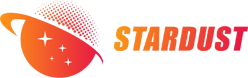
1 Preface
Selected zone laser melting (SLM) is a new rapid prototyping (RP) technology that has emerged in recent years. This technology is an additive manufacturing process that produces parts by melting a powder bed layer by layer using a laser beam as the energy source and pre-established CAD data [1].
SLM is a solid free-form manufacturing process in which 3D parts are constructed by laser scanning the powder bed in layers. Solidification is obtained by treating selected areas with thermal energy provided by a focused laser beam. A beam deflection system (galvanometer) is used and each layer is scanned with the corresponding cross-section calculated from a CAD model. Currently, SLM technology is widely used in aerospace and automotive industries. It offers a number of advantages over conventional manufacturing techniques: shorter time-to-market, use of inexpensive materials, higher product yields, versatility, high precision, and the ability to produce more functionality in parts with unique designs and inherent engineering features.SLM is an unconventional production process that uses a laser heat source to melt layers of metal powder. With a “layered manufacturing” approach, more complex parts can be formed.The principle of SLM technology is shown in Figure 1. Commercially available machines differ in the method of powder deposition (roller or scraper), the atmosphere (Ar or N2) and the type of laser used (CO2 laser, lamp or diode pumped Nd:YAG laser, disk or fiber laser) [2-4].Typical equipment for SLM is shown in Figure 2.
SLM triggers an extraordinary versatility in geometric and material design and is considered a near-net-shape technology and an exceptional technology for creating functionally gradient materials and complex components with individualized local functional requirements. In addition, SLM technology allows the production of metal parts that are almost completely dense. During the SLM process, phenomena such as residual stresses and deformation defects may occur, and in particular, the severity of warpage deformation constrains the melt quality and final application of SLM [5, 6].
This paper describes in detail the basic principle and processing of SLM technology, introduces in detail the key technology of SLM at home and abroad, the application of research results, and further discusses the application of SLM technology and its development.
2 SLM key technology research
2.1 Material optimization
Equipment, material and process are the three core elements that constitute SLM. According to the different shapes, the materials used in SLM can be categorized into metal powder, metal wire material and metal block material. The main evaluation indexes of metal powder include sphericity, average particle size, fluidity and impurity content, etc., which have different requirements for equipment and performance. However, there are no excessive requirements for the shape of wire and lump materials [7].
The main metal powder materials used in the selective laser melting process are iron-based alloys, nickel-based alloys, aluminum alloys, titanium alloys, copper alloys and cobalt-chromium alloys [8].
2.2 Equipment optimization
Compared with the traditional equipment, the newer multi-laser selective melting equipment has more than one set of lasers and scanning mirrors, which solves the problems of low forming efficiency and limited forming size [9].
Multi-laser selective melting equipment forming, each laser is responsible for processing a different area, and printing work at the same time. For the application of multi-laser selective melting technology, related scholars have conducted research. Zemin Wang et al [10] from the National Laboratory of Optoelectronics, Huazhong University of Science and Technology (HUST), used the four-laser beam selective zone laser melting equipment developed by them to study the tissue properties of Ti6Al4V lap and isolated zones formed by four lasers simultaneously. The results showed that the organizational properties of the lap zone did not change significantly (see Fig. 3).
2.3 Support processing
The support structure plays a very critical role in metal additive manufacturing technology, on the one hand, it needs to support the overhanging area of the part model, and anchor the formed metal parts to the substrate, avoiding the processing failure of the metal parts caused by gravity and external forces (such as the movement of the powder spreading roller in the SLM, etc.) during the molding process; on the other hand, it plays the role of heat conduction, and conducts out the heat accumulated during the molding process of the metal parts, avoiding the heat loss caused by the metal parts. On the other hand, it plays the role of heat conduction to transfer the heat accumulated in the metal parts during the forming process, avoiding warping and deformation, cracks, etc. caused by thermal stress and residual stress [11].
At present, a variety of styles of structures such as column support, point support, block support, ring support, mesh support and wire support can be applied to the manufacturing of parts in SLM technology. The molding effect of different types of support structures applied to the metal additive manufacturing process is shown in Figure 4. Since the generation method of this kind of support structure is not complicated, it can be supported in the current additive manufacturing CAD software (e.g., Magics, 3DXpert, etc.), additive manufacturing CAM software (e.g., Cura, Kisslicer, Slic3r, IceSL, etc.), and special software for support design (e.g., E-Stage, etc.). In recent years, some related researchers have also explored the use of infill types such as dot matrix structures and cellular units as support structures for printed models.
2.4 Process Control
SLM technology is a multidisciplinary fusion process technology, including complex thermodynamic, chemical, physical and metallurgical issues, and the process is prone to cause internal defects such as porosity, cracks and inclusions [12, 13]. Parts with excellent performance and high densities can be obtained by optimizing the process parameters in the SLM process, such as laser power, scanning path, scanning rate, lap rate and lift-off. The average applied energy per unit volume, i.e., volumetric energy density E, is usually used, and the specific expression [14] is
E = P / (vht)
Where E - volumetric energy density (J/mm3);
P - laser power (W);
v - laser scanning speed (mm/s);
h - laser scanning pitch (mm);
t - layer thickness (mm).
2.5 Composite Additive Manufacturing Technology
Composite additive manufacturing is mainly based on additive manufacturing technology, in the parts manufacturing process using one or more auxiliary processes and additive manufacturing process coupling and synergistic work, so that the process, part performance can be improved [15]. Composite additive manufacturing technology includes 3D printing technology composite new technology, 3D printing technology and traditional technology composite manufacturing technology, the use of additive manufacturing technology is not to abandon traditional manufacturing technology. Composite additive manufacturing technology includes laser-assisted composite additive manufacturing technology based on (see Figure 5), rolling-based composite additive manufacturing technology, machining-based composite additive manufacturing technology (see Figure 6), laser forging-based composite additive manufacturing technology, and shot peening-based composite additive manufacturing technology.
2.6 Multi-material additive manufacturing technology
Multi-material additive manufacturing (Multi-materialAdditiveManufacturing) technology is based on additive manufacturing technology, the parts of the material design, the use of a variety of materials with excellent properties of the overall forming, can optimize the performance of parts or achieve a variety of special features, so as to achieve the design purpose of the parts processing method. Multi-material additive manufacturing technology is rich in variety, including self-combination or cross-material combination between metallic and non-metallic materials, multiple combinations of materials, combinations of materials and stomatal dot matrix, and multi-material topology design and other forms [16].
3 Technological Applications
3.1 Applications in aerospace
SLM technology direction of development characteristics: adapted to small-size parts processing, its processing precision is higher, but the processing efficiency is low [17].SLM applications in aerospace are mainly embodied in the integration of complex internal runner structure (such as engine fuel nozzles, rocket motors, etc.), small gas turbine engines (GTE), lightweight structures (such as brackets, etc.) and bionic structures (such as cabin partition, bionic partition, etc.) and so on (see Figure 7). ), etc. (see Figure 7).
3.2 Application in rail transportation equipment manufacturing
At present, the application of laser additive manufacturing technology in rail transportation equipment manufacturing is in the frontier exploratory stage. In terms of rail transportation operation and maintenance, the German Federal Railway Company has successively carried out parts optimization design with Materialize, Concept Laser, EOS and other enterprises, and obtained bearing caps with hollow structure in order to improve the vibration-resistant performance and abrasion-resistant of the bearing caps. Alstom used SLM technology to print the topology and optimize the design of the anti-roll torsion bar mounts for the bogies of the train in order to achieve the target of 70% weight reduction. China CNR has also used SLM technology to mold a locomotive high-voltage grounding switch drive part (see Figure 8). The parts formed by SLM technology are superior to those manufactured by riveting or welding in terms of performance, with compressive performance improved by 25% to 75%, and mechanical properties even better than those of forgings, while the dimensional error of the parts is <0.1 mm [18].
3.3 Application of implants in laser additive manufacturing
In the application of SLM technology for implants, the key elements are the design of bioactive materials, pore size microstructure control, osteogenic activity of implanted materials, biomechanical properties of materials, as well as degradation of implanted materials. In addition, there are bioactive ceramics, magnesium alloy bone repair materials, surface modification of metal-based materials or polymer materials and material composite active factor addition and other active biomaterials [19].
Examples of SLM technology in terms of industrial applications abroad are as follows: the U.S. OSSEUS company formed a titanium alloy implant Aries (see Figure 9a), with a porosity of 80%, the implant can be grown in spinal tissues; the U.S. Zimmer company formed a titanium spinal implant (see Figure 9b); Germany's EIT formed a titanium intervertebral fusion with a porosity of up to 80% ( see Figure 9c), optimizing the size and shape of the foramina. Among China's companies, Akcome Medical launched titanium orthopedic implant products for the nation's first 19-cm multi-segment artificial vertebrae customized surgery (see Figure 9d).
4 Outlook
4.1 Accelerating the construction of a new type of technical safety risk regulation system
The development of science and technology sometimes brings some safety risks, and may even cause drastic changes in society. Additive manufacturing, as a manufacturing technology, is also a “double-edged sword”, on the one hand, it promotes the profound change of human production mode, on the other hand, it has also become a new source of risk in the fields of national security, social security and citizens' personal property safety [20].
The risks of additive manufacturing include the following: ① Defense security risk. ② Aerospace risk. ③Nuclear security risk. ④ Social security risk. ⑤ Food safety risk. ⑥ Medical security risk. ⑦ Economic security risk. ⑧ Ecological security risk.
4.2 Promote multi-material, multi-process synergistic metal additive manufacturing
Metal additive manufacturing technology contains a variety of different processes, such as powder bed fusion, directed energy deposition, cold spraying, etc., a variety of processes have proved to be suitable for different manufacturing areas. From personalization to small batches to high volume manufacturing of more than 100,000 pieces, additive manufacturing is working wonders. However, each process has its own technical limitations, whether due to material, size or cost, and processes cannot be generalized. In order to promote the development of multi-material and multi-process integration of metal additive manufacturing, 21 industrial and research partners from 8 European countries are jointly promoting a project called MULTI-FUN. The three-year project, funded by the European Union's Horizon 2020 Innovation Program, sets two important strategic goals: the first is to improve the performance of metal additively manufactured parts through the use of new active materials; the second is to realize the synergistic manufacturing of large-size, multi-material, complex structures through innovative and cost-effective new additive manufacturing technologies. structure collaborative manufacturing.
5 Conclusion
Additive manufacturing has been called the third industrial revolution and “savage magic weapon”, the wide range of applications in all walks of life has proved that additive manufacturing is the production of complex structural products, replacement parts, on-demand manufacturing, as well as mass customization of products ideal choice. As a metal additive manufacturing in the study of more mature SLM technology, in aerospace, rail transportation equipment manufacturing, implants, high value-added products repair and remanufacturing and other fields have a wide range of applications. Equipment, material and process are the 3 core elements of SLM. Printing strategy, material optimization, equipment optimization, model processing, support processing, simulation analysis, process control, quality control, occupational and occupational health control are the key technologies of SLM. Composite additive manufacturing, multi-material additive manufacturing, and metamaterial additive manufacturing are the cutting-edge technologies of SLM research.SLM faces many opportunities and challenges.In the future, the field of SLM should accelerate the construction of a new technology safety risk regulation system, improve the standard system, promote multi-material and multi-process synergistic metal additive manufacturing, accelerate the research and development of intelligent, high-precision and high-efficiency equipment, high-end special materials research and development, and strengthen the patent Layout and basic talent team construction, focusing on the whole process of autonomy and control.
reference:1994-2023 china Academic Journal Electronic pubolishing House. A1l rights reserved.
Stardust Technology Stardust Technology is committed to providing customers with comprehensive additive manufacturing solutions, not only focusing on the development and production of high sphericity metal powders, but also providing customers with a full range of technical support, including 3D printing services. Our products cover a variety of spherical monomaterial powders such as tungsten, molybdenum, tantalum, niobium, titanium, zirconium, vanadium, hafnium, rhenium and other high-performance materials such as tantalum alloys, niobium alloys, tungsten alloys and so on, which are widely used in the fields of aviation and aerospace, biomedicine, and industrial manufacturing. Meanwhile, we are equipped with advanced 3D printing equipments and professional technical team, which can provide one-stop service from material selection, process development to product molding, and help our customers realize efficient and innovative manufacturing needs.
If you need, please feel free to contact our professional Manager: Cathie Zheng 13318326187.