatures up to 1 000 ℃ [J]. Nuclear Materials and Energy, 2019, 19: 184-188.
[5] LUO Tiegang, QU Xuanhui, QIN Mingli, et al. Dimension precision of metal injection molded pure tungsten[J]. International Journal of Refractory Metals and Hard Materials, 2009, 27(3): 615-620.
[6] RAMON H, PEETERS J R, STERKENS W, et al. Techno- economic potential of recycling Tantalum containing capacitors by automated selective dismantling[J]. Procedia CIRP, 2020, 90: 421-425.
[7] HU Quanli, PARK M R, ABBAS H, et al. Forming-free resistive switching characteristics in tantalum oxide and manganese oxide based crossbar array structure[J]. Microelectronic Engineering, 2018, 190: 7-10.
[8] BASTIN F, JANSSEN A, LOLIVIER Y, et al. Exploration of alternative routes for recycling critical metals from waste PCB and tantalum capacitors[J]. Procedia CIRP, 2020, 90:437-442.
[9] GUO Yu, XIE Kai, JIANG Wenbo, et al. In vitro and in vivo study of 3D-printed porous tantalum scaffolds for repairing bone defects[J]. ACS Biomaterials Science & Engineering, 2019, 5(2): 1123-1133.
[ 10] BALLA V K, BODHAK S, BOSE S, et al. Porous tantalum structures for bone implants: fabrication, mechanical and in vitro biological properties[J]. Acta Biomaterialia, 2010, 6(8): 3349-3359.
[ 11] ASADULLAH S, MEI Shiqi, WANG Deqiang, et al. Sulfonated porous surface of tantalum pentoxide/polyimide composite with micro-submicro structures displaying antibacterial performances and stimulating cell responses[J]. Materials & Design, 2020, 190: 108510.
[ 12] LIN Zehuan, LI Ruidi, ZHU Hongbin, et al. Microstructure and mechanical properties of Al-Mg-Sc-Zr alloy by powder feeding laser additive manufacturing[J]. Journal of Central South University(Science and Technology), 2020, 51( 11): 3055-3063.
[ 13] ZOU Yu, LIAO Xianjie, LAI Qi, et al. Research status of preparation technology of spherical titanium powder for 3D printing[J]. Materials China, 2019, 38( 11): 1093-1101.
[ 14] ZHOU Wuping, ZHANG Yingying, WANG Xuebing, et al. Preparation and application of spherical tungsten powder[J]. Rare Metal Materials and Engineering, 2019, 48(8): 2594-2601.
[ 15] LIANG Yongren, WU Yinjiang. Production technology of titanium and its alloy spherical powders used in 3D printing [J]. World Nonferrous Metals, 2016( 12): 150-151.
[ 16] LIU Jianmin, LU Xionggang, LI Qian, et al. Prospect and retrospect of fused salt electrolysis process for producing refractory metals[J]. Rare Metals Letters, 2006, 25(9): 1-6.
[ 17] SU Pengfei, LIU Zuming, GUO Yang, et al. Microstructure and solidification defect of René104 nickel-base superalloy powder atomized by argon atomization[J]. Journal of Central South University(Science and Technology), 2018, 49( 1): 64-71.
[ 18] REN Ping, ZHOU Huiqin, CHEN Xueqing, et al. Preparation of spherical or near spherical tantalum powder [J]. Nonferrous Metals(Extractive Metallurgy), 2018( 12): 43-46.
[ 19] SHENG Yanwei, HAO Junjie, GUO Zhimeng, et al. Preparation of spherical tungsten powder by RF induction plasma[J]. Rare Metal Materials and Engineering, 2011, 40( 11): 2033-2037.
[20] LU Xin, ZHU Langping, ZHANG Bing, et al. Simulation of flow field and particle trajectory of radio frequency inductively coupled plasma spheroidization[J]. Computational Materials Science, 2012, 65: 13-18.
[21] XIONG Hongbing, ZHENG Lili, SAMPATH S, et al. Three- dimensional simulation of plasma spray: effects of carrier gas flow and particle injection on plasma jet and entrained particle behavior[J]. International Journal of Heat and Mass Transfer, 2004, 47(24): 5189-5200.
[22] YE R, ISHIGAKI T, JUREWICZ J, et al. In-flight spheroidization of alumina powders in Ar-H2 and Ar-N2 induction plasmas[J]. Plasma Chemistry and Plasma Processing, 2004, 24(4): 555-571.
[23] ZHANG Haibao, BAI Liuyang, HU Peng, et al. Single-step pathway for the synthesis of tungsten nanosized powders by RF induction thermal plasma[J]. International Journal of Refractory Metals and Hard Materials, 2012, 31: 33-38.
[24] ZI Xuhui, CHEN Chao, WANG Xiaojun, et al. Spheroidisation of tungsten powder by radio frequency plasma for selective laser melting[J]. Materials Science and Technology, 2018, 34(6): 735-742.
[25] ZHOU Xin, LIU Xihe, ZHANG Dandan, et al. Balling phenomena in selective laser melted tungsten[J]. Journal of Materials Processing Technology, 2015, 222: 33-42.
[26] GALY C, LE GUEN E, LACOSTE E, et al. Main defects observed in aluminum alloy parts produced by SLM: from causes to consequences[J]. Additive Manufacturing, 2018, 22: 165-175.
[27] TENG Chong, PAL D, GONG Haijun, et al. A review of defect modeling in laser material processing[J]. Additive Manufacturing, 2017, 14: 137-147.
Reference: Plasma spheroidisation process of spherical tungsten and tantalum powders for 3D printing
If you need to know about consulting spherical metal powder, please contact :Cathie +86 13318326187(WhatsApp)