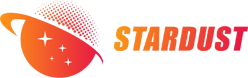
1.Introduction
Molybdenum (Mo) is a silver-grey colored metal with a high density of 10.22 g/ , and a high heat resistance due its melting point of 2610 °C,giving it excellent high temperature mechanical properties. This has made it a frequent choice for components used in crystal growing furnaces or crucibles intended for ultra-high temperature use [1], where the high creep resistance of Mo is critical to ensuring a long service life.
Most research on the high-temperature creep has so far focused on superalloys based on austenitic stainless steel, nickel (Ni) and cobalt (Co), which are often used as the main material in aircraft turbines,rockets and jet engines. Due to such excellent properties, researches on the superalloys in high-temperature industrial fields are actively performed [2,3]. Studies have been conducted on ultra-high temperature metals containing refractory metals such as niobium (Nb), tantalum (Ta), tungsten (W) and rhenium (Re), but these have tended to focus on their creep characteristics in the medium temperature range of 0.4-0.5 times the melting temperature of the metal (Tm) [4,5]. However, high-temperature creep deformation has been observed in iridium metal at ultra-high temperature ranges nearer to 0.9 Tm [6]. And the creep microstructures of these refractory metals are related to their recrystallization behaviors. Most researches on the commercial pure molybdenum are concentrated on the recrystallization behaviors, but the studies on the creep related microstructural change are little investigated.
Pure refractory metals have a higher melting point than alloys, and so are extensively used in high-temperature components. However,due to weak physical properties and peculiarities of usages of such metals, researches on high-temperature deformation behaviors above 0.7 Tm temperatures are limited. The characteristics of creep deformation at a high-temperature of 1720 °C (0.66 Tm) have been reported [7], but there has been insufficient attention given to creep at ultrahigh temperatures close to 2000 °C.
In this study, an ohmic joule heating creep tester is used to examine the creep characteristics of pure commercial molybdenum in the ultrahigh temperature range (0.61-0.77 Tm), and the creep deformation characteristics is investigated by selecting load and temperature as creep parameters. Since the secondary recrystallization of Mo occurs at a temperature of around 2000 °C, the microstructural changes of molybdenum sheet after the high-temperature creep testing are examined.
2.Experimentalmethod
A creep tester was produced by applying a single lever and raising the temperature of the sample through ohmic heating by connecting it directly to a power supply [8]. All tests were conducted under Argon (Ar) atmosphere and the temperature of the specimen was controlled using an optical pyrometer (IR-CAQ2TN, CHINO). Two commercial Molybdenum sheets were used, each with a purity of 99.995 wt.% but different concentrations of impurities, as determined by Glow Discharge Mass Spectrometry (Table 1). The oxygen and carbon content of each sheet was measured using ELTRA ON 900 and ELTRA CS 800 equipment.The Mo-A sheet (Plansee, Austria) was manufactured by compacting band sintering with Mo powder and hot-rolled to a thickness of 3.6 mm, then cold-rolled to 1.0 mm thickness [9]. The Mo-B sheet was sourced from a Chinese company, and though no details of its manufacturing process are available, it is believed to have undergone a very similar deformation process to that of the Mo-A sheet. Individual specimens with a gauge length of 30 mm, width of 6 mm and thickness of 1 mm (Fig. 1(a)) were obtained by electro-discharge wire cutting of the sheets. Any surface oxidation was then removed by sand blasting with glass beads (50-105 μm). The actual temperature distribution at the grip and gauge area is shown in Fig. 1(b). Fig. 1(c) shows the changes in cross-sectional micro-Vickers hardness along the specimen after creep testing, which was measured using a microhardness tester (FM-7, FUTURE, Korea) with a normal load of 100 g and a dwell time of 10 s. The hardness value of approximately 300 Hv at the grip is identical to the initial hardness, but in the gauge section where the target temperature was reached, this decreased to ~200 Hv.
The creep test was conducted using constant initial loads of 5, 10 and 20 MPa at a fixed temperature of 1800 °C, and with an initial load of 10 MPa at 1600, 1800 and 2000 °C. All tests were conducted in the rolling direction (RD) of the specimen. Resistance joule heating was used to reach the target temperature in 2 s, and this was maintained until fracture. Creep displacement was recorded using a linear gauge along with the change in temperature. The load applied is assumed to be constant given that the change in the cross-section of the sample during creep test is insignificant. To observe the change in the microstructure after creep test, eachspecimen was cut in its gauge area and a longitudinal cross-section
was polished using SiC paper (#400-#4000) followed by a ~1 μm diamond suspension (ALLIED). These specimen cross-sections were etched by Murakami's reagent, which was produced by diluting a 10 wt.% KOH solution and 10 wt.% K3Fe (CN)6 solution. The microstructure was then observed using optical microscope (OM, Nikon Epiphot-200BD) and
scanning electron microscope (FESEM, FEI Quanta 200F).
3.Resultsanddiscussions
Fig. 2(a) and (b) show the initial, as-received microstructure of the Mo-A and Mo-B sheets, in which we see a typical as-rolled fibrous microstructure extended in the rolling direction with layered deformation structures. These initial microstructures are very similar, and show a similar degree of deformation to achieve full density. In the previous report [10], the degree of deformation shown in Fig. 2 can be considered as being above 68%. Initial as-rolled surface EBSD images of the two Mo sheets in Fig. 2(c) and (d) reveal that Mo-A had a more random grain orientation, whereas Mo-B had a preferred orientation of ⟨001〉// ND grains. The grain size of the Mo-A sheet is also smaller than that of Mo-B sheet. The room temperature mechanical properties of the two Mo sheets are also presented in Fig. 2, and this shows that both have nearly the same tensile strength. However, the Mo-B sheet does exhibit a slightly higher tensile strength with a lower elongation when compared to the Mo-A sheet. The micro-Vickers hardness of the two Mo sheets in Fig. 2 shows a uniform distribution along the thickness direction.
Fig. 3 presents the displacement-time creep curves obtained from the rolling direction of the Mo-A sheet at 1800 °C, under different loads. Under a load of 20 MPa, there is an abrupt change from primary creep to third-stage creep without any intermediate steady-state creep stage. In contrast, the steady-state creep was maintained for a certain period of time at 10 MPa, with its duration increasing with a constant load of 5 MPa. The duration of the third creep stage, the acceleration stage, also increased with a decrease in load. The steady state creep strain rate at 1800 °C increased from 7.34 × 10-6 to 2.83 × 10-5 and 1.53 × 10-4 s -1 with increasing creep stress. In case of creep tests conducted at a temperature of 0.5 Tm, it has been reported that the creep rate is dependent on the rate at which dislocations move to pass the barrier [11]. As the creep deformation of pure Mo at this temperature shows steady-state creep under loads of 5 and 10 MPa, and it is considered that the strain hardening is balanced by the dynamic recovery produced by dislocation annihilation under these conditions.
In the cross-sectional microstructure of the crack tip produced in Area 1 of the Mo-B sheet after creep testing in the rolling direction at 10 MPa and 1800 °C shown in Fig. 4(a), most grains near the crack tip are secondary recrystallized grains. Some small primary recrystallized grains can also be observed along with cracks formed at the recrystallized grain boundaries. Fig. 4(b) is a photograph showing the microstructure in Area 2 of the Mo-B specimen, in which secondary recrystallized grains are so large that they are nearly equal in size to the thickness of the specimen. In the photograph of Area 3 in the MoB specimen shown in Fig. 4(c), small primary recrystallized grains can be seen near the grip due to the lower temperature than the target creep temperature. The image in Fig. 4(d) shows the appearance of the specimen after the creep test from which the different areas were define; i.e., Area 1 is the crack tip where fracture occurs, Area 2 is the region where secondary recrystallization is observed, and Area 3 is where primary recrystallized grains are observed. Thus although, the creep deformation is accompanied by secondary dynamic recrystallization in the gauge area, near the grip very fine primary recrystallized grains are also found. The length of the secondary recrystallization area is therefore considered to be dependent on the time to creep rupture for a given creep temperature and stress.
The image in Fig. 5 shows the microstructure of the Mo-A sheet in Area 1, 2 and 3 after creep testing at 1800 °C under different stresses. The photos of Area 1 in Fig. 5(a), (b) and (c) show the crack tips of creep ruptures and localized necking of the specimen, while the photos of Area 2 in Fig. 5(a), (b) and (c) show the secondary recrystallized microstructures. The photos of Area 3 in Fig. 5(a), (b) and (c) show that these recrystallized areas vary in length with creep rupture time. Fig. 5(a) shows coarse grains caused by secondary recrystallization in Area 1, 2 and 3, with subgrain traces present within the secondary recrystallized grains due to the high strain rate that is induced during necking. The small grains located between the large secondary recrystallized grains in Fig. 5(b) indicate that secondary recrystallization progressed from the surface to the interior of the specimen, leaving smaller primary recrystallized grains in the outer surface of the specimen in Area 1 and 2. Creep rupture took approximately 11 h and 32 min at 5 MPa in Fig. 5(a), which is thought to be sufficient time and temperature for secondary recrystallization to occur. In Fig. 5(b), rupture takes a much shorter time of approximately 1 h and 13 min. At 20 MPa, as shown in Fig. 5(c), coarse grains are produced by secondary recrystallization in Area 1. Meanwhile, in Area 3, an interface is produced between the primary and secondary recrystallization. Since creep at 1800 °C under 20 MPa exhibited an early transition to the acceleration stage without a steady-state stage, and ruptures in a very short time, it is considered that the duration time at creep temperature for the occurrence of dynamic recrystallization is insufficient and the length of secondary recrystallized area is very short in the gauge area. It is reported that, in molybdenum, the dynamic secondary recrystallization occurs at a temperature of approximately 1540 °C during plastic straining [12].
Fig. 6 shows the optical microstructure of the Mo-B sheet after creep testing at 1800 °C under different stresses. The case of 5 MPa in Fig. 6(a) shows the necking caused by creep deformation in Area 1and the coarse grains caused by secondary recrystallization. However, in the case of 20 MPa in Fig. 6(b), Area 1 exhibits a brittle fracture crack tip and cracks at the grain boundaries. In other words, when compared with the Mo-A sheet shown in Fig. 5, Mo-B is more susceptible to intergranular brittle fracture. The primary and secondary recrystallized grains in the Mo-B sheet are also smaller than those in Mo-A, and small primary recrystallized grains are observed between the large secondary recrystallized grains in Area 1, 2 and 3. As body centered cubic refractory metals such as Mo are well known to suffer brittleness at their grain boundaries due to primary recrystallization, brittle fracture is believed to occur in Mo-B at the grain boundaries of the primary recrystallized grains.
Following creep test, the specimens were intentionally fractured near the grip area to observe the morphology of the primary recrystallized grains. Fig. 7 presents SEM images and EDS chemical analysis results obtained from the fractured surface of Mo-A and Mo-B at Area 3. Note that a film-like phase with a higher oxygen peak was observed at the intergranular boundaries, suggesting that a film of molybdenum oxide (MoO2 or MoO3) was formed. Furthermore, this grain boundary oxide film is more prevalent in Mo-B than in Mo-A. Interstitial impurities with low solubility in Mo such as oxygen and nitrogen are known to accelerate intergranular embrittlement [13,14], and so the brittle fracture that occurred in the Mo-B sheet after creep testing was most likely caused by grain boundary embrittlement due to oxygen segregation [15].
A formula for calculating the minimum rate of creep strain for a pure metal can be determined by using the Sherby-Dorn Equation [16], in which it is assumed that the stress exponent (n) is constant at a given temperature. This allows a power-law to be established for the minimum creep rate against stress, from which the stress exponent was obtained for the Mo-A and Mo-B sheets. Fig. 8(a) provides a log-log plot of the steady-state strain rate against the stress applied to the Mo-A and Mo-B sheets. Note that if this is drawn using data acquired by the partial least-squares method, the slope of the line becomes the stress exponent (n). Using this, the stress exponent of the Mo sheets was estimated to be
3.85-3.98. The steady-state creep behavior of bcc metals such as Mo is known to show an approximate power-law-creep over a specified temperature and stress regime [17], and the creep mechanism of this is the dislocation climb under 0.6 Tm or above. However, pure Mo typically has a stress exponent of 5 [18], which is somewhat higher than the value
found in this study. It is possible that creep under lower stress could be involved with diffusional creep or grain-boundary sliding creep,and that small primary recrystallized grains near the grip area could involve as a grain boundary sliding creep with lower stress exponent.That is, as some minor solute and interstitial atoms can interact with dislocations, a minor dragging force might be exerted on the movement of dislocations [19].
The graph in Fig. 8(b) shows the minimum creep strain rate against the change in temperature, and as the slope is expressed as - Q/R, the activation energy for creep deformation (Q) can be obtained. This reveals that the activation energy for creep deformation is 412.9 kJ/mol in Mo-A, but 362.2 kJ/mol in the case of Mo-B. In comparison, the activation energy for self-diffusion in Mo is known to be 405.7 kJ/mol [20]. Since the creep activation energy of Mo-A is nearly the same as the self-diffusion energy, there must be smaller solute atoms included in the Mo-B sheet to account for the lower creep activation energy.
4. Conclusion
Creep tests of Mo sheets conducted with different loads (5, 10 and 20 MPa) at 1800 °C and at different temperatures (1600, 1800 and 2000 °C) under a constant load of 10 MPa have revealed that low loads and temperatures produce coarse secondary recrystallized grains through dynamic recrystallization that increase the fracture time to 10 h or more. At higher temperatures and loads, the fracture time is too short for secondary recrystallization to occur, as these grains are only partially observed on the crack tip. The Mo-B sheet has smaller primary and secondary recrystallization grains than the Mo-A sheet with a coexistence of both primary and secondary recrystallization grains. As a result of this difference, Mo-A undergoes ductile fracture, whereas Mo-B experiences brittle fracture at its grain boundaries. This brittle intergranular fracture of Mo-B is considered by an embrittlement of the primary grain boundaries due to the formation of a molybdenum oxide film. The steady-state creep strain rate at 1800 °C is obtained as from 7.34 × 10-6 to 2.83 × 10-5 and 1.53 × 10-4 s-1 with 5, 10 and 20 MPa load, respectively. The two Mo sheets tested had an estimated stress exponent (n) of 3.85-3.98, but differed in creep activation energy, indicating that Mo-B contains smaller solute atoms.
Citation information
Int. Journal of Refractory Metals and Hard Materials 60 (2016) 52–57
Stardust uses radio frequency plasma to spheroidize molybdenum powder, which has high purity, low oxygen content, high sphericity, smooth surface, no satellite balls, uniform particle size distribution, and excellent flow properties.
Widely used in contact materials, aerospace high temperature resistant components, target materials and other fields.
Spherical molybdenum powder is suitable for laser/electron beam additive manufacturing, laser direct deposition, hot isostatic pressing, injection molding, laser cladding and other processes. The particle size can be customized to meet the needs of customers in different fields.https://www.stardustpowder.com/spherical-pure-mo-powder
For more details, please contact Vicky at +86-13318326185