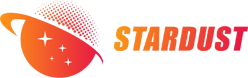
Introduction
As a new product manufacturing technology, additive manufacturing has received widespread attention in recent years. Since its emergence in the late 1980s, after more than 20 years of development, the potential of additive manufacturing technology has been continuously explored, and its combination with digital production models is driving the world to experience another "industrial revolution". 3D printing technology is a technology that uses powdered metal or plastic and other bondable materials to construct objects by printing layer by layer based on digital model files. Its basic principle is the discrete-stacking principle [2]. Compared with traditional manufacturing methods, 3D printing can reduce the use and loss of raw materials without reducing product performance, and greatly improve production speed [3]. At present, there are mainly several types of metal parts 3D printing technologies [4-]: (1) Selective laser melting (SLM), which is mainly used for complex metal precision parts, such as metal crowns, medical implants, etc.; (2) Laser near-net shaping (LENS), which is mainly used for large metal components of aircraft; (3) Electron beam selective melting (EBSM), which is mainly used for large metal components of aerospace. Selective laser melting (SLM) is one of the most important and widely used additive manufacturing technologies in metal material 3D printing. SLM can be traced back to 1989, when it was successfully developed by C. R. Dechard of the University of Texas at Austin. Initially, it could only sinter some non-metallic materials with low melting points, which was called selective laser sintering (SLS) technology [2]. Later, high-power lasers were developed and gradually applied to additive manufacturing rapid prototyping technology. SLS gradually developed into selective laser melting (SLM) technology [7].
1 Basic principle of selective laser melting
SLM is a technology that rapidly melts metal powder under the action of a high-energy laser beam and rapidly cools and solidifies. The high-energy laser inputs heat into the metal powder in a short period of time, and the metal powder quickly heats up to the melting point and melts quickly. After the laser beam leaves this point, the molten metal powder is cooled and solidified by heat dissipation, and achieves metallurgical bonding with the solid metal [8]. The first step of processing is to draw the CAD three-dimensional graphics of the workpiece in the computer, and then use the "slicing" software to discretize the three-dimensional entity into a two-dimensional plane figure to obtain the contour data of the cross section. The computer control system controls the laser scanning path according to the two-dimensional slicing information, and the laser beam acts on the powder that has been laid in the molding cavity. After one layer of scanning is completed, the substrate in the molding cavity drops a layer thickness, the powder feeding cavity rises a certain thickness, and the powder spreading roller spreads the powder evenly in the molding cavity, and then the laser scans the second layer. Then the cycle is repeated, and the melted and solidified metal powder accumulates layer by layer to form a three-dimensional entity. After the scanning is completed, the workpiece is taken out of the molding cavity and separated from the substrate, and the whole SLM process is completed. The principle is shown in Figure 1. Metal powder is easy to oxidize in a high temperature environment, and the finished workpiece may have serious defects. Therefore, during the scanning process, the cavity must be kept vacuum or a protective gas must be introduced into it to prevent metal oxidation.
2 Research Status of Metal Selective Laser Melting
2.1 Development of Selective Laser Melting Equipment
Germany is one of the earliest countries to conduct research on selective laser melting. As early as the 1990s, the Fraunhofer Laser Institute in Germany proposed this technology and successfully developed related equipment in 2002. In addition to Germany, the United Kingdom, Japan, Belgium, the United States, France and other countries have also made certain progress in this field. At present, there are many mature SLM equipment suppliers in the world, including Germany's EOS, ConnectLaser (recently acquired by General Motors) and MCP, the United Kingdom's Renishaw, the United States' 3D Company, Sweden's Arcam and France's PhenixSystem, etc. [3]. The research and development of SLM equipment is mainly concentrated in a few countries in Europe and the United States. Among them, Germany and the United States have the most mature technology and the earliest commercialization of SLM products. The above companies have developed a variety of equipment models based on the personalized product needs of users and for different application scopes and fields. The M400 of EOS in Germany is the company's latest selective laser melting equipment. The molding cavity volume is 400mm×400mm×400mm, which can manufacture large parts. The equipment uses Yb fiber laser, the maximum laser power is 1kW, and the laser spot diameter is 90μm [9]. EOSING M250 and M270 equipment can produce molded parts with a density close to 100%, a dimensional accuracy of 20-80 μm, and a minimum wall thickness of 0.3-0.4 mm; MCP's Realizer series uses a 100W solid-state laser, which can control the minimum scanning thickness to 30 μm when equipped with a galvanometer scanner, which can significantly improve the precision and surface quality of molded parts [10-11]. Additive manufacturing has developed rapidly around the world, and some universities, research institutes and companies in China have gradually begun to develop and produce SLM equipment. Huazhong University of Science and Technology, South China University of Technology, Beijing University of Aeronautics and Astronautics, Northwestern Polytechnical University and Nanjing University of Aeronautics and Astronautics started early and are in a leading position in China. At present, Huazhong University of Science and Technology has launched two sets of SLM equipment, namely HRPM-I and HRPM-II. South China University of Technology has independently developed three models, Dimetal-240, Dimetal-280 and Dimetal-100. In addition, Xi'an Polylite, Hunan Huashu High-Tech, Guangdong Hanbang Laser and other companies have gradually developed mature SLM equipment and completed commercialization. The main domestic and foreign SLM equipment manufacturers and equipment parameters are listed in Table 1.
2.2 Selective laser melting materials
SLM technology uses a high-energy-density laser beam to act on metal powder, and the temperature rises to the melting point of the metal in a short time to melt it. In theory, under the conditions allowed by the process and equipment, any metal powder can be used as the raw material of SLM. SLM powder can be divided into three types according to the composition type: pre-alloyed powder, mixed powder and single powder. The types of metal powder are shown in Figure 2. Among them, mixed powder is a mixture of multiple metal particles mixed together by mechanical mixing. The powder obtained by this method has a high bulk density, but the composition is uneven [8]. In practical applications, SLM technology has high requirements for the particle size, shape, and composition distribution of the powder. The main methods for preparing powders include water atomization, gas atomization, laminar flow atomization technology, ultrasonic coupling atomization technology, and hot gas atomization [16]. Among them, pre-alloyed powder and single-element powder are powders prepared by liquid alloy through gas atomization. The powder particles are uniform and have excellent performance, and are widely used. From the perspective of powder types, the commercial application of pre-alloyed powder is the most successful, and it is also the main research object of selective laser melting at home and abroad. Among them, titanium alloy, nickel alloy and iron alloy are the three main research directions.
2.2.1 Titanium alloy powder
Titanium alloy can be divided into three categories according to annealing structure: α, β, and (α+β). It is a structural material with excellent performance, with low density, high specific strength, good heat and corrosion resistance, good low temperature performance, low elastic modulus and thermal conductivity, etc. It is widely used in aerospace, military, medical, chemical and other fields [17]. In the direction of selective laser melting of titanium alloys, domestic and foreign research mainly focuses on pure titanium and (α+β) titanium. Among them, Ti6Al4V has good mechanical properties and excellent biocompatibility, so it has been widely studied and applied [18-21]. However, there are very few related research reports on α titanium and β titanium. Compared with (α+β) titanium, β titanium contains almost no Al and V elements that are harmful to the body, and has a higher strength level and better incision performance and toughness, which is suitable for human implants [22]. Abe et al. from Osaka University in Japan used titanium powder to form titanium bones, with a relative density of 95% and a tensile strength of 300 MPa. Pattanayak et al. from Chubu University in Japan used the SLM method to produce porous titanium with a porosity of 55% to 75% and a strength of 35 to 120 MPa [23]. Yan et al. from Huazhong University of Science and Technology used the SLM method to prepare Ti6Al4V artificial implant bones with a porosity of 5% to 10% and a microhardness of (4.0±0.34) GPa [24]. The Kruth team of the University of Leuven in Belgium used a self-developed laser to study the SLM process of atomized Ti6Al4V powder (particle size range of 5-50μm) and successfully prepared titanium alloy artificial teeth with a density of 97%. It was found that due to rapid cooling, the product is prone to form a brittle martensitic structure, and subsequent heat treatment is required to obtain a product with suitable mechanical properties [25].
2.2.2 Nickel alloy powder
Nickel alloys have good corrosion resistance, oxidation resistance and comprehensive mechanical properties, and are widely used in aerospace, petrochemical, marine ships and other fields. In aircraft engines, nickel-based high-temperature alloys are used to manufacture turbine blades to resist high temperature and high stress loads of gas to meet stringent working requirements. In SLM, the most widely used are Inconel625, Inconel718 and Waspaloy alloys. The Murr team at the University of Texas studied the SLM performance of two alloys, Inconel625 and Inconel718, with microhardness up to 4.0 GPa and 5.5 GPa, respectively, and analyzed the microstructure, surface composition and phase structure changes of the molded parts [26]. Mumtaz et al. from the Rapid Manufacturing Center of Loughborough University in the UK used a 550W Nd-YAG laser to prepare Waspaloy age-hardening high-temperature alloy, and the relative density of the finished product reached 99.7% [27]. There are also studies on SLM forming of nickel alloy powder in China. For example, Liu Bin's team at North University of China systematically and comprehensively studied the key process elements of SLM forming of GH4169 (similar to Inconel718) [10].
2.2.3 Ferroalloy powder Ferroalloy is the most widely used and largest metal material in the world. According to domestic and foreign literature, the SLM research of iron-based alloy powder is also the most comprehensive and in-depth. Iron-based alloy powder mainly includes pure iron powder, M2 high-speed steel, 316L stainless steel, H13 tool steel, maraging steel, etc. Casati of the Polytechnic University of Milan, Italy, studied the influence of scanning parameters and scanning methods on the mechanical properties and microstructure of SLM parts of 316L stainless steel. The powder size range is 5-50μm [13]. Shishkovsky of the Lebedev Physical Institute in Russia studied the SLM process of Permalloy and manufactured small complex structure electronic components. It was found that the hardness of the parts fluctuated greatly. The Fe3O4 was increased by applying an external magnetic field, which changed the distribution of the new phase [28]. Chen Hongyu from Nanjing University of Aeronautics and Astronautics successfully prepared 5CrNi4Mo die steel specimens using SLM, studied the phase transformation process and mechanism of laser forming, and analyzed the influence of linear energy density on the mechanical properties of SLM [29]. Mai Shuzhen et al. from South China University of Technology used the SLM equipment independently developed by them and adopted the orthogonal experimental method to study and analyze the cause of the step effect on the surface of NiCr alloy parts [30]. In addition to the above three main pre-alloyed powders, copper-based alloys and aluminum-based alloys are also the main research objects of SLM process, and their forming process research is also relatively complete.
2.3 Selective Laser Melting Process
Selective Laser Melting (SLM) is a complex processing and manufacturing technology involving many parameters (see Figure 3). These parameters have different degrees of influence on the SLM processing process, product morphology and performance, and the parameters also affect each other. However, a large number of research results show that as long as some of the important influencing factors (such as powder particle size, scanning speed, laser power, scanning strategy, etc.) are controlled, well-formed and excellent-performance molded parts can be obtained. If these parameters are not reasonably selected, some typical problems will occur in the SLM process, such as spheroidization, porosity, residual stress and strain, and affect the microstructure of the molded parts. These problems are briefly introduced below.
2.3.1 Spheroidization
In the SLM process, metal powder is melted into liquid metal under the irradiation of the laser beam. If it is not well spread on the substrate or the front layer substrate, but forms a large number of independent metal balls of different sizes, this phenomenon is called the spheroidization phenomenon in the SLM process [31]. Spheroidization is a common phenomenon in SLM. On the one hand, spheroidization will greatly affect the surface quality of the molded parts. Since the solidified metal balls are independent of each other, there are a large number of pores between the metal balls during the layer-by-layer scanning process, resulting in excessive porosity and decreased mechanical properties. On the other hand, the surface spheroidization will hinder the normal operation of the powder roller and increase the friction between the powder scraper and the surface. This will not only affect the surface quality of the metal, but also hinder the forming process in severe cases. The spheroidization process is shown in Figure 4.
The reason for the formation of the spheroidization phenomenon is the wettability problem between the liquid metal and the solid matrix. In the SLM process, the molten metal liquid has a tendency to automatically reduce the surface energy at the junction with the solid matrix, that is, condense into a sphere. Studies have shown that the wettability of the solution and the matrix is related to the particles, oxygen content, melting temperature, etc. of the powder [29, 32]. The increase in oxygen content is not conducive to the wetting and spreading of the molten pool. If the powder is made by the water mist method, the surface forming quality will be poor. In addition, the higher sphericity and smaller size of the powder can also increase the fluidity of the powder, thereby reducing the occurrence of spheroidization. High molten pool temperature can also improve the fluidity of the melt to reduce the spheroidization rate. Studies have found that when considering the effect of powder thickness on spheroidization, high powder layer thickness is very likely to cause spheroidization, while low layer thickness is conducive to the wetting and spreading of the melt [28-29]. The reasons are as follows: (1) High powder layer thickness reduces the laser energy per unit volume, and the temperature field decreases, resulting in poor flow-wettability; (2) It is difficult for the laser to penetrate the powder layer and contact the substrate, so a good welding effect cannot be obtained. In addition to the above spheroidization caused by wettability, there are some small spheroidizations that cannot be avoided in the SLM process. They are caused by the laser beam impacting the molten pool and the evaporation of the melt, which produces splashes [32]. TheseThe "small spheres" are very small and will remelt when scanning adjacent tracks, which has no adverse effect on the performance of the workpiece.
2.3.2 Porosity
Porosity is another important feature of the selective laser melting process. It will directly affect the density, microstructure and mechanical properties of the molded parts, and seriously affect the practical performance of SLM parts. The important purpose of optimizing SLM process parameters is to obtain high-density metal parts. Therefore, a large number of studies at home and abroad have focused on reducing porosity. Qiu et al. from the University of Birmingham in the UK studied the SLM forming process of Ti6Al4V and analyzed the influence of liquid flow on pore formation during the process. They found that with the increase of scanning speed and powder thickness, the porosity of the molded parts increased and the surface roughness also deteriorated. It is also speculated that the process parameters affect the flow properties of the liquid in the molten pool, which cannot be filled in time and produces pores [32]. Gu Dongdong et al. from Nanjing University of Aeronautics and Astronautics conducted SLM research on TiC/Inconel718 composites and found that with the increase of laser power, the number of large-sized irregular holes between layers decreased. This is because at lower laser power, the fluidity of the liquid phase deteriorates, making it difficult to penetrate and form holes. Only by controlling the energy density of the body within a reasonable range can it be beneficial to the densification of the workpiece and avoid the generation of defects such as pores [33].
The main reasons for the formation of pores in SLM are as follows:
(1) Spheroidization If a more serious spheroidization phenomenon occurs during the SLM process, gaps will be generated where the metal balls are in contact, and the metal powder cannot penetrate. After multiple layers are accumulated, larger holes will be formed; even if the powder can enter the gap between the metal balls, the laser's penetration ability is limited, and it is difficult to transmit energy to the deep melting powder, thus affecting the densification of the workpiece [34]. Spheroidization is the main reason for the appearance of pores.
(2) Porosity
Since the SLM powder layer is porous and the molding cavity is generally filled with inert gas to protect it from metal oxidation, gas is easily mixed into the molten metal liquid during the scanning process. If the cooling speed is too fast, the gas will not have time to escape from the molten pool, and holes may be formed. The volume of this type of hole is generally small and regular spherical, and the inner wall of the hole is relatively smooth. To avoid the generation of gas-induced pores, it is necessary to start from the process parameters and appropriately increase the retention time of the molten pool so that the gas in the molten pool has enough time to escape.
(3) Scanning spacing is too large (no overlap)
In the SLM process, the scanning spacing is an important process parameter. In order to obtain a molded part with higher density, it is necessary to reasonably design the scanning spacing so that the welds are partially overlapped to reduce the generation of pores. Even if the occurrence of spheroidization can be controlled during the scanning process, if the scanning spacing is too large, a large number of very large pores will still be formed.
(4) Cracks and thermal stress
Cracks and thermal stress are another important cause of pores. The selective laser melting process has a very fast cooling rate and a very large temperature gradient, and there are high thermal stress and phase change stress in the workpiece. Among them, thermal stress is the main reason for the cracking of SLM molded parts. During the laser heating and cooling process, the expansion and contraction trends inside and around the solidified metal are inconsistent, so thermal stress is generated. Phase change stress is generated because the specific volumes of two or more phases are different when some metal materials undergo solid phase transformation, and they restrain each other during expansion or contraction, generating internal stress. When stress is generated inside the molded part, warping, deformation or cracking will occur to release the stress, so pores are generated. This kind of pore can be reduced or eliminated by pre- and post-heat treatment. For example, the substrate and powder can be preheated before the part is made to reduce the temperature gradient, optimize the scanning method or strategy [35], and post-heat treatment such as hot isostatic pressing can eliminate pores [36].
2.3.3 Microstructure
Selective laser melting has the characteristics of short reaction time, high heating temperature, and fast cooling rate, which will significantly affect the microstructural characteristics. The main influencing factors include laser parameters, scanning parameters, material physical properties and scanning strategies. SLM microstructures generally have non-equilibrium solidification characteristics, and the structure is very fine and uniform. Thijs of the University of Leuven in Belgium used the SLM method to prepare Ti6Al4V and found that with the increase of volume energy density (i.e., increasing laser power, reducing scanning rate, etc.), the grains became coarser and intermetallic compounds Ti3Al precipitated during the scanning process [35]. The direction of grain growth is mainly related to the heat transfer direction. The microstructure morphology of SLM-prepared parts is diverse, including columnar crystals with obvious directionality, cellular crystals and equiaxed crystals growing in all directions. This is because the heat dissipation method and speed of different parts in the SLM process are inconsistent [34]. After the laser energy is absorbed by the metal powder, the excess heat is dissipated in the following three ways: (1) dissipated into the surrounding protective gas by convection; (2) diffused into the surrounding unmelted metal powder by heat conduction; (3) transferred to the substrate through the melted and solidified metal (see Figure 5).
Studies have shown that in addition to being affected by scanning parameters and heat conduction, scanning strategies also have an impact on microstructures [12, 35]. The Thijs team of the University of Leuven in Belgium found that in unidirectional and reciprocating scanning, the heat transfer along the substrate direction is the fastest, and the grains extend upward in a columnar shape from the bottom, tilted at a certain angle to the substrate. Under the orthogonal scanning strategy, the grain size in the sample tends to be consistent in all directions.
2.3.4 Post-heat treatment
SLM is a process of rapid heating and rapid cooling. The finished workpiece often has large residual stress, pores and uneven distribution of components. These problems will reduce or even deteriorate the mechanical properties of the workpiece. Therefore, in order to improve the performance and availability of SLM molded parts, subsequent heat treatment is particularly important. The main subsequent heat treatments include annealing, solution aging and hot isostatic pressing (HIP). For some aged steels, such as maraging steel, they need to precipitate second phase alloy compounds to improve strength and toughness, which requires solution and aging at a certain temperature and time. Therefore, for this type of material, the workpiece needs to be subjected to solution aging treatment after processing to improve performance [37]. Hot isostatic pressing is a process used in the field of powder metallurgy to eliminate pores and close microcracks. The HIP process first places the workpiece in a hot isostatic pressing furnace, raises it to a certain temperature (generally 2/3 of the melting point), and then pressurizes the workpiece through gas or liquid, and the pressure is evenly distributed on the surface of the workpiece. The workpiece treated with HIP can basically eliminate the holes and reach a dense state. Combined with the characteristics of SLM prepared parts, the HIP technology is applied to selective laser melting, which can effectively improve the density of the product and improve its mechanical properties. Leuders et al. of Paderborn University in Germany performed hot isostatic pressing on Ti6Al4V samples prepared by SLM and found that the fatigue strength and crack growth resistance of the samples were significantly improved [36]. Qiu et al. of the University of Birmingham in the UK found that HIP can effectively reduce the porosity of Ti6Al4V prepared parts and decompose the martensite part. The strength of the sample is slightly reduced, but the plastic toughness is significantly improved [12].
3 Conclusion
With the development and maturity of metal 3D printing technology, metal parts with perfect forming and reliable performance will gradually be applied to industrial production, aerospace, medical implants, education and teaching and other fields. The performance of metal parts prepared by selective laser melting technology is improved compared with traditional manufacturing methods. The main problems that need to be solved at present are: (1) The manufacturing cost is high. Its high equipment and material costs limit its promotion; (2) The manufacturing size is limited. The size of SLM molded parts is limited by the molding cavity of the equipment. The current maximum molding cavity volume is about 350mm×350mm×350mm; (3) The material processing parameters are different. In order to obtain the optimal processing and manufacturing parameters of different metal materials, a large number of pre-printing experiments are required in the early stage to obtain the optimal process window.
Paper citation information:
Material Guide, May 2017, Vol. 31, Album 29
Chinese Library Classification Number: V261.8; TP273; TB31
Document Identification Code: A
Stardust manufacturing various rare and refractory metal spherical powders
-Using radio frequency plasma spheroidization Technology, high purity, low oxygen content, high sphericity, smooth surface, no satellite balls, uniform particle size distribution, and excellent flow properties;
-Suitable for laser/electron beam additive manufacturing, laser direct deposition, hot isostatic pressing, injection molding, laser cladding and other processes;
-Acceptable particle size customization to meet the needs of customers in different fields.
For more details, please contact Vicky Zhang at +86-13318326185