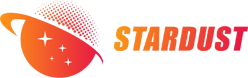
1. Introduction
Generally, niobium (Nb) based alloys withstand high stresses at elevated temperatures. These alloys also exhibit good formability and welding properties. Another advantage of Nb is that it possesses the lowest density (8.57 g/cc) amongst the refractory metals (Mo, Ta, W and Rh). On account of these properties, Nb alloys find extensive use in aerospace applications; such as in rocket nozzles, propulsion systems and turbine blades etc. Further,the Nb–Hf–Ti ternary alloy system is widely used in high temperature propulsion systems due to their excellent physical,thermal and mechanical properties up to 1300 1C [1–2]. In particular, C-103 alloy with a major composition of Nb–Hf 8.3–Ti1.0,which belongs to the above alloy system, is used in light-weight space propulsion systems.
Commercially pure (CP) Nb exhibits the dynamic strain aging (DSA), a phenomenon in which dislocations get anchored by the diffusing solute elements either due to elastic or chemical interaction in the intermediate temperature range (300–500 1C) [3–8].Szkopiak and Co-workers [4–6] investigated the role of interstitial solute elements (carbon, nitrogen, and oxygen) at different temperatures for the occurrence of DSA. Park et al. [7] have reported the most likely mechanism for DSA in CP-Nb. Shelly [3] in early 1960s, on the other hand, has studied the compressive properties of CP-Nb up to 1200 1C and showed that the effect of DSA is lost beyond 700 1C. Creep behaviour [9] and effect of oxidation on tensile properties [10–11] of C-103 alloy have also been reported. However, to the best of authors' knowledge, the high temperature (up to 1200 1C) tensile properties of this alloy have not been investigated.
In the present study, the quasi-static tensile properties of C-103 alloy are studied in the temperature range between RT and 1200 1C at a strain rate of 10 2 s 1. The DSA, deformation and fracture behaviour at high temperatures are discussed in detail.
2. Experimental methods
Alloy C-103 was received from M/s. TJTM, U.K in form of sheets with thickness 3 mm, which were cold-rolled and annealed. The nominal chemical composition of this alloy is listed in Table 1.Flat tensile specimens of 25 mm gauge length as per ASTM E 8M [12] were cut from these sheets using electric discharge machining (EDM) technique wire cut machine. Subsequently, these test coupons were heat-treated in vacuum at 1400 1C for 1 h followed by furnace cooling. The tensile specimens before testing and after testing at high temperatures (fractured) are shown in Fig. 1. Three specimens are tested for each test conditions and the average values are reported.
Tensile testing was carried out in a computer controlled thermomechanical simulator (GLEEBLE-3500C) at ambient temperature and in the temperature range between 600 1C and 1200 1C at the strain rate of 10 2 s 1. The polished surface of as received and post tested specimens was etched using a chemical solution comprising 30 ml HF, 15 ml HNO3, 15 ml HCL and 10 ml H2O. The microstructure of etched sample was examined using an optical microscope (Olympus). Planimetric method was used to examine size and volume fraction of the microstructural constituents. Elemental mapping was carried out using a scanning electron microscope (SEM) equipped with an electron backscattered diffractometer (EBSD) (SUPRA 55, Zeiss Germany). The specimens were examined under scanning electron microscope (Quanta 400 FEI) to study the deformation and fracture behaviour.
3. Results and discussion
The microstructure of the alloy in the vacuum heat-treated condition is shown in Fig. 2. The grain sizes for relatively finer and coarser grains were determined to be 30 mm and 60 mm,respectively. The secondary electron micrographs as shown in Fig. 2b and c clearly show the presence of spheroidal shaped precipitates which are larger in size as compared to much finer precipitates. The fine precipitates are decorated along the grain boundaries and relatively coarser precipitates lies within the grains. An attempt has been made to identify the spheroidal shaped precipitates by elemental mapping as shown in Fig. 3. Fig. 3 shows the preferential enrichment of hafnium and oxygen into these precipitates, which are due to the formation of hafnium dioxide [11].
The plastic region of engineering stress–strain plots at room temperature and in the temperature range of 600–1200 1C is shown in Fig. 4. Furthermore, the comparison of stress–strain plots in the temperature range 600–1200 1C is shown in Fig. 5. It is evident from Figs. 4 and 5 that the alloy exhibits well-defined yield point and flow oscillations in the plastic region of the stress– strain plot. These flow oscillations are identified as ‘serrations’ of the type AþB at RT, B at 600 1C and 800 1C, BþC at 900 1C, B at 1000 1C, BþC at 1100 1C and B at 1200 1C, respectively. Type A serrations are considered as locking serrations, characterised by an abrupt rise followed by a drop to below the general level of stress strain curve. Type B serrations are oscillations above the general level of the stress strain curve that occur in the quick succession due to discontinuous band propagation arising from the DSA of the moving dislocations within the band. However, Type C serrations are yield drop that occur below the general level of the flow curve and are therefore considered to be due to dislocation unlocking. The serrations of type A and B have been reported for CP Nb [7]. The amplitude of serrations is a function of temperature, strain rate and magnitude of deformation [13]. In the present study, the amplitudes were measured at a strain of 0.05 for various testing temperatures and the same are listed in Table 2. It is found that the amplitude of serrations is maximum at 600 1C and it decreases above 900 1C.
The 0.2% yield strength (0.2% YS), ultimate tensile strength (UTS), and percentage elongation (% El) of the alloy at different temperatures are presented in Table 3. The variation of 0.2% YS and UTS with temperature is shown in Fig. 6. As expected, the alloy shows better tensile properties (0.2% YS and UTS) at room temperature as compared to that at elevated temperatures (600–1200 1C). The ratio of UTS to 0.2% YS, which is a representative of work hardening is presented in Table 3. Interestingly, the UTS/0.2% YS and % El show a local maximum and minimum, respectively, at 600 1C. Further, it was found that the 0.2% YS remains almost insensitive to the temperature between 600 1C and 1200 1C; whereas the UTS remains nearly the same both at 600 1C and 800 1C; beyond which it decreases gradually up to 1200 1C. The serrated flow behaviour as shown in Fig. 4 and the temperature insensitivity of 0.2% YS are the typical manifestations of dynamic strain aging (DSA) [14]. It is confirmed in the present study that the alloy, C-103 exhibits DSA from room temperature to 1200 1C with predominant effect up to 900 1C.
The SEM fractographs of the fracture surfaces of the tensile specimens tested at different temperatures are shown in Fig. 7. The fracture surface of the specimen tested at RT shows dimple features (Fig. 7a). This essentially indicates the ductile mode of fracture which can be corroborated by the fact that the total fracture strain at RT is 58%. The fracture surfaces showed similar features (facets) for the specimens tested at temperatures between 600 1C (Fig. 7b) and 900 1C. However, at elevated temperatures between 1000 1C and 1200 1C (Fig. 7c), intergranular fracture is observed. In order to understand the tensile fracture mechanism, the microstructure of the alloy has been examined near the features are not seen in the specimen tested at 600 1C (Fig. 8a). Fig. 9b clearly shows the characteristic signature of intergranular cracking along the oxide enriched zone. This indicates oxidation of the alloy near the grain boundaries above 1000 1C. The fracture features observed in the temperature range of 600–900 1C are attributed to the DSA induced inhomogeneous deformation as grain boundaries are preferred sites for DSA [14]. Qualitatively, it is reasonable to consider that the amplitude of serrations is related to the available solute atmosphere during the pining process of DSA. Since the amplitude of serrations is significantly higher at 600 1C as compared to other test temperatures, the strength of DSA is expected to be higher at 600 1C. Minimum ductility (8.0%) at 600 1C could be attributed to the intense strain localisation due to hopping bands of B-type at 600 1C.
In the present study, based on the qualitative inference from the shape of stress–strain plots as shown in Fig. 5, amplitude of serrations as listed in Table 2, the trend of UTS/0.2% YS ratio (representative of work hardening) as listed in Table 3, and fracture features, it is clear that the effect of dynamic strain aging is dominant up to 900 1C. Apart from the effect of oxidation, dynamic recovery appears to nullify the effect of DSA beyond 1000 1C where plastic instability sets in at a much early stage at 1200 1C (Fig. 5).
The tensile behaviour of the C-103 alloy is schematically shown in Fig. 10. The alloy exhibits serrations in the plastic region of stress– strain curve at high temperatures, which are manifestation of DSA. The DSA effect is found to be predominant between the temperature range of 600–900 1C and found to be weak in temperature range 1000–1200 1C. Change in types of serrations often provides insight about the role of solute elements for the occurrence of DSA. The likely cause of DSA is the diffusion of oxygen and elements like, carbon and nitrogen to lesser extent due to their lower diffusion coefficients (C: 2.59 10 22 cm2 s 1 , N: 4.07 10 23 cm2 s 1 [7]) than that of oxygen (O: 6.47 10 18 cm2 s 1 [7]) into the alloy and the diffusion of elements to the interstitial positions is more pronounced at high temperatures. Dynamic recovery and oxidation influence the tensile properties in the temperature range 1000–1200 1C.
4. Conclusions
The C-103 alloy exhibits serrated flow behaviour in the temperature range from room temperature to 1200 1C.
Dynamic strain aging has dominant effect on tensile properties up to 900 1C, beyond which dynamic recovery and oxidation predominantly influences the tensile properties.
Paper citation information:
Materials Science & Engineering A 620 (2014) 286–292
Spherical C103 alloy powder (Nb-10Hf-1Ti) is a refractory metal alloy powder with niobium as the matrix and 10% hafnium and 1% titanium added.
Stardust Technology uses radio frequency plasma spheroidization technology to prepare spherical C103 alloy powder, which has excellent high temperature performance and processing adaptability. It can be used in the fields of aerospace and extreme environments, nuclear industry and energy, chemical industry and marine engineering, electronics and high-end manufacturing, biomedicine and other fields.
https://www.stardustpowder.com/niobium-hf-alloy15-53mm
To learn more about the performance of spherical C103 alloy powder, please contact Vicky at +86-13318326185