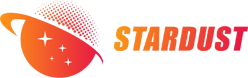
Metal injection molding (MIM) technology is a new type of powder metallurgy near-net forming technology that has developed most rapidly in the world in recent years. Its advantage is that it can directly form various complex shapes of metal parts at one time, just like forming plastic parts. In addition, since it is formed by fluid flow filling the mold cavity, the density of each part of the part is uniform, and there is no density gradient phenomenon that is inevitable in the traditional powder metallurgy pressing-sintering process (P/S—Press/Sinter). And because waste materials can be reused, the material utilization rate is almost 100% [1.2].
Tungsten-based heavy alloy parts are widely used in military, medical and scientific experimental equipment. With the advancement of technology, various departments have more and more complex requirements for the shape of tungsten-based heavy alloy parts, and the processing difficulty is increasing, and the production cost is high. Metal injection molding technology can solve this problem. Due to the small particle size of tungsten powder, the MIM process does not need to increase the powder cost. Compared with the injection molding of low-alloy steel, stainless steel and other materials, it has a unique raw material cost advantage. In this study, the injection molding method was used to prepare the back core and tensile specimens, and the process and material properties were analyzed and measured.
1 Experimental process
1.1 Raw materials
The metal powders used were W powder, Ni powder, and Fe powder, and the mass ratio of W, Ni, and Fe was 97:2:1. The binder was mainly polystyrene and polypropylene, and a small amount of active substances were added. The properties of the raw powder and the binder are shown in Tables 1 and 2 respectively.
1.2 Experimental process
First, the W, Ni, and Fe powders were pre-mixed in a V-type mixer for 8 hours, and then the powders were mixed with the binder for 4 hours, and the powder loading was 47.8% (volume fraction); the feed was granulated and extracted to remove polystyrene, the quenching time was 2 to 3 hours, and the solvent temperature was 50°C; then it was dried, thermally degreased, and pre-sintered, and the whole process was about 2 to 3 hours; finally, it was sintered in a molybdenum wire furnace at 1530°C for 2 hours. Two parts were prepared by this process, one is the standard tensile specimen of the American MIM Association, and the other is the rear core of a double-headed pistol bullet.
2 Results
2.1 Rheological properties of feedstock
The viscosity of the feedstock at different temperatures and rheological rates was measured by an Instron 3211 rheometer. The capillary diameter was 12.7 mm and the length was 76.2 mm. The pressure head rate was changed to obtain different load values, which were then converted into viscosity. The experimental results are shown in Table 3.
2.2 Mechanical properties of the specimen
The standard tensile specimen was subjected to a tensile test on an Instron material testing machine, and the mechanical properties obtained are shown in Table 4. Table 4 also lists the mechanical properties of the 97W-2.1Ni-0.9Fe specimen prepared by Rabin (4) using the P/S method.
2.3 Density distribution of injection molded blanks
The molded blank of the tensile specimen shown in Figure 1 was divided into three sections, and the density measurement results of each section are shown in the figure below.
2.4 Size change of injection molded blanks
Figure 2 is a schematic diagram of the half-section of the back elastic core with a more complex shape, and its size change is shown in Table 5.
3 Discussion
3.1 Rheological behavior of feedstock
Assume that the MIM feedstock belongs to a pseudoplastic. The viscosity-shear rate relationship of the pseudoplastic can be expressed by the following formula.
Find 7. Make a double logarithmic curve of viscosity and shear rate (Figure 3), and it can be seen that the three curves under different temperature conditions are smooth and show a good linear relationship. The n values obtained by fitting are all around 0.5. This shows that it is appropriate to treat the feedstock as a pseudoplastic, and also shows that the feedstock is a uniform melt.
From the experimental results, it can be seen that when the shear rate of the feedstock is 1100s' (close to the shear rate of the injection molding machine), the viscosity of the feedstock only drops from 47.9Pa·s to 39.7Pa·s when the temperature rises from 170℃ to 190℃ (injection temperature range), showing a relatively ideal stability, which is beneficial to injection molding.
3.2 Comparison of mechanical properties with materials produced by pressing-sintering process
Although Rabin and German adopted a complex sintering and heat treatment process, and the sintering atmosphere alone used dry hydrogen, argon and wet hydrogen alternately, and its theoretical density reached more than 99.5%, the mechanical properties of the alloy containing 97% W were comparable to those of MIM products in terms of ductility, but its strength was significantly lower than that of MIM products.
The microstructure of tungsten-based heavy alloys consists of granular tungsten particles and a network-distributed binder phase. The direct contact between tungsten particles is the most likely place for fracture sources to occur [8]. Therefore, it is an effective way to improve the performance of the alloy by evenly distributing the binder phase around the tungsten particles and reducing the direct contact between them, especially for heavy alloys with a high tungsten content (>93%). Compared with the traditional powder metallurgy process, the MIM process adds a mixing process. Due to the addition of organic binders and surfactants, the tungsten powder is more dispersed and the agglomeration phenomenon is eliminated. In addition, this mixing process can eliminate the powder density segregation existing in the dry mixing process, so that the distribution of the binder phase is more uniform (as shown in Figure 4). In addition, there is almost no pressure gradient in the injection molding process, and the product density distribution is uniform (Figure 1), so the strength of the MIM product is significantly improved.
3.3 Product size change and shrinkage uniformity
Due to the addition of a large amount of binder to the powder, the blank shrinks greatly during sintering. Under the isotropic condition, the shrinkage of the blank can be calculated by the following formula:
In the formula, δ is the shrinkage; Lx is the blank size; L= is the product size; V is the powder loading in the feed; p, is the relative density of the product.
If the sintered product is fully densified, that is, pr=1, then the shrinkage of the green blank in this experiment should be 21.89% according to formula (6). It is slightly larger than the test value of this experiment, which is mainly due to pr<1. From this formula, it can be inferred that the relative density of the experimental sintering test is 99.46%, which is consistent with the relative density of 99.41% in the experimental test results.
From the above comparison results and Table 5, it can be seen that the sintering shrinkage of injection molded products is basically isotropic. This is because the density gradient in the blank is small and the shrinkage is uniform during sintering.
4 Conclusion
(1) During the MIM process, the uniformity of powder distribution is improved and the density gradient of the blank is eliminated, so that the alloy exhibits better mechanical properties. The properties achieved are ob=936MPa, co.2=649MPa, δ=11.4%, HRC=31.
(2) The rheological behavior of MIM feed can be described by pseudoplastic body. The double logarithmic curve of viscosity-shear rate with good linearity is a reflection of the uniformity of feed.
(3) The sintering shrinkage of the heavy alloy products made by MIM process is basically isotropic, about 22%, the sintering relative density is 99.4%, and the dimensional deviation range of the product is ±0.02mm.
Tungsten-nickel-iron alloy (W-Ni-Fe)
Tungsten-nickel-iron alloy is a tungsten-based heavy alloy, which belongs to powder metallurgy materials and is made of three metals: tungsten (W), nickel (Ni), and iron (Fe) through a specific process. It combines the high density and high strength of tungsten with the toughness of the nickel-iron bonding phase, and is an important structural material in the industrial field.
The spherical W-Ni-Fe alloy powder produced by Stardust Technology is prepared by radio frequency plasma spheroidization process, which has the characteristics of high purity and low oxygen, high sphericity, smooth surface, no satellite, uniform particle size distribution, excellent flowability, high bulk density and high tap density.https://www.stardustpowder.com/spherical-wnife-refractory-hea-powder
For more details, please contact Vicky +86- 13318326185