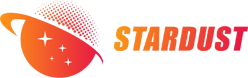
0 Preface
SiC ceramics are widely used in aerospace, military equipment, and nuclear reactors due to their high hardness, high strength, low coefficient of thermal expansion, and excellent resistance to irradiation and corrosion [1-2]. Despite the excellent comprehensive performance of SiC ceramics, its higher hardness, lower fracture toughness, and more difficult machining, to a certain extent, limits its application in the engineering field. Therefore, in practical engineering applications, the connection problems of SiC and its composites need to be solved urgently. At present, the connection technology of silicon carbide and its composites can be divided into brazing connection [3], diffusion connection [4], instantaneous liquid-phase connection [5], reaction connection [6] and so on. Among all the joining technologies, brazing joining is the most economical, convenient and effective joining technology, and its process is simple, which can realize the one-time joining of large-size complex structural parts, as well as the simultaneous joining of multiple batches of small-size samples. At present, the brazing materials used for brazing connection of SiC are mostly Ag-Cu-Ti, Ag-Cu-In-Ti, etc., and their carbide (Cr3C2, B4C, etc.) particles reinforced composite brazing materials, etc. [7-9], but the melting point and high-temperature strength of Ag-based metal brazing materials are lower, and they cannot meet the high-temperature environment in service.
High-entropy alloys, which are regarded as one of the most promising materials for application in the 21st century, are alloys consisting of five and more alloying elements in equal or near-equal amounts; medium-entropy alloys are alloys consisting of two to four elements, in which the content of each element is 5%-35%. In the research process of medium/high entropy alloys, it is found that high mixed entropy can effectively prevent the precipitation of brittle intermetallic compounds due to the addition of excessive amounts of other elements, and promote the formation of simple solid solutions, thus improving the overall strength and plasticity of the alloy. Some high entropy alloys have been applied to the joining of ceramics.Wang et al[10] brazed the joining of SiC ceramics using CoFeNiCrCu high entropy alloy braze.The typical interfacial organization of the joints is SiC/Cr23C6+Cu(s,s)+Si(s,s)/HEA+Cu(s,s)/Cr23C6+Cu(s,s)+Si(s,s)/ SiC. when the brazing temperature reaches 1180°C, the shear strength of the joint is up to 60 MPa. the overreaction between SiC ceramic base material and CoFeNiCrCu will lead to an excessively thick interfacial reaction layer, which will form a large stress concentration in the joint. liu et al [11] realized diffusion welding of SiC ceramics by adopting a high entropy alloy of CoFeNiCrCuTi as the intermediate layer. The typical organization of the joint interface is SiC/Cr23C6/HEA+TiC/Cr23C6/SiC. SiC ceramic weldments with a flexural strength of 54 MPa were obtained at a welding temperature of 1125°C. The SiC ceramic weldments with a flexural strength of 54 MPa were obtained at a welding temperature of 1125°C. The SiC ceramic weldments were obtained at a welding temperature of 1125°C.
NiCoCr meso-entropic alloy is face-centered cubic structure with high melting point, excellent plastic deformation ability, and high temperature organizational stability [12].NiCoCr meso-entropic alloy can be made to have good wettability with SiC because of the presence of the active element Cr. Therefore, the application of NiCoCr alloy as brazing material for joining SiC ceramics is expected to obtain high temperature resistant SiC ceramic joints. Based on this, in this study, the wetting test of NiCoCr medium entropy alloy on SiC ceramics was carried out firstly, and then it was adopted as brazing material for brazing connection of SiC ceramics, and the microstructure and strength of the joints were analyzed.
1 test materials and methods
1.1 Test materials
The pressureless sintered SiC ceramics are made into 8mm×8mm×8mm square specimens, and the cut silicon carbide specimens are successively polished with 400#, 1500# and 3000# diamond polishing discs in sequence, and finally polished with 1μm diamond lapping solution.
The Ni, Co, Cr pure metal blocks with purity greater than 99% were weighed according to the atomic ratio of 1:1:1, and placed in the suspension melting furnace for 8 times to obtain NiCoCr alloy ingot blocks with uniform composition. Using wire cutting to make 8mm × 8mm × 0.5mm sheet, sandpaper grinding surface, and finally get 8mm × 8mm × 0.12mm sheet brazing material.
1.2 NiCoCr/SiC wetting test
A high-temperature vacuum contact angle tester was used to measure the change of the wetting angle of NiCoCr with the temperature as well as the holding time during the wetting and spreading process on SiC ceramics, and it was recorded from the time when NiCoCr appeared in the liquid phase, and it was recorded every 10s.
1.3 SiC/Ti/NiCoCr/Ti/SiC brazing test
Sandpaper was used to polish the surface oxides of titanium foil cleanly, and then SiC ceramics, NiCoCr alloy and titanium foil were assembled according to the order of SiC/Ti/NiCoCr/Ti/SiC, and put into a vacuum tube furnace to carry out the brazing test, in which the thickness of titanium foil was 30 μm, the brazing temperature was The temperature of brazing connection is 1380~1400℃, and the holding time is 10min. The samples are cut by internal circular slicer and polished by diamond, and the standard specimen with the size of 2mm×1.5mm×14mm is finally obtained.
1.4 Characterization of the microstructure and mechanical properties of the joints
Gemini500 scanning electron microscope was used to analyze the morphology of the brazing interface organization and the morphology of interfacial reactants; scanning electron microscope spectral analyzer was used to conduct elemental analysis of the brazing interfacial reaction products, to determine the atomic percentage of various elements.
The three-point bending strength of brazed joints was tested using a material universal testing machine. During the bending test, the loading rate of the testing machine was 0.1 mm/min. 3 measurements were taken for each group and the average value was taken.
2 results and discussion
2.1 NiCoCr/SiC ceramic wetting interface reaction
Fig. 1 shows the wetting results of NiCoCr alloy on SiC ceramics under the condition of 1350°C and 2 min of insulation. As can be seen from Fig. 1(a), the shape of NiCoCr wetting on the SiC ceramic surface is nearly circular, and the radius of the circle is 2.5 mm, i.e., the final wetting area is 19.6 mm2. Fig. 1(b) shows the results after cutting along the cutting line in Fig. 1(a), and it can be seen that the alloy is detached from the surface of the SiC ceramic after wetting. Figures 1(c) and 1(d) show the initial state and the final state of NiCoCr alloy on SiC ceramics after wetting, and the equilibrium contact angle between NiCoCr alloy and SiC ceramics was measured to be 30°.
Figure 2 shows the SEM morphology of the interface organization of NiCoCr medium entropy alloy wetted on SiC ceramics, it can be seen that the interface reaction is intense, the composition delamination is obvious, and cracks appeared in the edge region of the alloy in contact with SiC ceramics, which is due to the different coefficients of thermal expansion of the metal and ceramics [13], and in the process of solidification and contraction of metal alloys, the residual thermal stresses were concentrated in the reactive layer of alloy-ceramic bonding neighborhood, resulting in cracks sprouting from the edges of the alloy-SiC bonding region. As the solidification of the alloy proceeds, the accumulation of residual thermal stresses increases, and cracks expand along the reaction layer neighborhood, ultimately leading to alloy dislodgement during the diamond cutting process. As can be seen in Fig. 2(a), the cross-section of the solidified wetted sample can be divided into three layers depending on the degree of lining, with layer I being white, layer II being gray, and layer III being black, where layer III is the interface reaction layer. In order to determine the composition of the physical phase in different layers, an energy spectrum analyzer was used for elemental analysis of the interface of the wetted sample. The elemental distribution of each component is shown in Fig. 2(f) to Fig. 2(j), C element is mainly enriched in the interface reaction layer between alloy and SiC, i.e., layer Ⅲ, Si, Co, Ni elements have the same distribution pattern, mainly distributed in layer Ⅰ and Ⅲ, and Cr element is mainly enriched in layer Ⅱ, which is because in the process of brazing, the strong carbide-forming element Cr will diffuse to the area of more graphite. Figure 2(e) shows the results of the line scanning of the elements corresponding to the delineated area, and it can be seen that the peak intensity of the C element is higher in the Ⅲ layer area, the peak intensity of the Cr element is higher in the Ⅱ layer area, and the peak intensities of Ni, Co, and Si are more stable in the whole scanning area.
The reaction between molten metal and SiC at high temperature is very complex and can be roughly divided into the following 2 reactions [14], namely
M+SiC→Silicides+C(graphite) (1)
M+SiC→Silicides+Carbides+MxSiyCz (2)
During the process of vacuum heating, when NiCoCr appears in the liquid phase, the first type of reaction (reaction 1) occurs between elemental Ni and Co and SiC, i.e., decomposition of SiC occurs under the promotion of elemental Ni and Co: SiC→ C(graphite)+Si, and then the elements Ni and Co combine to form metal silicides: Ni-Si, Co-Si, or Ni-Co-Si. At the same time, the element Cr reacts with SiC in a second type of reaction (Reaction 2), i.e., the reaction produces Cr-C, Cr-Si, and Cr-Si-C ternary compounds.
Table 1 gives the analytical results (atomic percentage) of the chemical composition of each phase region of the three layer zones of the NiCoCr alloy with SiC wetting reaction samples, where the C content is an inferred value. The atomic percentage of C content in test zone 7 is 96.10%, and it can be inferred that the black phase region in the Ⅰ layer zone is the graphite generated by the reaction between NiCoCr and SiC, because the solid solubility of C in Ni and Co is particularly small, and when the amount of graphite generated by the interfacial reaction exceeds the solubility of C in Ni and Co, then graphite is precipitated in the alloy at this time [14]. Graphite is inherently brittle, and if a brazed joint contains a large amount of graphite, it may degrade the mechanical properties of the joint. The light gray areas corresponding to test area 1 and test area 6 contain a major portion of C, Cr and Si elements, and it can be inferred that the light gray phase is mainly composed of Cr-Si compounds and Cr-C compounds. Test area 2 corresponds to the dark gray phase area, and the content of Ni, Co, and Si elements in this area is basically 0. It can be inferred that the dark gray phase area is composed of Cr-C compounds only. The test area 3 and test area 4 of the Ⅰ layer area, the test area 5 of the Ⅱ layer area and the test area 8 of the Ⅲ layer area are all located in the white phase area, and the content of Ni, Co, Si three kinds of atomic percentage is basically the same, so it can be inferred that the white phase area is basically composed of (Ni, Co)xSiy compounds.
2.2 Interfacial organization of brazed joints
Figure 3 shows the interfacial microstructure and elemental distribution of SiC ceramic joints obtained by brazing with NiCoCr medium-entropy alloy under the condition of holding temperature of 1400℃ for 10min. As can be seen from Figure 3, the NiCoCr/SiC brazing interface organization is similar to that of the wetting interface in Figure 2, with a strong interfacial reaction and the formation of graphite and silicides. From the above wetting and brazing test results can be seen, because NiCoCr entropy alloy containing a large number of Ni and Co and SiC intense interfacial reaction and produced a large number of metal silicides and graphite phase, and there are microcracks near the interfacial layer, so the direct use of NiCoCr alloy reaction connection with SiC is not conducive to obtaining a good performance of the brazed joint.
The metallurgical behavior of the weld bond interface has an important influence on the bonding properties of the interface. Studies have shown that the addition of V element to Co-based or PdNi-based alloys can effectively alleviate the intensity of the interfacial reaction between the alloy and SiC [13]. Because V element belongs to the strong carbide-forming elements, can be combined with the carbon generated in the reaction process to generate V2C, can effectively control the content of residual graphite in the interfacial reaction layer, and then obtain a good interfacial structure.Ti and V have similar properties, the same is a strong carbide-forming elements, easy to react with graphite to generate TiC, and the brazing material containing Ti element is conducive to the SiC surface to obtain a good wettability. In summary, the test was carried out on NiC surface. In summary, the test in NiCoCr entropy alloy on both sides plus a layer of Ti foil (thickness of 30μm) to form Ti/NiCoCr/Ti composite interlayer, and SiC ceramics assembled into a SiC/Ti/NiCoCr/Ti/SiC structure, the metallurgical reaction of the brazing interface is regulated in an attempt to obtain an interface with no residual graphite and excellent bending strength of the SiC brazed joints. The results are summarized in the following table.
The SEM morphology and XRD analysis of the brazed joints obtained at 1380°C with a holding time of 10 min are shown in Fig. 4. By observing the SEM morphology of SiC/Ti/NiCoCr/Ti/SiC brazed joints, it is found that compared with the microstructure of SiC ceramic joints brazed with NiCoCr alloy, there is no black-phase graphite in the interfacial reaction layer between brazed joints and SiC ceramics, i.e., it can be inferred that the reaction-generated graphite is effectively eliminated in the complex interfacial reaction between composite brazing material and SiC ceramics. Effectively eliminated. According to the shape and color of the phases present in the brazing seam, the brazing seam organization shown in Fig. 4(a) can be intuitively divided into a continuous gray phase near the interfacial layer, and a diffusely distributed gray phase, a black-gray phase, and a white matrix phase in the joint.
Fig. 4(d) shows the results of the elemental energy spectrum line scanning of the brazed joint, and it can be seen that the Si element almost diffuses to the whole brazed joint, which is due to the fact that SiC decomposes at high temperatures with a smaller Si radius and has a larger activation energy during the vacuum heating process, and thus continuously diffuses to the middle of the brazed joint on the SiC side.The enthalpies of mixing of Ti and C, Ni, Co, and Cr are -109kJ/mol, -35kJ/mol, -35kJ/mol, -35kJ/mol, -35kJ/mol, and -35kJ/mol, respectively. 35kJ/mol,
-28kJ/mol and -7kJ/mol, and the mixing enthalpies of Cr and C, Ni, and Co are -61kJ/mol, -7kJ/mol, and -4kJ/mol, respectively, so that Cr and Ti will preferentially react with C decomposed from SiC. When the scanning area passes through the black-gray phase, the relative intensity of the diffraction peaks of Ti and C elements rises significantly, combined with the elemental analysis of the corresponding points in the SEM morphology (see Table 2), the atomic ratio of C and Ti in the black-gray phase is close to 1:1, and it can be speculated that the black-gray phase in the brazing seam may be TiC. C atoms have a higher diffusion rate compared with Si atoms, so they diffuse from the base material into the brazing seam and combine with Ti atoms to form TiC. C atoms have a higher diffusion rate than Si atoms, so they diffuse from the base material into the brazed seam and combine with Ti atoms to form TiC.
Cr elements are mainly distributed in the gray areas on both sides of the brazed seam. Combined with the EDS line scans of the brazed seam and the analysis of the elemental compositions of the EDS test area 1, the gray phase may consist of Cr-Si and Cr-C compounds, which have a wide range of species and complex reactions [14], and combined with the analysis of XRD of the fracture, the presence of Cr5Si3 and Cr-C compounds in the brazed seam. Cr5Si3 and Cr23C6, it can be inferred that the following reactions may occur in the brazed seam [15]
Cr+SiC→Cr23C6+Cr5Si3 (3)
The lowest Gibbs free energy is required for a series of possible reactions between Cr and SiC, which further proves that the Cr-Si and Cr-C compounds in the brazing seam are most likely to be in the form of Cr23C6 and Cr5Si3. The metal carbide Cr23C6 has the transition property between metal and non-metal, which can alleviate the mismatch of the coefficient of thermal expansion (SiC: 4.1×10-6/K, Cr23C6: 10.1×10-6/K) between the metal brazing layer and SiC ceramics to a certain extent. The mismatch between the coefficient of thermal expansion of the metal brazing layer and the SiC ceramic (SiC: 4.1×10-6/K, Cr23C6: 10.1×10-6/K) can be alleviated to some extent. At the same time, the presence of Cr23C6 prevents the crack extension as well as increases the strength of the joint.
According to the results of the elemental line scan analysis of the brazed joints shown in Fig. 4(d), the diffraction peak intensities of the three elements Ni, Co, and Si are higher in the white phase region of the brazed joints, and the pattern of the diffraction peak intensities of the three elements is consistent, so it can be inferred that the white phase region should be a compound composed of the three elements Ni, Co, and Si. The elemental point analysis of the white phase region and the XRD analysis results of the brazing seam are shown in Fig. 4(b), and it can be inferred that the white phase region in the brazing seam should be (Ni, Co)2Si.When the EDS line scans through the diffusely distributed gray phase in the brazing seam, the diffraction peak intensities of Co and Si increase at the same time, and the heights of the other elements decrease significantly, and it can be inferred that the diffusely distributed striped gray phase in the brazing seam is a compound of the elements Co and Si. It can be assumed that the gray phase diffusely distributed in the brazing seam is a binary compound composed of elements Co and Si. Based on the elemental point analysis of this test area and the XRD analysis of the fracture, it can be inferred that the phase area may be Co2Si, i.e., SiC and Co occurred during the brazing process as follows reaction [13-16]
SiC+2Co→Co2Si+C(graphite) (4)
2.3 Brazed Joint Strength
Fig. 5 shows the brazed joints obtained by adopting the NiCoCr medium-entropy alloy and Ti/NiCoCr/Ti composite interlayer Flexural strength of SiC ceramic joints obtained by brazing, as well as the flexural strength of joints from other literature. As can be seen from Fig. 5, the strength of SiC ceramic joints brazed with NiCoCr medium-entropy alloy is 35.4 MPa, while the strength of joints brazed with Ti/NiCoCr/Ti composite interlayer is 85.6 MPa. The reason for the higher strength of joints brazed with composite interlayer can be attributed to two points: 1) there is no residual graphite between the interface between brazing alloy and SiC base material, and the interface between the two is not as strong as that between the brazing alloy and SiC base material, and the interface between the two is as strong as that between the brazing alloy and SiC base material. The mutual embedding and occlusion between the two interfaces makes the joint consume more energy when fracturing; ② The appropriate amount of TiC particles can regulate the thermal expansion coefficient of the brazing metal, alleviate the residual stress concentration phenomenon caused by the mismatch of the coefficients of thermal expansion between the base material and the brazing material at the interface, and effectively prevent the cracks from sprouting and expanding. At the same time, the appropriate amount of TiC particles as a reinforcing phase distributed in the brazing seam in the NiCo base alloy, so that the brazing seam metal strength; and because NiCo base metal matrix has a certain plastic deformation capacity, in the process of fracture of the joints, NiCo base alloy through the plastic deformation of the relief of the stress concentration, the brazing joints with high strength and a certain degree of plastic deformation capacity can withstand higher loads.
Meanwhile, the flexural strengths of SiC ceramic joints brazed using high melting point Co- and Ni-based brazing materials and high entropy alloy brazing materials reported in other literatures are given in Fig. 5.Wei et al [17] achieved SiC ceramic joints using Co-Si-V-Ti brazing materials under brazing processes with different joining temperatures (1200-1300°C) and holding times, and due to the fact that the tissues in the region of the brazed joints were dominated by CoSi2 and VSi2 are two brittle compounds, which adversely affect the strength of SiC ceramic joints, and the maximum room temperature flexural strength of the obtained joints was only 43 MPa. Chen Bo et al [18] brazed the SiC ceramics using Pd-Co-Ni-V-Si-B brazing material under the condition of holding time of 10 min at 1190°C, and the joints at the interface were mainly composed of Pd2S, CoSi (or Co2Si) and graphite phases, the brittle (Co, Ni)2Si phase was effectively divided into small regions, which effectively alleviated the brittleness of the SiC ceramic joints, and V reacted with part of the graphite to form the V2C phase distributed in the central part of the weld joints, and the joints had a room-temperature flexural strength of 52 MPa.Li Wenwen et al[19] used Co-Nb-Pd-Ni-V cobalt-based brazing to braze the obtained Cf/ SiC composite joints had a flexural strength of 68.1 MPa, Liu et al [11] also found more graphite phases and silicides in SiC ceramic joints brazed with Co-Fe-Cr-Ni-Cu-Ti high entropy alloy, and the joints had a flexural strength of 54 MPa. Mao et al [20] realized SiC ceramic joints using Ni-51Cr alloy, and the joints had a flexural strength of 74.2 MPa. In summary, the SiC ceramic joints prepared using Ti/NiCoCr/Ti composite brazing material in this experiment have higher flexural strength than the brazed joints prepared using Co-based and Ni-based brazing materials.
3 Conclusion
(1) NiCoCr medium entropy alloy and SiC ceramics both have good wettability, a strong chemical reaction occurs under the condition of 1350 ℃ heat preservation for 2min, the interface reaction layer contains a large number of graphite and brittle metal silicides.
(2) NiCoCr medium entropy alloy was used to realize the brazing connection of SiC ceramics, similar to the wetting test, a strong interfacial reaction occurred at the interface of NiCoCr and SiC and formed a graphite phase and silicide, and the flexural strength of the joint at room temperature was 35.4 MPa.
(3) The brazed connection of SiC ceramics was realized by using Ti/NiCoCr/Ti composite interlayer, and the interfacial organization of the joint was SiC/Cr23C6+Cr5Si3/TiC+(Ni,Co)2Si/Cr23C6+Cr5Si3/SiC, and the room-temperature flexural strength of the joint was 85.6 MPa.
References: Issue 5, Rui Zhu et al: NiCoCr Study on wettability and organization properties of brazed joints between medium entropy alloy and SiC ceramics
NiCoCr medium entropy alloy powder is a ternary alloy powder with nickel (Ni), cobalt (Co) and chromium (Cr) as the main components (usually iso-atomic ratio or nearly iso-atomic ratio), and its core feature is the formation of a single face-centered cubic (FCC) solid solution structure, which possesses a good balance of high-strength and high-plasticity, and especially maintains the excellent mechanical properties under the environment of ultra-low temperature. The powder can be prepared by atomization method into spherical or nearly spherical particles, good fluidity, high bulk density, suitable for additive manufacturing process; through mechanical alloying1, elemental doping (such as vanadium, tungsten, titanium) or oxide dispersion reinforcement (eg, Y₂O₃) can be further enhanced performance, for example, the addition of Y₂O₃ formation of ODS alloy at 1093 ℃ under the tensile strength of traditional nickel-based alloys to increase by two times, the creep life of more than a thousand times. by more than a thousand times. Applications include
Aerospace: as a reinforcing phase for the preparation of high-strength titanium matrix composites1 or for ultra-low-temperature components (e.g. liquid hydrogen engines);
Nuclear industry: as a structural material for nuclear reactors due to its excellent resistance to radiation hardening and helium cavity growth;
Surface engineering: composite with chromium carbide and other ceramics to make nuclear shell structural powders and prepare high-temperature wear-resistant coatings;
Additive manufacturing: high performance high temperature components, such as hot end components of space engines, are melted and shaped by laser powder bed.
More metal powder consulting, welcome to contact our professional staff, Manager Zheng 13318326187.