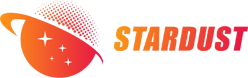
As a refractory metallic material with a body-centered cubic structure, tantalum is used in a large number of applications in the electrical and electronics industry, especially as a capacitor that needs to store a large amount of potential energy, due to the high reactivity of tantalum with oxygen and nitrogen atoms, which results in the formation of an oxide film layer of Ta2O5 with a high dielectric strength on the surface [1,2]. In addition, tantalum is chemically inert and has excellent corrosion resistance, which also allows it to be used in the manufacture of surgical implants and chemical equipment [3]. However, tantalum has a high melting point (2996°C), which is 1.8 times higher than that of titanium (1668°C), and good thermal conductivity, with a coefficient of thermal conductivity (57.5 W-m-1-K-1) that is 3.8 times higher than that of titanium. Therefore, it is difficult to form and process complex components of tantalum metal. In the past 50 years, most tantalum metal components were manufactured by using powder metallurgy or electron beam melting to obtain tantalum metal ingot billets, and then plastic deformation, welding and heat treatment to obtain the final product [4,5]. However, this is obviously unable to meet the urgent needs of industrial upgrading and personalized medicine for complex tantalum metal components such as porous tantalum implants.
In recent years, digitally driven advanced manufacturing processes have ushered in a period of high-speed development, and the powder bed fusion additive manufacturing equipment and processes represented by laser selective zone melting (selectivelasermelting, SLM) and electron beam selective zone melting (selectiveelectronbeammelting, SEBM) have been maturing, and the production of their titanium alloy parts in the medical, aviation, aerospace and other fields has achieved large-scale applications, providing a new process for the manufacture and production of metal tantalum [6,7]. Compared with the traditional processing technology, additive manufacturing technology has obvious advantages in the processing of metal tantalum [8-11], such as: high material utilization, the three-dimensional model of the component as a template makes the size of the blank part close to the final product, reduces the machining allowances, and reduces the cost of production; the machining process is simplified and shortened to improve the production efficiency, and personalized customization is possible. Therefore, the use of additive manufacturing technology to prepare tantalum metal components, to achieve high-quality forming of complex components of tantalum metal, to meet the industrial upgrading as well as personalized diagnosis and treatment services, has an important scientific value and application value.
This paper mainly introduces the current research status of tantalum powder raw materials for additive manufacturing, reviews the microstructure and mechanical properties of tantalum metal prepared by additive manufacturing technology, and then discusses the current research and application status of porous tantalum materials for medical use in additive manufacturing in combination with the relevant work of the author's team, analyzes some of the current problems of tantalum metal additive manufacturing technology, and puts forward suggestions for the future development of tantalum metal additive manufacturing technology.
1 The current situation of tantalum powder raw material for additive manufacturing
Metal powder is the raw material basis of additive manufacturing technology, and spherical powder with excellent fluidity and high packing density is the preferred raw material for additive manufacturing technology [12,13]. However, due to the high melting point of tantalum metal, it is difficult to realize the preparation of spherical tantalum powder by traditional spherical powder preparation processes, such as: aerosolization and other methods. On the other hand, the traditional preparation process of tantalum powder for capacitors, such as sodium potassium fluorotantalate reduction method, hydrogenation crushing and other methods, the resulting powder particle size is too small (<10 μm), complex shape and basically no mobility, which can not meet the process requirements of additive manufacturing technology [14].
With the maturity of additive manufacturing equipment and the increase in the demand for complex components made of refractory materials, research institutions and powder manufacturing enterprises in various countries have invested a great deal of energy in the process development of spherical tantalum, tungsten and molybdenum and other refractory metal powders since 2015 [15-17]. Table 1 gives the basic performance parameters of spherical tantalum powders commercialized by relevant enterprises in various countries. It can be seen that spherical tantalum powders are mainly prepared by plasma spheroidization (plasmaspheroidization, PS) and plasma rotating electrode atomization (plasmarotatingelectrodeprocess, PREP) technologies.
Canadian TENKA [20,21], as a global pioneer in the commercialization of plasma spheroidization technology (Fig. 1a), achieved commercial sales of additively manufactured spherical tantalum powders in 2015, and the U.S. GlobalAdvancedMetals, as well as China's University of Science and Technology Beijing, Northwest Research Institute of Nonferrous Metals, and Stardust Science and Technology, have also successively have prepared spherical tantalum powder using plasma spheronization (PS) technology, as shown in Figure 1c (cited from the official website of Stardust Technology). However, PS technology has large investment in equipment, high operating costs, and the technology is to manufacture powder as raw material, which limits the scale production and application of this type of powder due to cost and other factors.
PREP technology is currently one of the main methods for industrial production of high-quality spherical metal powders, as shown in Figure 1b and Figure 1d. Compared with PS technology, PREP technology is based on metal rods as raw materials, which has obvious advantages in the control of production cost, powder morphology and impurity content; however, the powder yield below 45 μm in the powder produced by PREP technology is generally less than 10%, which is difficult to meet the demand of SLM technology [19]. Therefore, further improving the fine powder yield of PREP technology through equipment upgrading and process optimization is the main challenge for this technology in the field of additive manufacturing.
2 Research status of additive manufacturing tantalum metal
In 2008, Fox et al [23] from the University of Liverpool, UK, prepared tantalum metal coatings on the surface of CoCr alloy using SLM technology for the first time, and since then, the research on additive manufacturing of molded tantalum materials has begun to become a hot spot in the field. From the technical point of view, the main technologies are laser selective zone melting, electron beam selective zone melting, and arc-fed wire additive manufacturing. As a pure metal material, tantalum has a relatively simple organization evolution law during the forming process. Therefore, according to the reported structural forms of tantalum metal, the current research status of solid tantalum and porous tantalum are described respectively.
2.1 Organization and properties of metallic tantalum prepared by additive manufacturing technology
The microstructure of metallic tantalum prepared by additive manufacturing process is given in Figure 2. It can be seen that through the optimization of process parameters, the internal defects of tantalum metal prepared by additive manufacturing technology at this stage have been effectively controlled, and the densities are all up to 99.9% or more [18,22,24-27]. Same as most of the metal materials prepared by additive manufacturing, the microstructure of tantalum metal also shows a coarse columnar crystal structure with epitaxial growth along the growth direction. Among them, the columnar crystals of the material formed by SEBM technology are the most distinctive, as shown in Fig. 2c, the width of the columnar crystals is 165.22 ± 3.44 μm [22].
The recent results of Zhou et al [26] showed that the organization of tantalum metal formed by SLM technology will be transformed from coarse columnar crystals to equiaxed crystals after triple high-temperature annealing, which is crucial for eliminating the anisotropy of additively manufactured metallic materials, as shown in Fig. 3. The authors believe that it is because the high-temperature annealing eliminates the huge internal stresses inside the SLM formed parts, while the dislocation motion is fully activated at high temperatures, and the dislocation slip or climb that occurs provides the necessary conditions for the transformation of the columnar crystals to the equiaxial crystals.
Figure 4 analyzes the room temperature mechanical properties of the additively manufactured tantalum metal material. According to the relevant material standards, an oxygen content of 300 µg/g is the upper limit of oxygen content in tantalum. Therefore, in order to systematically illustrate the mechanical properties of additively manufactured tantalum metal, the yield strength and elongation versus oxygen content are presented in Figs. 4a,4b, respectively. It can be seen that the oxygen content of some of the additively manufactured tantalum metals exceeded the upper limit specified in the standard due to the powder preparation technology at the early stage of the study. On the other hand, the oxygen content of the powder used in the SEBM technology is low, and the yield strength of the material is basically consistent with the conventional process, while the dispersion of the yield strength of tantalum metal prepared by SLM is large. For example, the yield strength of tantalum metal with an oxygen content of 1800 µg/g [28] is lower than that of the case with a low oxygen content [18,25], which may be caused by insufficient densification due to residual pore defects within the formed samples.
From the data in Fig. 4b, it can be seen that the change rule of the elongation of tantalum metal prepared by additive manufacturing technology with oxygen content is basically consistent with the traditional preparation process [29]. With the increase of oxygen content, the elongation of the specimen decreases from 50% to about 2%, which indicates that the ductility performance of additively fabricated tantalum metal is equally sensitive to the content of impurity elements such as oxygen. Among the mechanical properties, the yield strength and elongation of the material are considered to be the main properties of tantalum in high strain rate applications [30]. According to German [31], the yield strength and elongation of tantalum metal prepared by powder metallurgy should be higher than 396 MPa and 30%, respectively. Meanwhile, with reference to the commercial tantalum manufactured by PLANSEE, Germany, the yield strength and elongation of electron beam melting and powder sintered tantalum were 390 MPa and 31% and 420 MPa and 18%, respectively [32]. Therefore, tantalum metal prepared by additive manufacturing technology still has much room for improvement in mechanical properties, as shown in Fig. 4c, especially in the reasonable matching of strength and elongation.
2.2 Properties of porous tantalum materials prepared by additive manufacturing technology
Porous tantalum is a foamy porous metal material with similar pore structure to human bone, and compared with other medical metal materials, porous tantalum has the typical properties of high volumetric porosity, low elastic modulus, and high surface friction coefficient, which makes it considered as a more desirable bone substitution material [33]. However, due to the high melting point of tantalum metal, it is difficult to achieve the processing and fabrication of complex porous structures through conventional processing until the early 1990s, when Kaplan et al [34] achieved the preparation of porous tantalum through chemical vapor deposition technology, and it was commercially marketed by Zimmer in the United States. At present, Zimmer's standardized TrabecularMetal™ series of porous tantalum products basically monopolize the tantalum metal implant market in various countries [35]. In recent years, with the gradual popularization of the concept of personalized diagnosis and treatment and the improvement of the national health awareness level, the clinical demand for personalized orthopedic implants has shown explosive growth. Therefore, after the success in titanium alloy porous plants, the use of additive manufacturing technology to prepare porous tantalum materials with structures and properties comparable to those of Zimmer's porous tantalum implants has become a hotspot of cross-research in the fields of additive manufacturing and orthopedic clinics.
Table 2 lists the structure and properties of existing porous tantalum materials reported in the literature and compared with the porous tantalum materials prepared by Zimmer using CVD technology. It can be seen that the porous tantalum materials prepared by additive manufacturing technology have pore structures in the form of 1) random-type pore structure (stochasticstructure,SS), as shown in Figure 5a. Through the control of process parameters, a high-energy beam is used to partially melt the powder material, i.e., the gaps between the powder particles are used to form a three-dimensional connecting pore; 2) the regular ordered pore structure, which can also be called the lattice structure (lattice structure, LS), as shown in Fig. 5b,5c, is a porous structure constructed by rods or plates in a similar way to the crystalline lattice structure. Random-type pore structure is realized by changing the process parameters to adjust the pore parameters, and the controllable range of its porosity and pore diameter is narrower. In contrast, dot-type ordered pore structures, which have been validated in additively manufactured titanium orthopedic implants, can autonomously design the pore structure and pore size, which fits perfectly with the concept of personalized diagnosis and treatment [40]. Therefore, using additive manufacturing technology can not only realize the same pore structure as Zimmer's porous tantalum material (Fig. 5d), but also achieve on-demand tuning of the pore structure parameters and mechanical properties by changing the 3D model design.
Mechanical properties are one of the most important technical indicators of medical metallic materials. Sufficient strength can provide support for tissue growing in, and suitable elastic modulus can effectively reduce stress shielding, thus strongly contributing to the initial stability of the implant. The mechanical properties in Table 2 were analyzed in Figure 6, and the strength of porous tantalum prepared by additive manufacturing technology was lower than that of CVD technology under the same density conditions, but both reached the strength of human cancellous bone, as shown in Figure 6a. The difference in strength is due to the 1% (mass fraction) carbon residue in the porous tantalum prepared by CVD [39], which results in much higher strength than pure tantalum. According to Gibson and Ashby et al [41], there is a certain correspondence between the relative density and strength of porous metallic materials, which can be used to guide the structural design of personalized porous implants [38,42]. However, there are fewer publicly reported data on the mechanical properties of porous tantalum materials, especially on the modulus of elasticity.
It should be noted that the international standard for tantalum metal implants, ISO13782-1996, as well as the Chinese medical industry standard, YYT0966-2014, stipulate that the upper limit of the oxygen content of tantalum implants is 300 μg-g-1; however, some of the existing reports use powder raw materials that have an oxygen content of more than 300 μg-g-1.
3 Application status of tantalum metal for additive manufacturing
The continuous maturation of equipment and processes has driven the pace of clinical application of additively manufactured porous tantalum materials forward. Due to the urgent clinical demand for porous tantalum implants and the huge market potential, during the 13th Five-Year Plan period, the author's unit, with the support of the Key Research and Development Program of the Ministry of Science and Technology, broke through a number of key technologies, such as the preparation of medical-grade spherical tantalum powder, the development of special forming equipment, and the forming and post-processing processes, and completed the world's first case of powder-bed e-beam additive in the First Affiliated Hospital of the Army Military University of Medical Sciences on April 18, 2018 manufacturing personalized porous tantalum implants for clinical application assessment. During the period from 2016 to 2020, a total of 65 cases of personalized porous tantalum implants in 5 major categories have been completed, with good clinical application results, as shown in Figure 7.
4 Summary and Outlook
Tantalum metal has excellent physical and chemical properties and is widely used in chemical, electronic, electrical and medical industries. In recent years, the popularity of additive manufacturing equipment and the maturity of the process, for the preparation of complex components of tantalum metal provides a new processing method, and has been successful in the preparation of personalized orthopedic implants. However, due to the limited research time, tantalum metal additive manufacturing also faces some challenges, including:
(1) Most of the existing spherical tantalum powders are 2~3 times more expensive than metallurgical grade tantalum powders, which greatly limits the application of additive manufacturing technology in tantalum metal processing. Therefore, reducing the production cost of the powder as well as the powder yield through the optimization of the powder preparation process is one of the challenges faced by additive manufacturing technology in the processing of tantalum metal products.
(2) After nearly five years of research, additive manufacturing of tantalum metal has made great progress in research, solving the dilemma of no powder raw materials, China has also introduced and promulgated the national standard of powder raw materials, “Tantalum and Tantalum Alloy Powder for Additive Manufacturing” (GB/T38975-2020), and the existing reported material compositions and room-temperature mechanical properties basically reach the traditional processing technology. However, it should be noted that the research of tantalum metal for additive manufacturing is still in the early stage, the material and product standards for tantalum metal additive manufacturing have not yet been introduced, and the research on the properties of dense tantalum metal is not in-depth enough, for example, the corrosion resistance, high temperature mechanical properties of the material, as well as fatigue properties and other related work has not yet been reported. Therefore, to accelerate the comprehensive performance research of tantalum metal materials, comprehensively benchmark the traditional preparation process, and formulate the material and product standards of tantalum metal for additive manufacturing as soon as possible is a systematic research work that needs to be carried out urgently for tantalum metal for additive manufacturing.
(3) Although the personalized porous tantalum implants made by additive manufacturing have been applied to the clinic, orthopedic medical implants belong to Class III medical devices, and the Food and Drug Administration of each country has a strict access approval system for medical devices. Therefore, to formalize the mass production of additively manufactured personalized porous tantalum implants, basic experimental research needs to be completed as soon as possible, in accordance with the relevant provisions of the clinical trial process and approval process, in order to promote the pace of clinical application of additively manufactured porous tantalum, and to benefit patients at an early date.
(4) The application of additively manufactured tantalum metal is currently focused on orthopedic implants, and there have been no reports of application in other fields. Therefore, combining the process characteristics of additive manufacturing technology, further promoting and expanding the application of this technology in atomic energy, aerospace and other fields is of great significance in promoting the popularization and further development of this technology.
References: (c)1994-2022 china Academic Journal Electronic publishing House. All rights reserved. http://www.cnki.net
The spherical tantalum powders prepared by Stardust Technology using RF plasma spheronization powder making equipment have a wide range of specific applications in many fields due to their excellent performance. The following are some of the main applications and their specific descriptions:
1. Medical implants
Application scenarios: 3D printing of hip joint prostheses (such as acetabular cups), bone repair implants, dental implants, and so on.
Specific description: Tantalum has excellent biocompatibility and corrosion resistance, which can integrate well with human tissues and promote the growth and healing of bone cells. Therefore, spherical tantalum powder is widely used to make implants. Through the additive manufacturing process, structures with complex geometries can be precisely customized to meet personalized medical needs.
2. Aerospace
Application Scenario: High temperature parts, rocket nozzles, spacecraft combustion chambers.
Specific description: Tantalum has a high melting point, excellent thermal shock resistance and thermal conductivity. Using spherical tantalum powder through additive manufacturing (3D printing) technology, high-temperature-resistant parts with complex structures and reduced weight can be manufactured, thus enhancing the combustion efficiency and reliability of the aircraft.
3. Chemical and microchannel reactor
Application Scenario: Heat exchangers and microchannel reactors in highly corrosive environments.
Specific description: Spherical tantalum powder can be used to manufacture the core components of microchannel reactors, which need to withstand high temperature, high pressure, and corrosive environments with strong acids and alkalis. Tantalum's chemical resistance and excellent mechanical properties make it an ideal choice for chemical equipment manufacturing.
4. Electronics industry
Application Scenario: Tantalum capacitors, film resistors.
Specific description: Tantalum's high capacitance and low leakage characteristics make it widely used in electronic components. Due to its good fluidity and high purity, spherical tantalum powder is suitable for plasma spraying or powder metallurgy process to manufacture high-performance electronic components.
5. Defense industry
Application Scenario: Military high performance armor, warheads and armor-piercing bullets.
Specific description: Tantalum's high density and excellent impact resistance make it an important application in protective and weapon materials. By using spherical tantalum powder, it is possible to prepare parts with high densities, enhancing the destructive power and durability of weapons and equipment.
6. Laboratory and scientific research
Application Scenario: High-end equipment parts and targets.
Specific description: Sputtering targets for electron beam melting, high-temperature corrosion-resistant parts in vacuum systems, and various advanced thin film materials. The high purity and uniform particle size distribution of spherical tantalum powders ensure accurate experimental results and material stability.
These applications demonstrate the importance of spherical tantalum powders in high-end manufacturing and emerging technologies. By combining it with additive manufacturing technologies, its potential uses will continue to be explored and expanded.
For more information, please contact our professional manager: Cathie Zheng +86 13318326187.