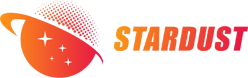
With the rapid development of China's aerospace and aviation industry, the engine's operating temperature continues to rise, which for high-temperature structural materials requirements are increasingly demanding, looking for a stable work in the high temperature environment at 1800 ℃ and above the resistance of ultra-high temperature materials has become the direction of the work of materials researchers.
Tantalum belongs to the Ⅴ B refractory metal, melting point as high as 3033 ℃, density of 16.68g/cm3, lattice type: body-centered cubic, thermal conductivity (25 ℃) 54W/M-K, coefficient of linear expansion (0 ~ 100 ℃) 6.5 × 10-6, corrosion resistance, not only has excellent mechanical properties, stable physicochemical properties, and good high temperature mechanical properties. The excellent characteristics of tantalum-based alloys have made them a candidate material for high-temperature structures in the field of aerospace and aviation and its importance.
However, tantalum-based alloys have poor oxidation resistance, and oxidation starts to occur at 600°C. With the continuous thickening of the oxide layer, the internal stress generated between the oxide and metal interfaces will cause the oxide layer to crack and lead to detachment, followed by continuous re-oxidation and detachment, resulting in catastrophic oxidation. Therefore, it is of great importance to improve the anti-temperature oxidation performance of tantalum-based alloys [1-6].
1 Improvement of anti-temperature oxidation performance through alloying
It is known from the literature that the elements to improve the anti-temperature oxidation performance of tantalum-based alloys mainly include Cr, Ti and Si and various rare earth elements, etc., of which Si is the most important element to improve the anti-temperature oxidation performance of tantalum-based alloys.
When a small amount of Cr is added, the inner layer of the oxide film on the surface of the alloy can form spinel-type oxides, which has a certain improvement effect on the improvement of anti-temperature oxidation performance; when the added amount reaches 20%, a complete Cr2O3 film will be formed, which has a good antioxidant performance; however, if the added amount of Cr continues to be increased, the effect is getting worse and worse.
Ti and O have a great affinity, in the air or oxidizing atmosphere, titanium surface will generate a layer of dense, strong adhesion, inert TiO2 oxide film, to protect the substrate from oxidation. When the addition of Ti reaches 25at%, the oxygen diffusion rate can be reduced to 1/10 of the original.
Si is the most commonly used element to improve the anti-temperature oxidation performance of tantalum-based alloys. SiO2 film formed by oxidation has excellent antioxidant performance in various atmospheres, and can effectively prevent the diffusion of oxygen into the tantalum-based alloy, and SiO2 glass has a certain mobility at high temperatures, has the ability of self-healing, and can withstand a certain degree of mechanical deformation, it is the most commonly used additive elements.
In addition, the addition of rare earth elements such as La, Ce, Y, etc. in tantalum-based alloys can also effectively improve the resistance to high-temperature oxidation performance, and the amount of addition is generally below 1at%; when added in the form of rare earth oxides, the amount of addition is generally 1% to 3%. Rare earths or rare earth oxides as active elements can enhance the bonding of the oxide film with the substrate, thus improving its resistance to high-temperature oxidation performance [8-12].
2 Grain refinement to improve the anti-temperature oxidation performance
The antioxidant performance of the alloy has a great relationship with the microstructure, especially the size of the grain. When the alloy composition is determined, the effect of grain size is particularly important. The methods of grain refinement include surface shot peening, cold rolling, laser treatment and rapid solidification, all of which can improve the high-temperature oxidation resistance of tantalum-based alloys. Grain refinement generally improves the oxidation resistance of the alloy through two mechanisms: (1) by improving the adhesion of the oxide film, so that it does not diffuse with the substrate to each other; (2) through the diffusion of grain boundaries occurs selective oxidation, the formation of good protective properties of the oxide film. The results of many studies have shown that with the reduction of the grain size of the alloy, its resistance to high-temperature oxidation performance are improved to varying degrees [1-6].
3 protective coating to improve the anti-temperature oxidation performance
Tantalum-based alloy surface anti-temperature oxidation protective coating research began in the 1970s, mainly based on niobium alloys and molybdenum alloy protection methods. The current research on anti-temperature oxidation protective coatings is mainly focused on Ta-10W alloys.
3.1 Classification of tantalum-based alloy high-temperature protective coatings
From the current research direction, tantalum-based alloy anti-temperature oxidation protective coating is mainly divided into silicide coating and metal coating.
Silicide coating is to use the Si element in the coating to generate SiO2 glass membrane after oxidation, effectively preventing the diffusion of external oxygen to the inside of tantalum-based alloy, so as to achieve anti-temperature oxidation protection effect. Silicide coating has good antioxidant performance, and has superior thermal stability, the use of temperature up to 1800 ℃. Some research institutes and scholars at home and abroad have used various methods to prepare silicide coatings with good comprehensive performance. Dozens of research units such as the United States developed a variety of protective coatings, such as the Selvania company developed R512A (Si - 20Cr - 5Ti) coating materials, successfully applied to the space shuttle engine thrust chamber and so on. However, the problem with silicide coatings is that when the use temperature exceeds 1800℃, the SiO2 glass film will rapidly volatilize and fail at high temperature, leading to catastrophic oxidation of tantalum-based alloys, thus, also limiting the use of silicide coatings in ultra-high temperature environments.
The study of metal coatings was first proposed by the Russians.IITRI developed Hf-Ta metal cladding to protect Ta-10W alloys. By adding Hf to the tantalum-based alloy to improve its oxidation resistance. 1800 ℃ below, through oxidation to form the inner layer of HfO2, the outer layer of Ta2O5 structure; and in 1800 ℃ above, the formation of the inner layer of HfO2, the outer layer of the structure of the Ta2Hf6O19, to improve the alloy's resistance to high-temperature oxidation performance. The United States Sylvania company was inspired by the development of the Hf-Ta protective layer prepared by slurry melting and burning method, and named R515 (Hf-20Ta-0.25Si), which can be used at 2220 ℃ for 1h; through the addition of alloying elements to the Hf-20Ta alloy, to improve its performance, it was found that only molybdenum on the antioxidant performance is slightly improved; in the R515 to add 2% of Al in R515 can improve the melting and burning performance, anti-temperature oxidation performance can be used in 2000 ℃ for a short time.
R515 based on the addition of Al, Cr, Si, B, Ir, etc. The study found that Hf-Ta-Cr-B, Hf-Ta-Cr-Al, Hf-Ta-Ir-Al and other protective layer system. The antioxidant life at 1371°C is above 450h, which is the most promising plastic protective layer for tantalum-based and niobium-based alloys for medium-temperature and long-cycle use.
A composite protective layer was developed on the basis of R515. The bottom layer is 90HfB2-10MoSi2 powder, made by melting and burning at 1820℃ for 15min, which is a porous compound layer; and then Hf-20Ta-0.25Si slurry coated with it and melting and burning in order to plug the filled pores, and it can be used for a long time at 1800℃ [11-19].
3.2 Preparation method of tantalum-based alloy high-temperature antioxidant coating
At present, the preparation of tantalum-based alloy high-temperature antioxidant coating more mature process methods are: package infiltration method, slurry sintering method, thermal spraying method and ion sputtering method.
(1) Overmolding method.
Package penetration method is generally in the vacuum sintering furnace or protective atmosphere, in a certain temperature range (800 ℃ ~ 1500 ℃), the preparation method is simple, the coating and the substrate for the metallurgical bond, and thus the bond is good, not easy to fall off, the disadvantage is that the coating is not uniform, the thickness of the unevenness is not easy to control.
(2) Slurry sintering method.
Slurry sintering method is a silicide slurry coated on the surface of tantalum-based alloys, high-temperature melting and burning treatment in a vacuum sintering furnace, through the diffusion between the slurry and the substrate to get a good bonding force of the coating, its composition and thickness are very uniform and controllable, and at the same time has the advantages of good heat transfer, fast penetration plating, and so on, and thus it is the preparation method of recent years is very concerned about.
(3) Thermal spraying method.
Thermal spraying is the spraying material heated melting or semi-melting into liquid droplets or entrained solid droplets, high-speed spray to the surface of the tantalum-based alloy, the formation of high-temperature oxidation-resistant protective coating process. From the 1950s developed self-melting alloy powder and exothermic composite powder, improve the porous structure of the coating, realize the metallurgical combination of the coating and the substrate, greatly expanding the application field of thermal spraying. The disadvantage is that the thickness and uniformity of the coating prepared on the surface of shaped parts are not easy to control.
(4) Ion sputtering method.
Ion sputtering method is the use of high charge energy particles under vacuum conditions to bombard the surface of the material, so that the material surface atoms or molecules to a certain energy to escape, and then deposited on the surface of the substrate into a film process method. Sputtering method can be obtained from a variety of materials of the film layer, in a variety of physical vapor deposition in the easiest to control the components of the anti-temperature oxidation protective coating, the disadvantage is that in the internal cavity of the part is not easy to prepare a uniform thickness of high temperature protective coating [13-19].
4 Problems and development trends
As a very potential high-temperature structural material, tantalum-based alloys have a very broad application prospect in the field of aerospace, and the study of tantalum-based alloys anti-temperature oxidation performance is of great significance. Although a lot of research work has been carried out at home and abroad on the anti-temperature oxidation protection methods of tantalum-based alloys, and some progress has been made, there are still some problems to be further studied.
(1) Alloying will reduce the high-temperature mechanical properties of tantalum-based alloys while improving the anti-temperature oxidation properties of tantalum-based alloys; and the effect of improving the anti-temperature oxidation properties of tantalum-based alloys through alloying is limited. Therefore, while improving the anti-temperature oxidation performance of tantalum-based alloys by alloying, it is also necessary to consider its effect on the high-temperature mechanical properties, so as to achieve the best optimization of the performance.
(2) The anti-temperature oxidation performance of tantalum-based alloys can also be improved by grain refinement to realize self-protection. However, the current domestic and foreign research on the effect of grain size on the anti-temperature oxidation performance of the alloy is still relatively fragmented and lacks systematic, and it is necessary to continue to carry out relevant research work in the future.
(3) The current problem of tantalum-based alloy high-temperature coatings is that the thermal expansion coefficient of the coating and the substrate is poorly matched, and it is easy to peel off when subjected to thermal fatigue or thermal shock. In addition, adverse chemical reactions between the coating and the substrate, and between the coating and the environment may also occur, leading to a decline in the mechanical properties of tantalum-based alloys. In order to solve this problem, the preparation method of gradient composite coating can be considered. Future research will also focus on: ① optimization of the existing coating preparation process, to further improve the anti-temperature oxidation performance of the coating; ② composite of a variety of coating preparation methods, the preparation of gradient composite coatings with excellent overall performance; ③ development of new anti-temperature oxidation coating materials.
Reference: (c)1994-2023 china Academic Journal Electronic publishing House. All rights reserved. http://www.cnki.net
Advantages of RF Plasma Spheronization Technology for TaW Alloys
High purity: High-energy RF plasma is used to remove impurities and ensure that the purity of the alloy powder meets the needs of high-end applications.
Excellent flowability: high sphericity and uniform particle distribution, suitable for additive manufacturing and precision molding processes.
Customized production: support a variety of W-Ta ratio alloys and particle size range customization to meet the needs of different fields.
Process stability: the core process has been strictly optimized, with good product consistency and minimal batch-to-batch variation.
We are committed to providing reliable guarantee for high-performance materials with our technical strength.
If you need more rare refractory metal spherical powder, please feel free to contact our professional manager: Cathie Zheng 13318326187.