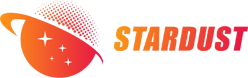
Molybdenum and molybdenum alloys have become important materials for electronic and power equipment manufacturing, metal material processing, glass manufacturing, high-temperature furnace structural component manufacturing, aerospace and defense industry applications due to their good thermal conductivity, electrical conductivity, low thermal expansion coefficient, high temperature strength, low vapor pressure and wear resistance. The application of molybdenum and molybdenum alloys in the above-mentioned fields is mainly made by machining, forming, metal processing and welding.
1 Application of molybdenum and molybdenum alloys
The electronic and power equipment manufacturing industry is the main application field of molybdenum and molybdenum alloy materials. These include filaments, lighting and electron tube components, special printed circuit board coatings, microwave devices, medical electronic power equipment, internal components of x-ray tubes (such as rotating targets, brackets and heat shields, etc.), x-ray flaw detectors, low thermal expansion materials for integrated circuit components, and "buffers" for equipment power supply and heat dissipation, silicon substrates that can replace certain components, heat-treated molybdenum sheets plated with nickel, copper or rhodium (Rh) for rectifiers, and heat sinks for pressing and sintering of small electronic components. Molybdenum (Mo) can also form Cu/Mo/Cu (CMC) composite materials with copper (Cu). Among them, Cu can improve the thermal expansion properties of the composite material, so that it can better match the ceramic matrix. The elastic modulus of this CMC component is high, so its vibration failure can be reduced. The main application areas of molybdenum and molybdenum alloys in the material processing industry are as follows.
1.1 Used for hot working molds
The aviation and aerospace sectors mainly use molybdenum alloys to make molds and for high temperature forging engine parts. The application materials are mainly three kinds of alloys: active metal carbide reinforced molybdenum, optional element reinforced molybdenum and mechanical dispersion two-phase reinforced molybdenum. Active metal carbide reinforced molybdenum alloy has
good high temperature strength and high thermal conductivity, so it is mainly used in the hot working mold industry. It is precisely because of the high thermal conductivity and low thermal expansion of molybdenum that it has become the preferred heat shock resistant material.
1.2 Used for molten metal processing
Aluminum foundries use molybdenum to restrain the thermal cracking problem of their processed materials, that is, usually using TZM (titanium-zirconium-molybdenum) alloy cores and core rods (rods) in the parts of the processed materials that are prone to thermal cracking can also avoid the thermal cracking of the materials. The use of TZM and MHC alloys can also improve the rapid solidification ability of processing equipment. Tungsten-molybdenum alloys have the same corrosion resistance, which can significantly reduce production costs. Therefore, Mo-25%W and Mo-30%W alloy materials suitable for promotion and application in impellers, pump units and molten zinc pipe systems have been developed.
1.3 For thermal spraying
Molybdenum can be used for thermal spraying of piston rings. The method is to mix molybdenum powder with a binder containing nickel (Ni) and chromium (Cr), and then spray the mixture on the piston by plasma. The coating can be pure molybdenum or a molybdenum alloy mixed powder, which is both wear-resistant and corrosion-resistant, and is therefore suitable for papermaking applications. In addition, molybdenum powder can also be mixed with different contents of nickel, chromium, boron and silicon powder to form different powder mixtures, but the spraying powder requires good fluidity. Thermal spray powder should generally be spherical or nearly spherical after spraying. In addition. Molybdenum and molybdenum alloy mixed powders can also be used in plasma nozzles to densify into pre-alloyed powders of different qualities that are more wear-resistant and corrosion-resistant.
1.4 Used for chemical treatment
The use of molybdenum as an electrode material in glass melting can also improve the processing capacity of traditional furnaces. Molybdenum is suitable for high-temperature furnace component materials due to its high-temperature strength and thermal stability. For example, molybdenum and molybdenum alloys are mostly used as hot isostatic pressing (HIP) device materials, heating elements, sleeves and brackets; ceramics generally use molybdenum fixtures and sintered molybdenum boats; oxide ceramic products produced by the electronics industry are almost all fired with molybdenum carriers. In addition, thanks to the compatibility of molybdenum with hot gases and its high-temperature strength, it can also be used in aerospace and defense industries. However, the poor oxidation resistance of molybdenum limits its application range. Molybdenum is mainly used as a component material for rockets and active gas valves with high speed and good performance.
2 Production methods of molybdenum and molybdenum alloy materials
Molybdenum and molybdenum alloy materials can be made by machining, forming, metal processing and welding. After machining, molybdenum and molybdenum alloys have a smooth surface and high precision. However, it should be noted during processing that molybdenum has high temperature strength, but poor room temperature strength, and its toughness is not as good as carbon steel or brass. Its high ductile-brittle transition temperature also means that molybdenum is prone to internal cracking. In addition, molybdenum and molybdenum alloy materials can also be processed by grinding, photolithography and discharge (EDM). EDM molybdenum surface area often forms a recrystallized layer, which is easy to produce micro-cracks and can be eliminated by mechanical or chemical corrosion polishing. However, if the cooling degree is not enough, the abrasive will overheat and produce surface cracks during grinding. Forming and metal processing are commonly used bending, stamping, punching, drawing and spinning processing methods for molybdenum and molybdenum alloys. The processing effect is related to the surface state of the processed material, the size of the forming section and the deformation rate. In addition, molybdenum and molybdenum alloys have typical plastic anisotropy, that is, when bending the molybdenum plate, the bending axis is perpendicular to the main rolling direction, and the processing effect will be better. Stamping, punching and shearing are particularly prone to plane cracks in the formed sheet. These are intergranular cracks that spread along the plane of the grain boundary during rolling. 0.5mm thick molybdenum slabs can be sheared at room temperature; the preheating temperature for 0.5-1.2mm slabs is 65-95℃; the preheating temperature for 1.5-3.2mm slabs is 350℃; 6.3mm thick plates need to be preheated to 600℃.
Molybdenum and molybdenum alloys can be welded, that is, this method is usually used without excessive stress. The strength of the weld point and the surrounding matrix recrystallization area is extremely low, and the ductile-brittle transition temperature is much higher than the area around the weld point that is not affected by welding. The concentrated deformation potential of this weld area and the triaxial stress caused by the restriction of the base metal can lead to brittle fracture. The general welding method of molybdenum and molybdenum alloys, that is, when processed by electron beam welding, the weld and heat affected zone are small and not prone to problems. Oxygen has an adverse effect on welding and segregates at grain boundaries, thereby reducing plasticity. Therefore, arc-cast molybdenum alloys with higher carbon content are easier to weld than powder-metallurgical molybdenum alloys. Similarly, carbide-strengthened molybdenum alloys are easier to weld than pure molybdenum. Most molybdenum parts are welded in a high-purity inert gas chamber to minimize the adverse effects of oxygen. When welding materials containing volatile alloy components, bubbles (bubbles) will form in the weld. Therefore, doped molybdenum alloys are generally not easy to weld.
Paper citation information
DOI:10.13384/i.cnki.ami. 1006-2602.2000.05. 005
Vol.24 No.5
October 2000
CHINA MOLYBDENU M INDUSTRY
Stardust uses radio frequency plasma to spheroidize molybdenum powder
-high purity, low oxygen content, high sphericity, smooth surface, no satellite balls, uniform particle size distribution, excellent flow performance, high bulk density and tap density.
-Widely used in contact materials, aerospace high temperature resistant components, target materials and other fields.
-Spherical molybdenum powder is suitable for laser/electron beam additive manufacturing, laser direct deposition, hot isostatic pressing, injection molding, laser cladding and other processes.
-Customized particle size is acceptable to meet the needs of customers in different fields.
For more details, please contact Vicky +86-13318326185