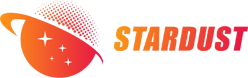
Abstract: Tantalum-based alloys have become one of the important candidate materials for high temperature structural parts in the aerospace field due to their high melting point and good high temperature strength, but poor high temperature oxidation resistance is the key problem restricting their application. This paper reviews the protection methods of tantalum-based alloys against high temperature oxidation from three aspects: alloy, grain refinement and high temperature coating, and analyzes the problems faced in current research.
With the rapid development of my country's aerospace industry, the operating temperature of the engine continues to rise, which has increasingly stringent requirements for high temperature structural materials. Finding a high temperature resistant material that can work stably in a high temperature environment of 1 800 ℃ and above has become the work direction of material researchers.
Tantalum belongs to the ⅤB group refractory metal with a melting point of up to 3 033 ℃, a density of 16.68 g/cm3, a lattice type: body-centered cubic, a thermal conductivity (25 ℃) of 54W/M·K, a linear expansion coefficient (0-100 ℃) of 6.5×10-6, good corrosion resistance, not only excellent mechanical properties, stable physical and chemical properties, but also good high temperature mechanical properties. The excellent properties of tantalum-based alloys make them an important candidate for high-temperature structures in the aerospace field. However, tantalum-based alloys have poor oxidation resistance and begin to oxidize at 600 °C. As the oxide layer continues to thicken, the internal stress generated between the oxide and the metal interface will cause the oxide layer to crack and fall off, followed by continuous re-oxidation and shedding, forming catastrophic oxidation. Therefore, it is of great significance to improve the high-temperature oxidation resistance of tantalum-based alloys [1-6].
1.Improving high-temperature oxidation resistance through alloying
From the literature, it can be seen that the elements that improve the high-temperature oxidation resistance of tantalum-based alloys mainly include Cr, Ti, Si and various rare earth elements, among which Si is the most important element for improving the high-temperature oxidation resistance of tantalum-based alloys.
When a small amount of Cr is added, the inner layer of the oxide film on the surface of the alloy can form spinel oxides, which has a certain improvement effect on improving the high-temperature oxidation resistance; when the addition amount reaches 20%, a complete Cr2O3 film will be formed with good oxidation resistance; but if the addition amount of Cr continues to increase, the effect will become worse and worse.
Ti has a strong affinity with O. In air or oxidizing atmosphere, a dense, highly adhesive, and inert TiO2 oxide film will be formed on the titanium surface to protect the substrate from oxidation. When the Ti addition reaches 25at%, the oxygen diffusion rate can be reduced to 1/10 of the original.
Si is the most commonly used element to improve the high-temperature oxidation resistance of tantalum-based alloys. The SiO2 film formed by oxidation has excellent oxidation resistance in various atmospheres and can effectively prevent the diffusion of oxygen into the interior of tantalum-based alloys. In addition, SiO2 glass has a certain fluidity at high temperatures, has self-healing ability, and can withstand certain mechanical deformation. It is the most commonly used additive element.
In addition, adding rare earth elements such as La, Ce, and Y to tantalum-based alloys can also effectively improve the high-temperature oxidation resistance. The addition amount is generally less than 1at%; when added in the form of rare earth oxides, the addition amount is generally 1% to 3%. Rare earth or rare earth oxides, as active elements, can enhance the adhesion between the oxide film and the substrate, thereby improving its high-temperature oxidation resistance [8-12].
2.Grain refinement improves high temperature oxidation resistance
The oxidation resistance of alloys is closely related to the microstructure, especially the grain size. Once the alloy composition is determined, the influence of grain size becomes particularly important. Methods for grain refinement include surface shot peening, cold rolling, laser treatment and rapid solidification, which can all improve the high temperature oxidation resistance of tantalum-based alloys. Grain refinement generally improves the oxidation resistance of alloys through two mechanisms: (1) by improving the adhesion of the oxide film so that it does not diffuse with the matrix; (2) by selective oxidation through grain boundary diffusion to form an oxide film with good protective performance. Many research results show that as the grain size of the alloy decreases, its high temperature oxidation resistance improves to varying degrees [1-6].
3. Protective coating improves high temperature oxidation resistance
The research on high temperature oxidation resistance protective coatings on tantalum-based alloy surfaces began in the 1970s, mainly drawing on the protection methods of niobium alloys and molybdenum alloys. At present, the research on high temperature oxidation resistance protective coatings is mainly focused on Ta-10W alloys.
3.1 Classification of high-temperature protective coatings for tantalum-based alloys
From the current research direction, tantalum-based alloy high-temperature oxidation-resistant protective coatings are mainly divided into silicide coatings and metal coatings. Silicide coatings use the Si element in the coating to oxidize to form a SiO2 glass film, which effectively prevents the diffusion of external oxygen into the interior of the tantalum-based alloy, thereby achieving a protective effect against high-temperature oxidation. Silicide coatings have good oxidation resistance and excellent thermal stability, and the operating temperature can reach 1 800 ℃. Some research institutions and scholars at home and abroad have used a variety of methods to prepare silicide coatings with good comprehensive performance. Dozens of research units in the United States and other countries have developed a variety of protective coatings, such as the 512A (Si-
20Cr-5Ti) coating material developed by Servania, which has been successfully used in the engine thrust chamber of the space shuttle. However, the problem with silicide coatings is that when the operating temperature exceeds 1 800 ℃, the SiO2 glass film will quickly volatilize and fail at high temperatures, resulting in catastrophic oxidation of tantalum-based alloys. Therefore, it also limits the use of silicide coatings in ultra-high temperature environments.
The research on metal coatings was first proposed by the Russians. IITRI developed Hf-Ta metal coating layer protection Ta-10W alloy. Hf was added to the tantalum-based alloy to improve its oxidation resistance. Below 1 800 ℃, a structure with HfO2 as the inner layer and Ta2O5 as the outer layer was formed by oxidation; above 1 800 ℃, a structure with HfO2 as the inner layer and Ta2Hf6O19 as the outer layer was formed, improving the high-temperature oxidation resistance of the alloy. Inspired by this, Sylvania Company of the United States developed an Hf-Ta protective layer prepared by slurry sintering method and named it R515 (Hf-20Ta-0.25Si), which can be used at 2 220 ℃ for 1 h; by adding alloying elements to the Hf-20Ta alloy to improve its performance, the study found that only molybdenum slightly improved its oxidation resistance; adding 2% Al to R515 can improve the sintering performance, and the high-temperature oxidation resistance can be used for a short time at 2 000 ℃.
Research on adding Al, Cr, Si, B, Ir, etc. to R515 found protective layer systems such as Hf-Ta Cr-B, Hf-Ta-Cr-Al, and Hf-Ta-Ir-Al. The anti-oxidation life at 1 371 ℃ is more than 450 h, which is the most promising plastic protective layer for long-term use of tantalum-based and niobium-based alloys at medium temperature.
A composite protective layer was developed based on R515. The bottom layer is 90HfB2-10MoSi2 powder, which is made by sintering at 1 820 ℃ for 15 min and is a porous compound layer; then Hf-20Ta-0.25Si slurry is applied on it and sintered to block and fill the pores, which can be used for a long time at 1 800 ℃ [11-19].
3.2 Preparation method of high-temperature anti-oxidation coating of tantalum-based alloys
At present, the more mature process methods for preparing high-temperature anti-oxidation coatings of tantalum-based alloys are: infiltration method, slurry sintering method, thermal spraying method and ion sputtering method.
(1) Infiltration method.
The infiltration method is generally carried out in a vacuum sintering furnace or in a protective atmosphere within a certain temperature range (800 ℃ ~ 1500 ℃). The preparation method is simple, and the coating and the substrate are metallurgically bonded, so the bonding strength is good and not easy to fall off. The disadvantage is that the coating is uneven and the thickness is difficult to control.
(2) Slurry sintering method.
The slurry sintering method is to apply silicide slurry to the surface of tantalum-based alloy, and perform high-temperature sintering treatment in a vacuum sintering furnace. Through the diffusion between the slurry and the substrate, a coating with good bonding strength is obtained. Its composition and thickness are very uniform and controllable. At the same time, it has the advantages of good heat transfer and fast infiltration and plating speed. Therefore, it is a preparation method that has attracted much attention in recent years.
(3) Thermal spraying method.
Thermal spraying is a process method in which the spraying material is heated and melted or semi-melted into droplets or droplets with solids, and then sprayed at high speed onto the surface of tantalum-based alloy to form a high-temperature oxidation-resistant protective coating. Since the 1950s, the self-fluxing alloy powder and exothermic composite powder developed have improved the porous structure of the coating, achieved metallurgical bonding between the coating and the substrate, and greatly expanded the application field of thermal spraying. The disadvantage is that the thickness and uniformity of the coating prepared on the surface of special-shaped parts are difficult to control.
(4) Ion sputtering method.
A process method in which atoms or molecules on the surface of the material escape with a certain energy and then deposit into a film on the surface of the substrate. The sputtering method can obtain film layers of various materials. Among various physical vapor deposition methods, it is easiest to control the components of the high-temperature oxidation protection coating. The disadvantage is that it is not easy to prepare a high-temperature protection coating with uniform thickness in the inner cavity of the part [13-19].
4. Existing problems and development trends
As a high-temperature structural material with great potential, tantalum-based alloys have a very broad application prospect in the field of aerospace. It is of great significance to study the high-temperature oxidation resistance of tantalum-based alloys. Although a lot of research work has been carried out on the high-temperature oxidation protection methods of tantalum-based alloys at home and abroad, and some progress has been made, there are still some problems that need further research.
(1) While alloying improves the high-temperature oxidation resistance of tantalum-based alloys, it also reduces the high-temperature mechanical properties of tantalum-based alloys; and the effect of improving the high-temperature oxidation resistance of tantalum-based alloys by alloying is limited. Therefore, while using the alloying method to improve the high-temperature oxidation resistance of tantalum-based alloys, its influence on the high-temperature mechanical properties must also be considered to achieve the best optimization of the performance.
(2) Grain refinement can also improve the high-temperature oxidation resistance of tantalum-based alloys and achieve self-protection. However, the current research on the influence of grain size on the high-temperature oxidation resistance of alloys is relatively scattered and lacks systematicity. Related research work needs to be continued in the future.
(3) The current problem of tantalum-based alloy high-temperature coatings is that the thermal expansion coefficients of the coatings and substrates are poorly matched, and they are easy to peel off when subjected to thermal fatigue or thermal shock. In addition, adverse chemical reactions may occur between the coating and the substrate, and between the coating and the environment, resulting in a decrease in the mechanical properties of tantalum-based alloys. In order to solve this problem, the preparation method of gradient composite coatings can be considered. Future research will also focus on: ① Optimizing the existing coating preparation process to further improve the high temperature oxidation resistance of the coating; ② Compounding multiple coating preparation methods to prepare a gradient composite coating with excellent comprehensive performance; ③ Developing new high temperature oxidation resistance coating materials.
Paper citation information
2016 NO.09
SCIENCE & TECHNOLOGY INFORMATION
DOI: 10.16661/j.cnki.1672-3791.2016.09.150
Tantalum-tungsten alloy is a high-density material with high melting point, high tensile strength, good dynamic ductility and corrosion resistance. It is used in chemical corrosion protection, machinery, aerospace and military fields. The spherical Ta-W alloy powder produced by Stardust Technology is prepared by radio frequency plasma spheroidization process, which has the characteristics of high purity and low oxygen, high sphericity, smooth surface, no satellite, uniform particle size distribution, excellent flowability, high bulk density and high tap density.
https://www.stardustpowder.com/spherical-ta-w-alloy-powder
Please contact us for more details,Vicky +86-13318326185