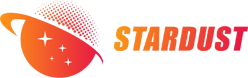
Refractory metal refers to metal materials with melting point greater than 2000℃, mainly including tungsten, molybdenum, tantalum, niobium, rhenium, vanadium and other six metal elements, as well as alloy materials based on the six metal elements [1]. Due to the high temperature performance, creep resistance, melting point and other excellent comprehensive performance and is used in aerospace, equipment manufacturing, nuclear industry and other cutting-edge fields [2-4]. Traditional refractory metal preparation methods mainly include sintering and smelting methods, however, such methods have longer production processes, lower raw material utilization and higher costs, which limit the application and development of refractory metals. In recent years, with the rapid development of additive manufacturing technology, it provides a new development idea to solve the problem of refractory metal preparation and processing [5].
Additive manufacturing is a manufacturing technology to create components with complex shapes by adding layers of powder materials. In the international standard ISO/ASTM52900, additive manufacturing is defined as the process of connecting materials from 3D model data into parts [6]. In the field of additive manufacturing of metallic materials, high-density energy heat sources such as lasers and electron beams are generally used for selective melting, and according to the classification of different energy sources, the most representative ones are selective laser melting (selectivelasermelting, SLM) [7] technology and electron beam selective melting ( Selective laser melting (SLM) [7] and electron beam selective melting (EBSM) [8]. SLM uses a laser source to input energy to melt metal powders in a selected area, and the main process parameters of this technology include input energy, scanning speed, filling space and layer thickness, and by adjusting the above parameters, nearly fully dense metal components can be obtained. EBSM has the same workflow as SLM, and the main difference with SLM is that EBSM uses an electron beam instead of a laser beam as the energy source, and the technology is known for its high-speed electron bombardment and high power density. In the manufacturing process, in order to avoid splashing when the electron beam impacts the powder, it is necessary to preheat the powder bed. During the preheating process, the scanning is completed under high electron beam flow and ultra-fast scanning rate (≥103mm/s), and the scanning speed is about several orders of magnitude higher than that of SLM. It is due to the differences in the two process parameters of input energy and scanning speed, which results in SLM and EBSM products with different microstructures and mechanical properties. Laser additive manufacturing technology has the advantages of direct and rapid, can be complex structure forming, especially for difficult to deform the material of the complex shape of the components have significant advantages, has covered a variety of fields such as aerospace, biomedical, automotive manufacturing, etc. [9-12]. Due to the high cost of rhenium and vanadium raw materials, little has been reported in recent years, so this paper outlines the latest research progress in laser additive manufacturing of four common refractory metals, namely tungsten, molybdenum, tantalum, and niobium, with a view to broadening the application of laser additive manufacturing in the field of refractory metals.
1 Tungsten and tungsten-based heavy alloys
Tungsten is a material with special inherent properties (high melting point, high tensile strength and low coefficient of thermal expansion), which can be used for high-temperature, high-heat-flow-density components in radiation environments, such as collimators, plasma components for future fusion reactors and high-performance rocket nozzles [13]. In recent years, scholars' research for additively manufactured tungsten and tungsten-based heavy alloys has focused on the two major challenges of controlling porosity and cracking, and have obtained research results with important reference values. Table 1 summarizes the latest research progress of laser additive manufacturing of tungsten and tungsten-based alloys in the past five years, which includes key information such as fabrication techniques used, performance or tissue characteristics, and application areas. It can be seen that in the laser additive manufacturing of tungsten alloys, the main technologies used are selectivelasermelting (SLM), laserpowderbedfusion (LPBF), and lasermeltingdeposition (LMD), laserdirectedenergydeposition(LDED) and laser sintering (LS). In the laser additive manufacturing research of pure tungsten, for the problem of porosity inside the sample, Xie Yanjun et al. [14] from the General Research Institute of Iron and Steel (GRIIS) analyzed the effect of SLM laser parameters on the surface morphology and internal defects of tungsten blocks, and found that the surface of tungsten blocks is flatter and the internal porosity will be reduced with the increase of laser energy density. Figure 1 shows the surface morphology of tungsten blocks prepared by SLM technology under different laser powers, and it can be seen that there are more unmelted porosity on the surface of the samples under low power.
In addition to the problem of internal porosity, cracking is also a major challenge for additively manufactured tungsten. In order to investigate the inhibition effect of additive manufacturing orientation on cracks, Li et al [15] from Tsinghua University found that extremely high thermal stresses were generated in the samples during LPBF, and defects of different degrees were produced in both parallel and vertical additive samples, where serious melting and splattering phenomena appeared in vertical additive samples, while only a small number of cracks were observed in parallel additive samples, which was attributed to the fact that the columnar crystals grown in the horizontal This is due to the fact that the columnar crystals grown in the horizontal direction are more favorable for heat conduction. In order to overcome the problems of cracks and porosity at the same time, Iveković's group at the University of Leuven [16] prepared high-density W and W-Ta parts by using the SLM process and investigated the melting and solidification behavior of tungsten and tungsten alloys under this process. It was found that cracks were always present regardless of the process parameters and scanning strategy used, however, with the addition of tantalum elements, the crack morphology became irregular and the grain size was significantly reduced. In the conventional fabrication process of W, alloying with group IV or V transition metals can inhibit crack development and improve the intrinsic plasticity. For example, Wang [17] from Tianjin University prepared W-6Ta alloy by LPBF technique and found that it contained abundant nanoscale pores in the grain boundaries of the preform, and the mechanism of crack inhibition was investigated. The results showed that the nanopores were trapped inside the grains due to the presence of a porous structure in the W-6Ta alloy, thus reducing the possibility of cracking. Later, in the cracking behavior and microstructure study of pure tungsten and tungsten-tantalum specimens [18], it was found that the number and length of cracks in W-Ta alloys were significantly reduced, the grains were refined, and a large number of dislocations were entangled with Ta oxide nanoparticles. The dislocations favor plastic deformation, while Ta removes oxygen impurities and facilitates crack reduction, as can be seen from Fig. 2, which shows that cracks are significantly reduced after the addition of 6% Ta. Guo [19] of Air Force Engineering University used SLM technology to well solve the problem of forming high-density tungsten-based alloys with large-scale complex structures and thin plate structures, and the elastic constants were calculated by tissue characterization and XRD results, which confirmed that the alloys showed almost no macroscopic or microscopic cracks. In addition, the addition of tantalum helps to improve the plasticity and formability of tungsten alloys while maintaining high density, hardness and strength, which is of great value for the application of high-density tungsten alloys. In addition to the addition of Ta element, it has been found that crack suppression can also be achieved by adding small amounts of elements such as Re and Ti. Yamamoto [20], University of Toyama, Japan, studied the cracking behavior and microstructure of tungsten-rhenium (W-Re) alloys prepared by the LPBF method, and found that the columnar grains were elongated along the fabrication direction and gradually refined as the rhenium content increased.
In recent years by using solid solution strengthening and secondary phase nanoparticle dispersion strengthening to make the reinforcing phase combined with the solid solution of additively fabricated tungsten, the strengthening of the substrate and the inhibition of cracking can be realized simultaneously [17,29]. Chen Jinhan [21] of Tsinghua University used in situ reaction to form the reinforced phase to improve the cracking problem occurring in tungsten blocks prepared by LPBF, and low alloy tungsten blocks of tungsten-tantalum carbide (5%) were successfully prepared using LPBF technology. It was found that the holes in the specimens were reduced and the cracks were also significantly reduced, and it was also demonstrated that the intrinsic strength of the material was significantly improved after the addition of tantalum carbide. The group then analyzed the role of carbide in influencing the additively manufactured tungsten, and it was found in the study [22] that the crack density of the alloy would be significantly reduced by the addition of TaC, and the W(Ta) solid solution and intercellular tungsten carbide (W2C) formed different morphologies of the cellular structure at different locations compared to pure W, which provided an effective way of refining the W organization. Fig. 3 shows the crack distribution and internal microstructure of pure tungsten and W-5% TaC, and it can be seen that the cracks of W-5% TaC are more disordered and the density is reduced compared with pure W.
Elemental iron has also been chosen as an additive to conventional tungsten alloys to effectively inhibit pore formation in tungsten-based alloys, which are often used in the first wall of fusion reactors to extend their service life [27-28]. Li [23] from the Northern Polytechnic University found that the organization of the W-20% Fe alloy prepared by the LMD method consisted of W, Fe and Fe7W63 phases.Fe7W6 was distributed around the tungsten phase in the form of shells or in the form of fragments in the Fe matrix, and it was the formation of the Fe7W6 phase and the tungsten dendrites that significantly increased the hardness and brittleness of the tungsten alloy. The laser process parameters are also critical in determining the internal microstructure and defects, and it is essential to study the effect of laser process parameters on the quality of 3D printing. Sun [24] of Nanjing University of Aeronautics and Astronautics studied the effects of laser process parameters on the thermal behavior, melting/solidification mechanism and tissue evolution of W-20%Fe alloys during the LMD process, and a three-dimensional finite element model was established based on the consideration of temperature-dependent thermophysical properties. The results show that the cross-sectional structure of the melt pool becomes deeper with the increase of laser power, and columnar dendrites and equiaxed dendrites are formed at the bottom and top of the melt pool, respectively.
Tungsten-based heavy alloys (WHAs) are composite materials consisting of a hard tungsten phase and a matrix phase γ (W-Ni-Fe/Cu) [30-31].WHAs are used in aerospace, weaponry, electrical and electronic, and nuclear industries due to their properties such as high density, high ray-absorption capacity, and high hardness [32-33]. For example, such as gyroscope rotors, counterweight and vibration damping materials for aerospace, armor-piercing bullet cores for conventional weaponry, and thermonuclear fusion test materials [34-35]. The traditional powder metallurgy technology has the advantages of low cost, high raw material utilization, high production efficiency, energy saving and environmental protection, and can directly produce high-performance products with unique shapes, and can even achieve near-net molding of materials, but at present, the powder metallurgy products still have the problems of high impurity content and part of the porosity can not be completely eliminated, which seriously affects the performance of the products' practical applications [36-37]. However, the fabrication of tungsten-based heavy alloys (WHAs) using direct 3D printing technology is still immature, so in recent years, many scholars have carried out a lot of exploratory work around the control of defects and densification of 3D printed tungsten-based heavy alloys. Wang [25] of California Polytechnic University used laser sintering (LS) technology to study the effect of process parameters on the densification of 90W-7Ni-3Fe, and found that the laser power and scanning speed were the most critical parameters, and the pores were changed from open pores to closed pores with the increase of the laser energy, and the tungsten was not melted but dissolved in the NiFe matrix during the sintering process, and the rearrangement and the dissolution-re-precipitation mechanism were both the the reason for densification. In order to solve the problem of difficult machining of W-Ni-Cu alloys with complex shapes, Wang [26] from Central South University used the SLM process to strengthen the W-10Ni-10Cu composite powders, and found that an amorphous W-Ni solid-solution phase was detected in the SLM-treated samples, which was induced by the migration of Marangoni, and that the Ni-Cu phase tends to break up the liquid W into small particles to form nanocrystals. Wei [27] from Nanchang University prepared 90W-7Ni-3Fe alloy by laser direct energy deposition (LDED) technique and found that the microstructure of the sample showed obvious non-homogeneity along the fabrication direction.The hardness of the matrix phase and the W particles in the LDED samples was higher than that of the liquid-phase sintered samples, and this basic understanding will provide a basis for the improvement of the mechanical properties of the additively fabricated tungsten-based heavy alloys and the optimization of the post-treatment . The mechanical properties of laser additively manufactured samples can be enhanced by using an optimized post-heat treatment process. Wei [28] of Central South University used an optimized post-heat treatment process to prepare a high-performance laser-sintered 90W-7Ni-3Fe alloy, in which W particles were involved in matrix-phase coordinated deformation, improving the interfacial bonding strength and the ductility of matrix-phase coordinated deformation. In addition, it was found that a short cycle heat treatment could lead to a simultaneous increase in strength and plasticity of the as-cast specimens. Figure 4 shows the representative engineering stress-strain curves and room temperature tensile properties (YS, UTS, and EL) of the three specimens, which show that the ultimate tensile strength and elongation have been improved after the two heat treatments (HT1 and HT2).
2 Pure molybdenum and molybdenum-silicon-boron alloys
Due to the molybdenum's difficult to process and high material loss, so that its production and development is subject to certain restrictions, and through the use of additive manufacturing technology can avoid thermo-mechanical processing and reduce the secondary processing, with shorten the manufacturing cycle, improve production efficiency advantages. In the last five years the research of laser additive manufacturing molybdenum and molybdenum alloy focuses on pure molybdenum and molybdenum-silicon-boron alloy. Braun [38] of the University of Innsbruck, Austria, studied the process of molybdenum and tungsten melting by SLM technology and found that the cause of cracks and residual porosity in SLM-treated molybdenum and tungsten is the presence of oxygen impurities, and the oxygen is polarized at grain boundaries in the form of molybdenum/tungsten oxide, which leads to thermal cracking. Rebesan [39] at the National Institute of Nuclear Physics, Italy, prepared pure molybdenum blocks with a relative density of 99.5% by adjusting the process parameters of LPBF and verified that the Vickers microhardness of the fully dense specimen, HV0.15 (2077.6 ± 176.4 MPa), was similar to that of commercial molybdenum. Carbon improves the plasticity and grain boundary strength of molybdenum, and the scientific consensus on this phenomenon is that carbon either displaces oxygen impurities at grain boundaries or inhibits oxygen diffusion into grain boundaries. In order to elucidate the mechanism of carbide interaction with oxygen impurities and the molybdenum matrix, the Kaserer research group at the University of Innsbruck has successively carried out extensive research work on reducing porosity and the number of cracks in laser additively fabricated molybdenum alloys by adding carbon to simultaneously increase the plasticity and grain boundary strength of molybdenum. The group first used the new concept of alloying molybdenum powder to process molybdenum with the mechanical properties of powder metallurgical materials using the SLM method. It was found that molybdenum alloying with the addition of 0.45% mass fraction of carbon leads to tissue supercooling, which leads to a shift in the solidification mode of the material from planar to cellular, and this organizational shift can lead to an increase in densities, hardness, and flexural strength [40]. Subsequently, the group prepared molybdenum alloys with a carbon mass fraction of 0.45% in the LPBF additive manufacturing process, and identified the carbides as orthorhombic crystals ζ-Mo2C, with ζ-Mo2C at a semi-coherent interface with α-Mo. No cracks were detected at the α-Mo/α-Mo interface or at the α-Mo/ζ-Mo2C interface. pure molybdenum produced by the LPBF process has an epitaxially grown, coarse, columnar crystalline structure with large cracks at angular grain boundaries, which were embrittled by oxygen polarization [41]. In order to investigate the effect of carbon content on the mechanical properties of laser additively manufactured molybdenum alloys, the group studied the grain size, tensile strength and hardness of five different molybdenum-carbon alloys [42]. The results showed that grain refinement at high carbon content was attributed to an increase in thermal and structural subcooling. Subcooling permits particles to nucleate and grow on the underlying solidification layer, with the fastest growth direction being closer to the thermal gradient than the epitaxially grown grains, and it is evident from Fig. 5 that the porosity and the number of cracks decreases with the increase in carbon content [42].
Molybdenum-silicon-boron (Mo-Si-B) alloys have good high-temperature mechanical properties, high creep resistance, and excellent oxidation resistance, and thus are considered as one of the alternatives to nickel-based high-temperature alloys in engines [43-44]. Currently, there are 2 main methods to prepare Mo-Si-B alloys: arc melting and powder metallurgy [44]. Arc melting has the advantages of simple equipment, low energy consumption, and instantaneous synthesis. However, voids and microcracks may occur in the prepared materials. In contrast, the Mo-Si-B alloy prepared by powder metallurgy has fewer microcracks and a relatively homogeneous organization, and it exhibits high strength at room temperature and even at 1200°C, but it may contain many cavities with high oxygen content [45]. Additive manufacturing technology allows the integration of complex cooling structures, which not only leads to superior materials for turbine blades, but also to more efficient cooling systems for turbine blades. This combination of optimized materials and improved cooling systems will lead to significant increases in operating temperatures, which will significantly improve the efficiency of modern gas turbines [46]. Laser additively fabricated Mo-Si-B alloys have a more complex phase composition structure which will play a decisive role in the material properties, and therefore the interactions between the phases after laser additive fabrication must be thoroughly investigated. Makineni [47] at the Max-Planck-Institut in Germany found in the solidification organization of laser additively manufactured Mo-Si-B alloy materials that the main phase is the dendritic α-Mo phase, and the mixed phase between dendrites is Mo5Si3(T1)+Mo5SiB2(T2) instead of the expected equilibrium phase Mo3Si+Mo5SiB2(T2), and that such a combination of phases improves the creep properties, and that the creep properties of these materials are improved. It was also demonstrated that the successful dispersion of oxide particles mainly among the dendrites led to a higher indentation fracture toughness. The feasibility of printing Mo-Si-B powder materials using the LMD process was demonstrated for the first time by Schmelzer [48] at the University of Magdeburg, who conducted a detailed analysis of the printability and microstructure evolution of the prepared multiphase Moss-Mo3Si-Mo5SiB2. The results show that the hardness of the LMD-processed material is comparable to that of Mo-Si-B alloys produced by powder metallurgy (PM). The first systematic study of the process of manufacturing high melting point near-eutectic Mo-Si-B alloys using LPBF was carried out by Fichtner [49] at RWTH Aachen University, Germany, where the near-eutectic Mo-Si-B alloys were aerosolized and the powders were analyzed to determine the suitable process parameters for the preparation of crack-free samples. In terms of mechanical properties, the toughness-brittle transition temperature and creep rate at potential application temperatures were determined. Ma [50] of Xi'an Jiaotong University investigated the effects of SLM parameters on the relative density and sample defects of Mo-Si-B alloys through orthogonal tests, and found that the layer thickness had the greatest effect on the relative density, followed by laser power and hatch spacing, and the scanning speed had the least effect on the relative density. By adjusting the SLM parameters, dense Mo-Si-B samples with relative densities greater than 99% can be obtained. In addition, there are a large number of intergranular cracks in Mo-Si-B alloys under SLM, and these cracks can be regulated by substrate preheating. As can be seen from Fig. 6, the compressive strength of the specimen increases with the increase of the substrate preheating temperature, and importantly, the cracks in the horizontal cross section almost disappear when the substrate is preheated at 400°C. The reduction of cracks improves the compressive properties of the specimen to a certain extent.
3 Niobium-silicon and niobium-titanium alloys
Niobium-silicon based alloys have been considered to replace nickel-based high-temperature alloys as hot-section materials for the new generation of aero-engines due to their high melting temperatures (>1750 °C), relatively low densities (6.6-7.2 g/cm3), high high-temperature strengths and good creep resistance [51]. However, the limited plastic deformation capability and lower room temperature fracture toughness are one of the bottlenecks that currently limit their applications. With the development of laser additive manufacturing, laser additive manufacturing of Nb-Si and Nb-Ti system alloys has gradually come into the limelight. Laser power is currently a hot issue in the study of laser process parameters of Nb-Si system alloys for additive manufacturing. Goncharov [52] of St. Petersburg Polytechnic University used mechanically alloyed powder as raw material and LMD technology to laser process metal samples at different laser powers, and found that the microstructures of samples under 500 W laser power consisted of solid solutions of Nb, Nb3Si, and Ti dendritic chains; when the laser power was increased to 1400 W, Ti dissolved in Nb, the dendritic chains disappeared, and Nb5Si3 silicides were stabilized. Liu Wei et al [53] from Beijing Institute of Aeronautical Materials carried out a detailed study on the microstructure and phase composition of Nb-16Si alloys prepared by LMD technology, and found that the laser power does not significantly affect the phase composition, and the formation of the substable Nb3Si phase and NbSS (niobiumsolidsolution) phase is due to the in-situ reaction of silicon powder and niobium powder under the action of high-energy laser beam. in situ reaction occurred. Figure 7 shows the microstructures of Nb-16Si alloys prepared under different laser powers, and it can be seen that the NbSS+Nb3Si eutectic and pre-eutectic NbSS phases in Nb-16Si alloys were refined with the increase of laser power.
Nb-Ti system alloys due to its biocompatibility and low elastic modulus, it can be used in the medical field [54-55]. Guzmán [56], University of São Paulo, prepared four samples of Nb-47Ti alloys with different scanning strategies using the LPBF process and combining plasma atomization (PA) and hydride dehydrogenation (HDH) and compared the interstitial element content, and found that the melts and the cellular dendrites formed a similar organization in the phase matrix with body-centered cubic (bcc) structure. University of São Paulo deMouraNobre [57] used the LPBF process to increase the Young's modulus of metallic biomaterials by controlling the laser power and scanning speed parameters. Weave analysis showed that the higher the laser power and scanning speed, the more pronounced the surface near-cubic weave and the smaller the Young's modulus.
4 Tantalum porous metal for medical use
Tantalum has good biocompatibility and is an important metal material for medical use. Laser additive manufacturing technology has become a research hotspot in the field of pure tantalum material fabrication due to the advantages of rapid, near-net forming of complex parts. Biocompatibility is a core issue to be solved for medical porous tantalum. Balla's group [58] at Washington State University used laser near-net-shaping technology to fabricate porous tantalum with relative densities ranging from 45% to 73% by adjusting the design porosity and confirmed that porous tantalum has a better cellular adherence and propagation ability than porous titanium. Subsequently, the group compared the biocompatibility of laser additively fabricated porous Ta and Ti6Al4V (Ti64) and found that porous Ta and surface-modified porous Ti64 implants had comparable performance for early osseointegration via seamless osteomaterial interlocking at 5 weeks after implantation, whereas porous Ta had sustained and prolonged efficacy in terms of bone formation at 12 weeks postoperatively [59]. To improve the osteointegration performance, Bandyopadhya [60] at Washington State University successfully deposited a tantalum coating on a titanium surface using the LENS technique, and the Ta-coated surface showed good cell adhesion and growth with abundant extracellular matrix formation compared to the Ti surface. However, these dense Ta coatings will not withstand low fatigue resistance due to the pores and the lack of a sharp interface between the coating and the substrate, which is a major problem for porous coatings used to enhance early biological immobilization. Wauthle [61] at the University of Leuven first fabricated porous tantalum samples using SLM technology, and the mechanical properties of porous tantalum were tested and found to be very close to those of human bone. Compared with the porous Ti-6Al-4V structure, the porous tantalum fabricated by SLM has excellent osteoconductive properties with high normalized fatigue strength and high ductility. Figure 8 shows a porous tantalum material for medical use fabricated using SLM technology. In order to verify the stability of porous tantalum implanted prosthesis, DeMartino et al [62] of New York Hospital for Special Surgery conducted a clinical follow-up of standard porous tantalum implanted in artificial hip joints for 15 years, which fully verified the stability of porous tantalum implanted prosthesis.
Important progress has also been made in laser additive manufacturing of porous tantalum materials for medical use in China. Zhou et al [63] from Central South University found that when printing pure tantalum materials using SLM, they found that too fast a laser scanning rate would lead to the formation of micropores inside the material, while too low a laser scanning rate would cause microcracks between layers. Guan [64] of the Northern Polytechnic University used the LMD process applied to the preparation of tantalum powders with two different interstitial element contents and investigated the microstructure and mechanical properties of the LMD specimens. The results showed that the tantalum samples had large columnar grains that were close to fully dense, with the growth direction slightly deviating from the deposition direction, and the hardness of tantalum fabricated by LMD was as high as 2940 MPa, which was mainly attributed to the solid-solution strengthening of the interstitial elements nitrogen and oxygen. Li Yang et al [65] from Soochow University used SLM technology to prepare porous metal materials such as porous tantalum, porous titanium alloy and porous 316L stainless steel for medical use, and subsequently found that the cell proliferation ability on the surface of porous tantalum was stronger than that of other porous medical materials after comparing the biological properties of various porous materials. Yang Liu [66] and others completed the world's first additive manufacturing personalized porous tantalum metal cushion implant total knee revision surgery. Chongqing Runze Medical Co. Ltd. used SLM technology combined with high-temperature sintering to fabricate porous tantalum to satisfy the implant [67-68].
5 Summary and Prospect
Laser Additive Manufacturing (LAM) technology is one of the hot directions for the preparation of refractory metals due to its advantages of high efficiency, rapidity, short production cycle and green processing. However, due to the short development history of laser additive manufacturing technology, there are still problems such as high manufacturing cost, unstable process, lack of systematization and standardization, which still restrict the application of laser additive manufacturing in the field of refractory metals. This paper describes the application of different laser additive manufacturing technologies on refractory metals, especially summarizes the latest research results in the past 5 years, and draws the following conclusions:
(1) Laser additive manufacturing technology provides new development ideas for manufacturing complex components of refractory metals, and has made great progress in manufacturing tungsten and tungsten-based heavy alloys, pure molybdenum and molybdenum-silicon-boron alloys, niobium-silicon and niobium-titanium alloys, and porous tantalum.
(2) laser additive manufacturing refractory metal maturity is still lacking, including process and equipment, especially in the crack suppression and reduce porosity two major problems still need systematic and in-depth research to solve the problem for the promotion of large-scale industrial applications have a great role in promoting.
(3) Reduce raw material costs and manufacturing costs is still the main direction of the development of laser additive manufacturing technology, especially for medical porous tantalum materials, the need to control the quality of raw materials and short process processing two aspects of in-depth basic research, to achieve the purpose of reducing costs, so as to benefit more patients.
(4) laser additive manufacturing refractory metals there is a huge potential for development, with the optimization and upgrading of additive manufacturing equipment, will greatly enhance the production efficiency and accuracy of the product, in which the laser additive manufacturing and other technologies can be combined to achieve twice the result with half the effort, which may also be the focus of the future direction of development of laser additive manufacturing technology.
Reference:Chinese graphic method classification number: TG 146.4+ 1
Literature identification code: A
Article Number: 1002-185X(2023)05-1943-11
Stardust Technology focuses on the preparation of rare and refractory metal powders, and adopts RF plasma spheronization technology to efficiently spheronize the metal powders, which significantly improves the fluidity and loose loading density of the powders. Through laser additive manufacturing technology, the spherical powder can realize high-precision, high-performance molding of complex parts, especially suitable for aerospace, medical implants and other high-end fields.
Relying on the self-developed RF plasma system, the company is able to handle refractory metals such as tungsten, tantalum, molybdenum, etc. The powder has a high degree of sphericity and low oxygen content, which meets the consistency and reliability requirements of materials for additive manufacturing. Stardust is committed to providing high-quality metal powder solutions for industrial-grade 3D printing and promoting the development of cutting-edge manufacturing technology.